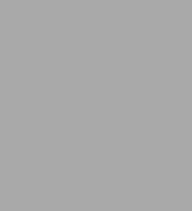
Development of a New Material: Monolithic Ti4O7 Ebonex Ceramic
113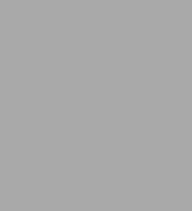
Development of a New Material: Monolithic Ti4O7 Ebonex Ceramic
113Paperback
-
PICK UP IN STORECheck Availability at Nearby Stores
Available within 2 business hours
Related collections and offers
Overview
Product Details
ISBN-13: | 9780854049844 |
---|---|
Publisher: | RSC |
Publication date: | 02/16/2001 |
Pages: | 113 |
Product dimensions: | 6.15(w) x 9.20(h) x (d) |
Read an Excerpt
Development of a New Material â" Monolithic Ti4 07 Ebonex Ceramic
By P C S Hayfield
The Royal Society of Chemistry
Copyright © 2002 MFIS LtdAll rights reserved.
ISBN: 978-0-85404-984-4
CHAPTER 1
Towards an Electrically Conductive Ceramic
1.1 INTRODUCTION
It may on first consideration seem implausible that monolithic titanium dioxide ceramic, well-known as an electrical insulator/dielectric material, could ever be transformed into an electrically conductive material, with a potential application as a commercial electrode to rank alongside existing materials such as graphite, magnetite, silicon iron and the family of noble metal/oxide-coated titanium anodes. Yet this is now the case, and what follows is a first-hand account of its inception in an industrial metallurgical laboratory, and the successes and failures, as those involved, guided largely by intuition, backed with empirical trials, felt their way towards a useful and totally novel material.
The work described, was carried out in the Central Research & Development Laboratories of Messrs IMI plc, at Witton, Birmingham, and began in 1981. As it became apparent that a novel, electrically conductive and relatively corrosion-resistant material was within reach, there were some who felt it might provide an alternative substrate to titanium as a basis for precious metal (or oxide) coated electrodes to be used in aggressive electrolytes, such as the strong sulphuric acid used in many metal electro winning processes. However the commercial incentive for change from the widely-used lead-silver alloy anodes was weak, and it seemed to some, too big a step to introduce a brittle ceramic into an industry where large and robust components were handled with abandon .. Others contemplated an opportunity for the electrode material in reversing-polarity swimming pool electrochlorinators, a vast market. Yet others, from a manufacturing background, perceived improved methods of manufacture, leading to a much wider range of possible applications, including lower weight lead-acid-type batteries than hitherto possible. These and other applications are discussed below.
The material, for which the registered Trademark "Ebonex", was secured, because of its lustrous dark grey or black appearance, has been commercially available for some years now, and has been used in a range of applications, principally cathodic protection (Fig 1-1). Originally registered to Messrs Marston Palmer Ltd (a wholly-owned subsidiary of IMI Ltd), the Trademark is now the property of Messrs Atraverda Ltd, and covers a range of electrically-conducting sub-oxides of titanium. Many other applications remain to be explored. Some are contingent on further improvement in manufacturing technique, while others, as is so often the case, have to surmount the barrier posed by existing investment in long-established plant and processes. Significant capital investment is called for before new markets can be addressed and such ventures are not without risk.
1.2 THE PATH TO A NEW MATERIAL
A description of the events leading up to the identification of Ti4 O7, as an electrically conductive ceramic and a possible electrode material here begins with a series of paragraphs that might seem disjointed and non-sequitur, but which – taken together – describe how the concept of the all-titanium oxide electrode came about.
The 1970's and 1980's were a time when many of the graphite-based anodes used in the chlor-alkali industry (including production of chlorine, chlorate and hypochlorite) were replaced by low overpotential, noble metal oxide-type, coated titanium electrodes. The incentives for phasing out graphite anodes were powerful. Most chlor-alkali processes are operated at high current density meaning that quite small savings in cell voltage (typically 0.3V or so) result in substantial long-term energy savings. So rapid and rewarding was the introduction of the new coated anodes that, over and above electrode re-coating/replacement market, the electrode industry set its sights on related markets, that is on the introduction of titanium based electrodes in other processes, notably electrowinning of metals, where huge quantities of electricity were used. The anode manufacturers were confident that in these industries too, impressive cost-savings could be won. The most obvious target industries were those involved in metal winning, principally zinc, copper and manganese.
Electrowinning is, for the most part, carried out at much lower current densities than those used in chlor-alkali manufacture, and to this extent, energy savings might be expected to be smaller. The electrolyte used, however is usually strong sulphuric acid, often containing significant concentrations of hydrofluoric acid. While titanium can broadly be considered to be highly corrosion-resistant to most chlor-alkali electrolytes, the same is not true in strong sulphuric acid, even when anodically polarized. The presence of hydrofluoric acid in these electrolytes further increases corrosion rates. The result of such attack is a tendency to undermine the applied noble metal oxide electrocatalyst coatings, thereby shortening the electrode life.
The substrate attack described above, posed a dilemma for those seeking to move into these huge new markets by developing replacement anodes for the lead-silver alloys widely used in electrowinning. (For completeness, it should be noted that there have been extensive studies of other binary, ternary and quaternary lead-based alloys to replace the conventional lead silver. Some did show an apparent superiority, but for various reasons do not appear to have been widely introduced on an industrial scale). The obvious approach was to deposit coatings which would be so impervious to electrolyte as effectively to hide the substrate titanium for most of the electrode useable life. Another approach related to the use of titanium intermetallics. It had previously been noted, in pickling-off the copper used as a lubricant in certain titanium processing eg. in wire-drawing where an intermetallic forms between titanium and copper, that the last vestiges of copper were difficult to remove. When an electrochemical method using sulphuric acid electrolyte was tried, it was observed that, when the surface was anodically polarised, oxygen evolution occurred in preference to copper dissolution. The balance between the two reactions was about 98 to 2. Such intermetallics were never seriously considered as a coating for titanium substrates. However, lumps of titanium-copper intermetallic contained within a titanium mesh anode basket seemed to work satisfactorily, and these and other possibilities for titanium intermetallic-type anodes were extensively examined.
It was during the testing of such copper-titanium intermetallics that it was observed particles became covered with a titanium oxide film. This could simply have been a consequence of the selective dissolution of copper. However, a view at the time, later shown to be erroneous, was that perhaps the titanium oxide film could be controlling the rate of copper dissolution. Whether logical or not, could a form of titanium oxide be made into an electrode its own right?
As chance would have it, the company in which the above work was being progressed, had once owned a ceramics manufacturing facility. Their product range included titanium dioxide, usually in the form of tube, used as a dielectric for manufacture of capacitors. Over the years another use of this material had developed, stemming from its toughness, which allowed its use as a thread guide in the textile industry. Continuous rubbing of thread leads to build up of static electricity which in turn attracts 'dirt' which can then cause damage to the thread. Over the years it had been found that build-up of static could be diminished or eliminated by introducing a measure of electrical conduction into surface layers. This was achieved by heating the vitrified products in hydrogen at about 600°C for a few hours. The treatment caused the titanium dioxide ceramic to darken or go a blue-black, a process know as 'blueing'. As it happened, in connection with an earlier investigation into the metallising of plastics., two rods of such 'blued' titania were to hand, approx. 10mm diameter x 120mm long.
With hindsight, and given the perceived importance at the time, of developing possible alternative anodes to replace lead-silver in electrowinning, in particular of zinc, it might have seemed logical to test the 'blued' titania rods in a simulated zinc winning electrolyte. But as it happened, a simulated manganese winning solution was readily available, based on sulphuric acid and operated at the unusually high temperature of ca. 95°C. Thus it was that the 'blued' rods were tested as anodes in this electrolyte, and in the short term at least, appeared to pass current satisfactory. So, for the first time, the concept of a monolithic titanium sub-oxide electrode was demonstrated.
The concept of such an electrode could easily have been overlooked, had it not been for a succession of fortunate events. First there was the felicitous (albeit erroneous) conception of an outer film, forming on anodically polarized titanium-copper intermetallic, which displayed semiconducting behaviour, thereby providing a rate controlling effect on the anodic processes occurring at the surface. Secondly was the ready availability of some of the 'blued' titania rods; and finally there was to hand a supply of manganese electrowinning electrolyte. As was later appreciated, the manganese-winning electrolyte is much more favourable to the operation of such anodes than, for example, zinc-winning electrolytes, allowing even uncoated titanium to function satisfactorily. Had zinc-winning electrolytes been used, as might so easily have been the case, less encouraging results could have led to the project being abandoned. It was widely accepted that the IMI Research and Development Department had been wisely organised in such a way as to encourage lateral thinking. But even so, the path from initial concept to eventual commercialisation of a product and identification of appropriate markets, was to take another 20 years and to involve costs of many millions of pounds.
1.3 INITIAL PRODUCTION OF TEST MATERIAL
It was recognised at the time that the electrical conductivity of the "blued" titania was only superficial. On fracturing, the bulk of the ceramic is creamy white in colour, as is its 'non blued' precursor. It was loosely thought that the outer layer was some form of non-stoicheometric rutile , referred to as TiOx where "x" was not known. (Full details of the titanium – oxygen equilibrium diagram had not been established at that time). Most of those working on the project had no knowledge of oxide phases, either by name, such as "Magneli" or "Wadsley" or by their stoicheometry, such as Ti4O7
To explore further the possibilities of a modified titanium dioxide ceramic as an electrode, it was necessary to establish a supply source, for experimentation and trials. Mainstream ceramic manufacturers were not interested in supplying such small quantities. The alternative was to identify stockists who might be prepared to do so. From such stockists, a few tubes were procured, all approximately 10mm OD x 100 mm long.
Within the Research & Development Department, equipment was available for the heat treatment of metals and alloys in non-oxidising atmospheres, including hydrogen. The commercially procured tubes were therefore heated in hydrogen at ca. 1000°C for a few hours. The 'blued' tubes which emerged, were darkened not only superficially, but throughout the bulk of the ceramic. The ceramic had become integrally electrically conductive, though with a conductivity still far short of that characteristic of most metals.
Coated with an established noble metal/oxide electrocatalyst, Pt + Ir0x by a paint/thermal decomposition route (described below), the tubes were anodically polarised in simulated zinc winning electrolyte (165 gm/litre sulphuric and +115 ppm chloride + 5 ppm fluoride). Most gave good performance, some for up to a year when, for commercial reasons, the project was halted.
In other work, an uncoated 'blued' tube was made an anode in saturated brine at ambient temperature, in order to observe its current carrying capacity. Almost immediately after switch-on, and to the amazement of the onlookers, the 'blued' material visibly disintegrated, with a pile of fine black powder forming on the floor of the tank, directly underneath. This powder was later identified as titanium oxide, and in subsequent spectrographic analysis, the starting electrode was found to have contained significant quantities of aluminium.
With hindsight, the incredulity of those involved in the experiment, that alumina was present in a nominally all-titania tube, might seem naive. The truth was that these were largely metallurgists either by training or experience, and with little knowledge of either the theory or industrial practices in the ceramics industry. Clearly, there was an urgent need to learn in some detail, what was involved in the manufacture of ceramics. Thus it was appreciated that much difficulty attends the vitrification of high melting point ceramic particles. In many instances, and this includes the manufacture of titania, a low melting point vitrifying agent is added, effectively to glue together the high melting point particles. These are sometimes known as "sintering aids". In the case of titania, such agents include clays and tungsten oxide. Such clays (for example bentonite) contain aluminium. Vitrifying agents are routinely added, whether the end use is as a dielectric material or as threadguides. Of the handful of titania tubes acquired from a stockist, half contained several percent of aluminium, and the others tungsten (both in the form of their oxides).
Asked to supply titania tubes without sintering aids, manufacturers warned that it would be difficult to ensure a dense product. They also asked what purity was required for an electrode-grade ceramic. Not really knowing how to answer at that stage, it seemed reasonable to specify impurity levels similar to those set for commercial grade titanium to ASTM Grade I. In this specification, aluminium, iron and several other impurities must each not exceed 0.05 wt%. Achieving such low levels proved far from simple. Most ceramic manufacturers offering titania, are primarily alumina producers. Furthermore, most of the equipment used in powder processing or handling is ferrous-based. Impurity levels found in initially used samples from manufacturers are listed in Table 1-1.
Many more lessons in the technology of ceramics manufacture were learned through hard experience, mainly those related to the processing of the precursor powders into vitrified ceramics. It is essential, in carrying out this transformation, to ensure a predictable shrinkage rate on vitrification. Unless this is the case, components cannot be manufactured to any reasonable dimensional tolerances. In essence, this implies production of a starting powder, ('the green mix'), in which the packing of powder particles prior to vitrification, is reproducible. It may be necessary to mix several raw materials which are usually milled, sometimes for hours or even days, in order to achieve a reproducible shrinkage rate. At some point in the processing a wax-like organic binder is added to provide mechanical strength when the product is shaped (the green state) prior to vitrification. It is also normal, once the product is shaped, to burn out this organic binder prior to vitrification.
(Continues...)
Excerpted from Development of a New Material â" Monolithic Ti4 07 Ebonex Ceramic by P C S Hayfield. Copyright © 2002 MFIS Ltd. Excerpted by permission of The Royal Society of Chemistry.
All rights reserved. No part of this excerpt may be reproduced or reprinted without permission in writing from the publisher.
Excerpts are provided by Dial-A-Book Inc. solely for the personal use of visitors to this web site.