5
1
9780966784305
Learning to See: Value Stream Mapping to Add Value and Eliminate MUDA / Edition 1 available in Hardcover, Other Format
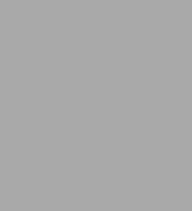
Learning to See: Value Stream Mapping to Add Value and Eliminate MUDA / Edition 1
- ISBN-10:
- 0966784308
- ISBN-13:
- 9780966784305
- Pub. Date:
- 06/01/1999
- Publisher:
- Lean Enterprise Institute, Incorporated
- ISBN-10:
- 0966784308
- ISBN-13:
- 9780966784305
- Pub. Date:
- 06/01/1999
- Publisher:
- Lean Enterprise Institute, Incorporated
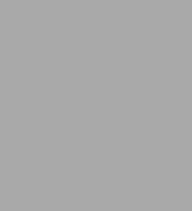
Learning to See: Value Stream Mapping to Add Value and Eliminate MUDA / Edition 1
$60.0
Current price is , Original price is $60.0. You
$60.00
Temporarily Out of Stock Online
$48.90
$60.00
Save 19%
Current price is $48.9, Original price is $60. You Save 19%.
60.0
Out Of Stock
Product Details
ISBN-13: | 9780966784305 |
---|---|
Publisher: | Lean Enterprise Institute, Incorporated |
Publication date: | 06/01/1999 |
Series: | Lean Enterprise Institute Ser. |
Edition description: | EDITION 1.2 |
Pages: | 112 |
Product dimensions: | 9.00(w) x 10.90(h) x 0.60(d) |
About the Author
From the B&N Reads Blog