Membrane Technology and Applications / Edition 2 available in Hardcover
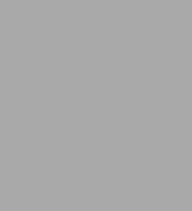
Membrane Technology and Applications / Edition 2
- ISBN-10:
- 0470854456
- ISBN-13:
- 9780470854457
- Pub. Date:
- 05/31/2004
- Publisher:
- Wiley
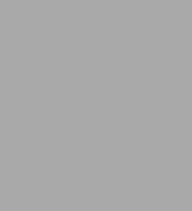
Membrane Technology and Applications / Edition 2
Hardcover
Buy New
$140.00Buy Used
$99.83-
-
SHIP THIS ITEM
Temporarily Out of Stock Online
Please check back later for updated availability.
-
Overview
Building on the success of the previous edition, Membrane Technology and Applications Third Edition provides a comprehensive overview of separation membranes, their manufacture and their applications. Beginning with a series of general chapters on membrane preparation, transport theory and concentration polarization, the book then surveys several major areas of membrane application in separate chapters. Written in a readily accessible style, each chapter covers its membrane subject thoroughly, from historical and theoretical backgrounds through to current and potential applications. Topics include reverse osmosis, ultrafiltration, pervaporation, microfiltration, gas separation and coupled and facilitated transport; chapters on electrodialysis and medical applications round out the coverage.
NEW TO THE THIRD EDITION
- New sections on the use of membranes in the chlor-alkali industry, membrane distillation, pressure retarded osmosis and constant flux-variable pressure ultrafiltration
- Zeolite and ceramic membranes, submerged membrane modules, and fuel cell membranes
- Substantially enhanced chapters on ultrafiltration, pervaporation and membrane contactors
- Updates to every chapter to reflect the developments in the field
Product Details
ISBN-13: | 9780470854457 |
---|---|
Publisher: | Wiley |
Publication date: | 05/31/2004 |
Edition description: | Older Edition |
Pages: | 552 |
Product dimensions: | 6.44(w) x 9.25(h) x 1.35(d) |
About the Author
Read an Excerpt
Membrane Technology and Applications
By Richard W. Baker
John Wiley & Sons
Copyright © 2004 John Wiley & Sons, LtdAll right reserved.
ISBN: 0-470-85445-6
Chapter One
OVERVIEW OF MEMBRANE SCIENCE AND TECHNOLOGY
Introduction
Membranes have gained an important place in chemical technology and are used in a broad range of applications. The key property that is exploited is the ability of a membrane to control the permeation rate of a chemical species through the membrane. In controlled drug delivery, the goal is to moderate the permeation rate of a drug from a reservoir to the body. In separation applications, the goal is to allow one component of a mixture to permeate the membrane freely, while hindering permeation of other components.
This book provides a general introduction to membrane science and technology. Chapters 2 to 4 cover membrane science, that is, topics that are basic to all membrane processes, such as transport mechanisms, membrane preparation, and boundary layer effects. The next six chapters cover the industrial membrane separation processes, which represent the heart of current membrane technology. Carrier facilitated transport is covered next, followed by a chapter reviewing the medical applications of membranes. The book closes with a chapter that describes various minor or yet-to-be-developed membrane processes, including membrane reactors, membrane contactors and piezodialysis.
Historical Development of Membranes
Systematic studies of membrane phenomena can be traced to the eighteenth century philosopher scientists. For example, Abbé Nolet coined the word 'osmosis' to describe permeation of water through a diaphragm in 1748. Through the nineteenth and early twentieth centuries, membranes had no industrial or commercial uses, but were used as laboratory tools to develop physical/chemical theories. For example, the measurements of solution osmotic pressure made with membranes by Traube and Pfeffer were used by van't Hoff in 1887 to develop his limit law, which explains the behavior of ideal dilute solutions; this work led directly to the van't Hoff equation. At about the same time, the concept of a perfectly selective semipermeable membrane was used by Maxwell and others in developing the kinetic theory of gases.
Early membrane investigators experimented with every type of diaphragm available to them, such as bladders of pigs, cattle or fish and sausage casings made of animal gut. Later, collodion (nitrocellulose) membranes were preferred, because they could be made reproducibly. In 1907, Bechhold devised a technique to prepare nitrocellulose membranes of graded pore size, which he determined by a bubble test. Other early workers, particularly Elford, Zsigmondy and Bachmann and Ferry improved on Bechhold's technique, and by the early 1930s microporous collodion membranes were commercially available. During the next 20 years, this early microfiltration membrane technology was expanded to other polymers, notably cellulose acetate. Membranes found their first significant application in the testing of drinking water at the end of World War II. Drinking water supplies serving large communities in Germany and elsewhere in Europe had broken down, and filters to test for water safety were needed urgently. The research effort to develop these filters, sponsored by the US Army, was later exploited by the Millipore Corporation, the first and still the largest US microfiltration membrane producer.
By 1960, the elements of modern membrane science had been developed, but membranes were used in only a few laboratory and small, specialized industrial applications. No significant membrane industry existed, and total annual sales of membranes for all industrial applications probably did not exceed US$20 million in 2003 dollars. Membranes suffered from four problems that prohibited their widespread use as a separation process: They were too unreliable, too slow, too unselective, and too expensive. Solutions to each of these problems have been developed during the last 30 years, and membrane-based separation processes are now commonplace.
The seminal discovery that transformed membrane separation from a laboratory to an industrial process was the development, in the early 1960s, of the Loeb-Sourirajan process for making defect-free, high-flux, anisotropic reverse osmosis membranes. These membranes consist of an ultrathin, selective surface film on a much thicker but much more permeable microporous support, which provides the mechanical strength. The flux of the first Loeb-Sourirajan reverse osmosis membrane was 10 times higher than that of any membrane then available and made reverse osmosis a potentially practical method of desalting water. The work of Loeb and Sourirajan, and the timely infusion of large sums of research and development dollars from the US Department of Interior, Office of Saline Water (OSW), resulted in the commercialization of reverse osmosis and was a major factor in the development of ultrafiltration and microfiltration. The development of electrodialysis was also aided by OSW funding.
Concurrently with the development of these industrial applications of membranes was the independent development of membranes for medical separation processes, in particular, the artificial kidney. W.J. Kolf had demonstrated the first successful artificial kidney in The Netherlands in 1945. It took almost 20 years to refine the technology for use on a large scale, but these developments were complete by the early 1960s. Since then, the use of membranes in artificial organs has become a major life-saving procedure. More than 800 000 people are now sustained by artificial kidneys and a further million people undergo open-heart surgery each year, a procedure made possible by development of the membrane blood oxygenator. The sales of these devices comfortably exceed the total industrial membrane separation market. Another important medical application of membranes is for controlled drug delivery systems. A key figure in this area was Alex Zaffaroni, who founded Alza, a company dedicated to developing these products in 1966. The membrane techniques developed by Alza and its competitors are widely used in the pharmaceutical industry to improve the efficiency and safety of drug delivery.
The period from 1960 to 1980 produced a significant change in the status of membrane technology. Building on the original Loeb-Sourirajan technique, other membrane formation processes, including interfacial polymerization and multilayer composite casting and coating, were developed for making high-performance membranes. Using these processes, membranes with selective layers as thin as 0.1 µm or less are now being produced by a number of companies. Methods of packaging membranes into large-membrane-area spiral-wound, hollow-fine-fiber, capillary, and plate-and-frame modules were also developed, and advances were made in improving membrane stability. By 1980, microfiltration, ultrafiltration, reverse osmosis and electrodialysis were all established processes with large plants installed worldwide.
The principal development in the 1980s was the emergence of industrial membrane gas separation processes. The first major development was the Monsanto Prism(r) membrane for hydrogen separation, introduced in 1980. Within a few years, Dow was producing systems to separate nitrogen from air, and Cynara and Separex were producing systems to separate carbon dioxide from natural gas. Gas separation technology is evolving and expanding rapidly; further substantial growth will be seen in the coming years. The final development of the 1980s was the introduction by GFT, a small German engineering company, of the first commercial pervaporation systems for dehydration of alcohol. More than 100 ethanol and isopropanol pervaporation dehydration plants have now been installed. Other pervaporation applications are at the early commercial stage.
Types of Membranes
This book is limited to synthetic membranes, excluding all biological structures, but the topic is still large enough to include a wide variety of membranes that differ in chemical and physical composition and in the way they operate. In essence, a membrane is nothing more than a discrete, thin interface that moderates the permeation of chemical species in contact with it. This interface may be molecularly homogeneous, that is, completely uniform in composition and structure, or it may be chemically or physically heterogeneous, for example, containing holes or pores of finite dimensions or consisting of some form of layered structure. A normal filter meets this definition of a membrane, but, by convention, the term filter is usually limited to structures that separate particulate suspensions larger than 1 to 10 µm. The principal types of membrane are shown schematically in Figure 1.1 and are described briefly below.
Isotropic Membranes
Microporous Membranes
A microporous membrane is very similar in structure and function to a conventional filter. It has a rigid, highly voided structure with randomly distributed, interconnected pores. However, these pores differ from those in a conventional filter by being extremely small, on the order of 0.01 to 10 µm in diameter. All particles larger than the largest pores are completely rejected by the membrane. Particles smaller than the largest pores, but larger than the smallest pores are partially rejected, according to the pore size distribution of the membrane. Particles much smaller than the smallest pores will pass through the membrane. Thus, separation of solutes by microporous membranes is mainly a function of molecular size and pore size distribution. In general, only molecules that differ considerably in size can be separated effectively by microporous membranes, for example, in ultrafiltration and microfiltration.
Nonporous, Dense Membranes
Nonporous, dense membranes consist of a dense film through which permeants are transported by diffusion under the driving force of a pressure, concentration, or electrical potential gradient. The separation of various components of a mixture is related directly to their relative transport rate within the membrane, which is determined by their diffusivity and solubility in the membrane material. Thus, nonporous, dense membranes can separate permeants of similar size if their concentration in the membrane material (that is, their solubility) differs significantly. Most gas separation, pervaporation, and reverse osmosis membranes use dense membranes to perform the separation. Usually these membranes have an anisotropic structure to improve the flux.
Electrically Charged Membranes
Electrically charged membranes can be dense or microporous, but are most commonly very finely microporous, with the pore walls carrying fixed positively or negatively charged ions. A membrane with fixed positively charged ions is referred to as an anion-exchange membrane because it binds anions in the surrounding fluid. Similarly, a membrane containing fixed negatively charged ions is called a cation-exchange membrane. Separation with charged membranes is achieved mainly by exclusion of ions of the same charge as the fixed ions of the membrane structure, and to a much lesser extent by the pore size. The separation is affected by the charge and concentration of the ions in solution. For example, monovalent ions are excluded less effectively than divalent ions and, in solutions of high ionic strength, selectivity decreases. Electrically charged membranes are used for processing electrolyte solutions in electrodialysis.
Anisotropic Membranes
The transport rate of a species through a membrane is inversely proportional to the membrane thickness. High transport rates are desirable in membrane separation processes for economic reasons; therefore, the membrane should be as thin as possible. Conventional film fabrication technology limits manufacture of mechanically strong, defect-free films to about 20 µm thickness. The development of novel membrane fabrication techniques to produce anisotropic membrane structures was one of the major breakthroughs of membrane technology during the past 30 years. Anisotropic membranes consist of an extremely thin surface layer supported on a much thicker, porous substructure. The surface layer and its substructure may be formed in a single operation or separately. In composite membranes, the layers are usually made from different polymers. The separation properties and permeation rates of the membrane are determined exclusively by the surface layer; the substructure functions as a mechanical support. The advantages of the higher fluxes provided by anisotropic membranes are so great that almost all commercial processes use such membranes.
Ceramic, Metal and Liquid Membranes
The discussion so far implies that membrane materials are organic polymers and, in fact, the vast majority of membranes used commercially are polymer-based. However, in recent years, interest in membranes formed from less conventional materials has increased. Ceramic membranes, a special class of microporous membranes, are being used in ultrafiltration and microfiltration applications for which solvent resistance and thermal stability are required. Dense metal membranes, particularly palladium membranes, are being considered for the separation of hydrogen from gas mixtures, and supported liquid films are being developed for carrier-facilitated transport processes.
Membrane Processes
Six developed and a number of developing and yet-to-be-developed industrial membrane technologies are discussed in this book. In addition, sections are included describing the use of membranes in medical applications such as the artificial kidney, blood oxygenation, and controlled drug delivery devices. The status of all of these processes is summarized in Table 1.1.
The four developed industrial membrane separation processes are microfiltration, ultrafiltration, reverse osmosis, and electrodialysis. These processes are all well established, and the market is served by a number of experienced companies.
The range of application of the three pressure-driven membrane water separation processes-reverse osmosis, ultrafiltration and microfiltration-is illustrated in Figure 1.2. Ultrafiltration (Chapter 6) and microfiltration (Chapter 7) are basically similar in that the mode of separation is molecular sieving through increasingly fine pores. Microfiltration membranes filter colloidal particles and bacteria from 0.1 to 10 µm in diameter. Ultrafiltration membranes can be used to filter dissolved macromolecules, such as proteins, from solutions. The mechanism of separation by reverse osmosis membranes is quite different. In reverse osmosis membranes (Chapter 5), the membrane pores are so small, from 3 to 5 Å in diameter, that they are within the range of thermal motion of the polymer chains that form the membrane. The accepted mechanism of transport through these membranes is called the solution-diffusion model.
Continues...
Excerpted from Membrane Technology and Applications by Richard W. Baker Copyright © 2004 by John Wiley & Sons, Ltd. Excerpted by permission.
All rights reserved. No part of this excerpt may be reproduced or reprinted without permission in writing from the publisher.
Excerpts are provided by Dial-A-Book Inc. solely for the personal use of visitors to this web site.
Table of Contents
Preface xiAcknowledgments xiii
1. Overview of Membrane Science and Technology 1
1.1 Introduction 1
1.2 Historical Development of Membranes 1
1.3 Types of Membranes 4
1.3.1 Isotropic Membranes 4
1.3.2 Anisotropic Membranes 6
1.3.3 Ceramic, Metal, and Liquid Membranes 6
1.4 Membrane Processes 6
References 13
2. Membrane Transport Theory 15
2.1 Introduction 15
2.2 The Solution-Diffusion Model 18
2.2.1 Molecular Dynamics Simulations 18
2.2.2 Concentration and Pressure Gradients in Membranes 22
2.2.3 Application of the Solution-Diffusion Model to Specific Processes 27
2.2.4 A Unified View 50
2.3 Structure-Permeability Relationships in Solution-Diffusion Membranes 53
2.3.1 Diffusion Coefficients 55
2.3.2 Sorption Coefficients in Polymers 64
2.4 Pore-Flow Membranes 72
2.4.1 Permeation in Ultrafiltration and Microfiltration Membranes 73
2.4.2 Knudsen Diffusion and Surface Diffusion in Microporous Membranes 79
2.4.3 Polymers with Intrinsic Microporosity (PIMs) 86
2.4.4 The Transition Region 89
2.5 Conclusions and Future Directions 90
References 92
3. Membranes and Modules 97
3.1 Introduction 97
3.2 Isotropic Membranes 98
3.2.1 Isotropic Nonporous Membranes 98
3.2.2 Isotropic Microporous Membranes 100
3.3 Anisotropic Membranes 102
3.3.1 Phase separation membranes 104
3.3.2 Interfacial Polymerization Membranes 121
3.3.3 Solution-Coated Composite Membranes 125
3.3.4 Other Anisotropic Membranes 128
3.3.5 Repairing Membrane Defects 132
3.4 Metal, Ceramic, Zeolite, Carbon, and Glass Membranes 134
3.4.1 Metal Membranes 134
3.4.2 Ceramic Membranes 135
3.4.3 Zeolite Membranes 139
3.4.4 Mixed-Matrix Membranes 141
3.4.5 Carbon Membranes 145
3.4.6 Microporous Glass Membranes 148
3.5 Liquid Membranes 148
3.6 Hollow Fiber Membranes 148
3.7 Membrane Modules 154
3.7.1 Plate-and-Frame Modules 155
3.7.2 Tubular Modules 157
3.7.3 Spiral-Wound Modules 158
3.7.4 Hollow Fiber Modules 162
3.7.5 Other Module Types 165
3.8 Module Selection 167
3.9 Conclusions and Future Directions 169
References 170
4. Concentration Polarization 179
4.1 Introduction 179
4.2 Boundary Layer Film Model 182
4.3 Determination of the Peclet Number 191
4.4 Concentration Polarization in Liquid Separation Processes 193
4.5 Concentration Polarization in Gas Separation Processes 196
4.6 Cross-Flow, Co-Flow, and Counter-Flow 197
4.7 Conclusions and Future Directions 204
References 205
5. Reverse Osmosis 207
5.1 Introduction and History 207
5.2 Theoretical Background 208
5.3 Membranes and Materials 213
5.3.1 Cellulosic Membranes 213
5.3.2 Noncellulosic Polymer Membranes 216
5.3.3 Interfacial Composite Membranes 217
5.3.4 Other Membrane Materials 219
5.4 Reverse Osmosis Membrane Categories 220
5.4.1 Seawater and Brackish Water Desalination Membranes 221
5.4.2 Nanofiltration Membranes 222
5.4.3 Hyperfiltration Organic Solvent Separating Membranes 224
5.5 Membrane Selectivity 227
5.6 Membrane Modules 228
5.7 Membrane Fouling Control 231
5.7.1 Scale 231
5.7.2 Silt 233
5.7.3 Biofouling 233
5.7.4 Organic Fouling 235
5.7.5 Membrane Cleaning 236
5.8 Applications 237
5.8.1 Brackish Water Desalination 238
5.8.2 Seawater Desalination 240
5.8.3 Ultrapure Water 241
5.8.4 Wastewater Treatment 242
5.8.5 Nanofiltration 244
5.8.6 Organic Solvent Separation 245
5.9 Conclusions and Future Directions 246
References 247
6. Ultrafiltration 253
6.1 Introduction and History 253
6.2 Characterization of Ultrafiltration Membranes 254
6.3 Membrane Fouling 257
6.3.1 Constant Pressure/Constant Flux Operation 257
6.3.2 Concentration Polarization 261
6.3.3 Fouling Control 271
6.4 Membranes 274
6.5 Constant Pressure Modules, System Design, and Applications 274
6.5.1 Cross-Flow Ultrafiltration Modules 275
6.5.2 Constant Pressure (Cross-Flow) System Design 278
6.5.3 Applications of Cross-Flow Membrane Modules 282
6.6 Constant Flux Modules, System Design, and Applications 292
6.6.1 Constant Flux/Variable Pressure Modules 292
6.6.2 Submerged Membrane Modules and System Design 293
6.6.3 Submerged Membrane Applications 296
6.7 Conclusions and Future Directions 299
References 300
7. Microfiltration 303
7.1 Introduction and History 303
7.2 Background 305
7.2.1 Types of Membrane 305
7.2.2 Membrane Characterization 306
7.2.3 Microfiltration Membranes and Modules 313
7.2.4 Process Design 316
7.3 Applications 320
7.3.1 Sterile Filtration of Pharmaceuticals 322
7.3.2 Sterilization of Wine and Beer 322
7.3.3 Microfiltration in the Electronics Industry 323
7.4 Conclusions and Future Directions 323
References 324
8. Gas Separation 325
8.1 Introduction and History 325
8.2 Theoretical Background 326
8.2.1 Polymer Membranes 328
8.2.2 Metal Membranes 337
8.2.3 Ceramic and Zeolite Membranes 337
8.2.4 Thermally Rearranged/Microporous Carbon Membranes 338
8.2.5 Mixed-Matrix Membranes 338
8.3 Membrane Modules 338
8.4 Process Design 339
8.4.1 Pressure Ratio 340
8.4.2 Stage-Cut 343
8.4.3 Multistep and Multistage System Designs 345
8.4.4 Recycle Designs 347
8.5 Applications 349
8.5.1 Hydrogen Separations 350
8.5.2 Oxygen/Nitrogen Separation 352
8.5.3 Natural Gas Separations 359
8.5.4 Carbon Dioxide Separation 361
8.5.5 Vapor/Gas Separations 368
8.5.6 Dehydration of Air 369
8.5.7 Carbon Dioxide/Hydrogen and Carbon Dioxide/Nitrogen Separations 370
8.5.8 Vapor/Vapor Separations 372
8.6 Conclusions and Future Directions 373
References 375
9. Pervaporation 379
9.1 Introduction and History 379
9.2 Theoretical Background 381
9.3 Membrane Materials and Modules 389
9.3.1 Membrane Materials 389
9.3.2 Dehydration Membranes 392
9.3.3 Organic/Water Separation Membranes 393
9.3.4 Organic/Organic Separation Membranes 394
9.3.5 Membrane Modules 395
9.4 System Design 398
9.5 Applications 400
9.5.1 Solvent Dehydration 401
9.5.2 Separation of Dissolved Organics from Water 406
9.5.3 Separation of Organic Mixtures 409
9.6 Conclusions and Future Directions 412
References 412
10. Ion Exchange Membrane Processes – Electrodialysis 417
10.1 Introduction/History 417
10.2 Theoretical Background 421
10.2.1 Transport through Ion Exchange Membranes 421
10.3 Chemistry of Ion Exchange Membranes 423
10.3.1 Homogeneous Membranes 425
10.3.2 Heterogeneous Membranes 426
10.4 Electrodialysis 428
10.4.1 Concentration Polarization and Limiting Current Density 428
10.4.2 Current Efficiency and Power Consumption 433
10.4.3 System Design 435
10.5 Electrodialysis Applications 438
10.5.1 Brackish Water Desalination 438
10.5.2 Salt Recovery from Seawater 438
10.5.3 Other Electrodialysis Separation Applications 440
10.5.4 Continuous Electrodeionization and Ultrapure Water 442
10.5.5 Bipolar Membranes 443
10.6 Fuel Cells 444
10.7 Membranes in Chlor-Alkali Processes 448
10.8 Conclusions and Future Directions 449
References 449
11. Carrier Facilitated Transport 453
11.1 Introduction/History 453
11.2 Coupled Transport 459
11.2.1 Background 459
11.2.2 Characteristics of Coupled Transport Membranes 463
11.2.3 Coupled Transport Membranes 468
11.2.4 Applications 472
11.3 Facilitated Transport 473
11.3.1 Background 473
11.3.2 Process Designs 476
11.3.3 Applications 481
11.4 Conclusions and Future Directions 486
References 487
12. Medical Applications of Membranes 493
12.1 Introduction 493
12.2 Hemodialysis 493
12.3 Blood Oxygenators 498
12.4 Plasma Fractionation 500
12.5 Controlled Drug Delivery 501
12.5.1 Membrane Diffusion-Controlled Systems 502
12.5.2 Biodegradable Systems 510
12.5.3 Osmotic Systems 512
References 518
13. Other Membrane Processes 521
13.1 Introduction 521
13.2 Dialysis 521
13.3 Donnan Dialysis (Diffusion Dialysis) 522
13.4 Charge Mosaic Membranes and Piezodialysis 526
13.5 Membrane Contactors and Membrane Distillation 529
13.5.1 Applications of Membrane Contactors 532
13.6 Membrane Reactors 538
13.6.1 Applications of Membrane Reactors 541
13.7 Ion-Conducting Membrane Reactors 544
13.8 Pressure-Retarded Osmosis (PRO) and Reverse Electrodialysis (RED) 547
13.9 Chiral Drug Separation 551
13.10 Conclusions and Future Directions 552
References 553
Appendix 559
Index 571