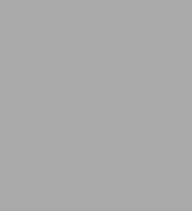
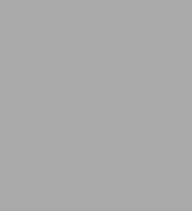
Hardcover
-
SHIP THIS ITEMIn stock. Ships in 1-2 days.PICK UP IN STORE
Your local store may have stock of this item.
Available within 2 business hours
Related collections and offers
Overview
Product Details
ISBN-13: | 9780854046133 |
---|---|
Publisher: | RSC |
Publication date: | 08/06/2003 |
Series: | Special Publications , #290 |
Pages: | 96 |
Product dimensions: | 6.15(w) x 9.20(h) x 0.30(d) |
Read an Excerpt
Additives in Water-borne Coatings
By Gerry Davison, Bruce Lane
The Royal Society of Chemistry
Copyright © 2003 The Royal Society of ChemistryAll rights reserved.
ISBN: 978-0-85404-613-3
CHAPTER 1
ADDITIVES IN COATINGS - A NECESSARY EVIL?
Roger F G Brown
Pigment Dispersion Group, Technology Centre Decorative Coatings Akzo Nobel Decorative Coatings PO Box 37, Crown House Hollins Road, Darwen, Lancashire, BB3 0BG, UK.
1 INTRODUCTION
It is generally accepted that surface coatings are applied to decorate and protect (paints and lacquers) or to inform (paints and inks). Coatings in their simplest form as a dried film on the substrate consist of binder (lacquers) or binder and pigment (lacquers, paints and inks). Additionally, it is necessary for the paint to be applied to the substrate. With the exception of some curable liquid formulations (e.g. radiation cured, liquid two pack paints, etc.) some form of diluent is required to enable the coating to be applied. In the majority of cases, this diluent is some kind of liquid volatile material (organic or aqueous) though in the case of powder coatings the diluent enabling application is air. Hence, to generalise, liquid paint, in its simplest form, will consist of pigment, binder and diluent. In this simplified formulation, the only variables are pigment volume concentration (PVC) and solids content (SC) and it is straightforward to record any given measurable property of the wet or dry paint as a function of the composition.
An optimised formulation with the best balance of properties can then be readily determined. Unfortunately, in the vast majority of, if not all cases, this optimised balance point is deficient in a number of key areas and, in some areas, the required level of performance simply cannot be achieved in such a simplified formulation. This is where additives play a part. By selective use of additives, it is possible to achieve better properties in specific performance attributes that cannot be achieved with the simplified tertiary formulation. Additionally, it becomes possible to achieve an enhanced balance of properties, where some properties can be improved without the same degree of detrimental effect on other properties. Additives are used in coatings for a great number of purposes to improve specific properties throughout the lifecycle of a paint such as processing properties in manufacture, in-can stability, application properties, drying properties and final film performance. Unfortunately, each extra additive adds a degree of complexity to the formulation and achieving the optimum balance point between varying (often opposed) properties. Hence, from the paint developer's point of view, a minimalist approach to formulation is to be preferred. Nevertheless, because it is generally impossible to achieve the desired properties without additives, this increase in formulation complexity is justifiable and wholly necessary. With VOC legislation stimulating the development of alternative technologies such as waterborne, high solids, radcure and powder, the need for additives will not go away. If anything, with waterborne technologies supplanting solventborne in a number of sectors, it can be argued that the importance of additives is increasing due to the added complexity of formulating in water.
2 LEGISLATION
It is not intended to provide a comprehensive list of legislation relevant to the coatings industry. However, within the European market, a number of legislative acts have been passed with many subsequent amendments and adaptations to technical process which have great significance for the Coatings industry. A number of important Directives are presented in Table 1. These have profound implications for the formulator in terms of labelling, inclusion of specific products and the levels at which specific products may be used. Furthermore, there are a number of voluntary labelling initiatives within the Deco sector such as Ecolabel, Blue Angel and the Globe. Additional to this, there are also sector specific directives currently under consultation, such as the Deco Directive on VOC's, which will further add to the framework within which the formulator must work. In many cases, it is this framework which drives product development but also the conversion from one type of technology to another. Environmental issues, both legislative and voluntary, will continue to drive additive development and paint development simultaneously for a long time to come.
3 THE NEED FOR ADDITIVES
As already discussed in the introduction, additives are frequently essential to obtain properties that cannot be obtained from the simple combination of pigment, binder and diluent. Additives are multifarious in nature and are used to control a number of different properties. A list of properties that may be controlled by selective use of additives, by no means exhaustive, is presented in Table 2, along with examples of the chemical nature of such materials. Paint formulation is a balancing act. This is because paint is expected to fulfil a number of key requirements, which will vary, dependent on the application. To maximise profitability, paints should be cheap to manufacture both in terms of raw material costs but also ease of production with high throughput, low energy processes preferred. Technically, paints must have good in-can stability so that there is no separation of ingredients or colour. Paints are required to have good application properties, specifically associated with rheology, whether for brush application, spray application, dip coating, coil coating, etc. dependent on the sector. The paint should dry well with respect to coalescence or cure. Finally, the final paint should adhere well to the substrate, have the correct colour and level of gloss, show good retention of colour and gloss and have the desired protective properties, ideally for as long possible. Hence, there are a great number of properties that a paint is expected to have, some of which are specifically opposed (e.g. sag resistance vs. levelling) and there is no such thing as the perfect paint. It is obvious that a balance must be struck between opposed properties. One of the key requirements when formulating a paint is to establish what balance of properties should be achieved. Within this, tacit acceptance must be made that the perfect paint does not exist and that the paint may not be able to match all desired properties. In establishing the desired balance, the most important properties for the specific application must be defined so that, where a trade between properties is required, the relative weighting given to gains and losses reflects their relative importance. Less obvious to non formulator's, is that non opposed properties also need to be balanced because each additive, as well as affecting desired properties, coincidentally will usually have knock-on effects, often unexpected, on other properties. For example, drying agents added to a paint to improve curing properties may migrate to the surface of the film and have a detrimental effect on gloss and or gloss retention. However, this is where the skill of the formulator comes to the fore, and paint companies are able to differentiate their own products in terms of the performance balance achieved for a specified price. The type and quantity of each additive used must be carefully selected, based on experience, and optimised, based on well designed experiments, to achieve the best balance of properties, taking into account the relative importance of each property. Hence, whilst formulation is easier with fewer components, the increasing complexity of including multiple additives allows each paint manufacturer the chance to make their products distinguishable in the market. However, when increasing the number of additives used, care should be taken that particular combinations are not antagonistic. The ideal situation, obviously, is where synergy is achieved within the additive cocktail used.
4 WATERBORNE VS. SOLVENTBORNE – INCREASING THE NEED FOR ADDITIVES
There are a number of fundamental differences between solventborne and waterborne paints. When comparing, for example, a latex trim paint with its solventborne counterpart, there are a number of features that have been taken into account when developing the two formulations. Firstly, the high surface tension of water must be considered. This makes pigments more difficult to wet and stabilise and makes substrate wetting more difficult and generates a requirement for the use of surface active additives to help overcome this. Secondly, the disperse nature of the binder should be considered. This has direct effects in that surface active material is usually needed to stabilise the binder but also has indirect effects such as rapid increase in viscosity with increasing solids content and the need for phase inversion and colalescence during the film formation stage. There is a further complication with increased crowding in a latex system but this is considered outside the scope of this paper.
In a dispersion (waterborne) paint, viscosity is generally very low (reflecting the viscosity of the medium) below a volume fraction of particles of 40% whilst it goes up increasingly rapidly above this value. Additionally, because the binder is not soluble in the medium, once the binder particles come into contact, the film cannot be spread further by working in extra medium. This leads to a generalised phenomenon in waterborne paints whereby open time is short. Because the viscosity can increase very rapidly with increase in solids content due to evaporation of a small amount of water, becoming irreversible at a certain point, it is necessary to formulate at sufficiently low volume solids to obtain satisfactory open time. Formulating at low volume solids leads to paints of low viscosity and thickening agents are required to give adequate in-can viscosity and film build (body) to the paint.
By comparison, in a solution (solventborne) paint, the viscosity increases in a much more controlled manner as the volume solids increases during solvent evaporation and it is also possible to work extra solvent into the existing film to thin the paint back during application. Hence, it is possible to formulate with good in-can viscosity and film build, whilst still retaining sufficient open time, levelling and flow, without the need for specific thickening agents.
Also, when comparing dispersion and solution coatings, in the latter, the binder is already part of the continuous phase in the wet paint whilst in the former, the binder is dispersed in the continuous phase. Hence, for a solution coating, the continuous phase becomes gradually more concentrated during drying until all of the solvent has evaporated. Conversely, for a dispersion coating, there is a point of phase inversion where the binder particles touch and deform and change from being part of the dispersed phase to being the continuous phase. Following this phase inversion, to develop film integrity, it is important that the binder particles deform and coalesce to fill the voids left by the still evaporating medium and coalescing solvents are frequently needed to assist in this. Hence, it can be seen that many properties that can be taken for granted with solventborne paints must be specifically provided through use of additives in waterborne paints.
To summarise the comparison between alkyd trim paints and their Waterborne counterparts, a lot of properties are provided by solventborne alkyd technology for which specific additives are required in waterborne dispersion paints. Frequently, the polar alkyd resins are capable of wetting and stabilising the pigment for which dispersing agents are needed in waterborne.
Additionally, during drying, solventborne alkyd paints have tendency to spontaneously stratify to yield a thin resin rich layer at the air interface. This gives high gloss, further reducing the need for specific wetting and dispersing additives to improve the degree of dispersion of the pigment, necessary in waterborne paints to achieve high gloss. The relationship between volume solids and viscosity is frequently such with alkyd paints that good in-can viscosity and film build can be obtained at the same time as good open time, levelling and flow, without the need for specific thickening agents, as needed in waterborne. The fact that the resin is already present as a constituent in the continuous phase in solventborne paints alleviates the need for coalescing solvents which are frequently needed to promote development of film integrity in waterborne paints following phase inversion. Finally, because of the aqueous environment, there is generally a need for biocidal additives in waterborne paints, which are frequently not required in solventborne paints. Therefore, it can be seen that changing from solventborne to waterborne technology is likely to entail an increase in the requirement to include additives in the formulation.
5 SUMMARY
From a simplistic point of view, the formulator's job is easiest with the minimum number of paint ingredients. A response surface can be easily constructed for a four component system by use of an equal dimensioned tetrahedron.
This would allow for the ratio of pigment, binder, diluent and a single additive/performance modifier to be easily optimised. Provided that the correct weighting is assigned to each measurable property, commensurate with its importance, the best balance of performance is readily achievable. However, because of the simplicity of achieving this, it would be extremely difficult for individual paint manufacturers to differentiate their products in the market unless they have proprietary materials available with superior performance. Fortunately/unfortunately (dependent on the viewpoint) paint formulation is not this simple and it is generally not possible to achieve a satisfactory balance of properties without a multi-component formulation containing a range of different additives. This is where the skill and experience of the paint formulator to maximise synergy and minimise antagonism allows products to be differentiated in the market. Hence, additives in coatings are an integral and necessary part of paint formulation to give enhanced performance. With environmental concerns driving formulation development and a gradual move from conventional solventborne technology to technologies with reduced environmental impact, the need for additives in coatings is set to increase. Although inclusion of a number of different additives increases the complexity of the formulation, additives are fundamental in improving the balance of performance and providing market opportunities – truly a necessary evil.
CHAPTER 2BIOCIDE REVIEW
Scott Betts
1 INTRODUCTION
A wide range of water based products, including paints, polymer emulsions, building products and the like are usually susceptible to attack by a number of different microorganisms. Such attacks can result in severe economic loss and it is, therefore vital to institute measures that will prevent this from happening. The use of Biocides has been extremely important to thwart economic damage caused to paints and other industrial products. Microbial damage in coatings can be categorised into two types: In-can Damage and Dry Film Damage.
2 IN-CAN DAMAGE: INFECTION OF INDUSTRIAL PRODUCTS IN THE WET-STATE
If a coating is not protected with the right biocide, microbial damage could occur. Damage to paints or other systems can manifest itself in a number of different ways.
Firstly, there is the possibility that visible surface microbiological growth could occur. Here the surface of the product is visibly fouled. Fungal growth can be seen as usually green, black or off-white growths on the surface. Occasionally pools of bacterial colonies are seen. These appear as off-coloured product spots on the surface.
Secondly, damage can been as product separation. Coatings contain varying amounts of solids depending on its function. To keep these solids suspended in a water medium, other additives such as cellulosic thickeners and LAS surfactants are used. These components can be attacked by microorganisms and can be broken down. As this happens, their ability to function properly diminishes and the solid matter of the formulation settles to the bottom of the container.
Thirdly, depending on the type of microbial infection, gas production is known to occur. Gases such as carbon dioxide are generated as the result of microbial activity. As gas is produced, pressure can build up in the package causing swelling. In rare cases, the pressure has been sufficient to cause the lids of the container to buckle and is forced off the container. Other gases such as hydrogen sulphide can be given off if anaerobic bacteria infect the product. In this case the odour of "rotten eggs" is perceptible.
Fourthly, microbial infections can produce unpleasant odours as microbial by-products build up. Production of hydrogen sulphide (as described above) and various organic acids can result providing the noticeable odours.
Other problems of product discoloration, pH drift, loss of viscosity, loss of performance can also result from products contaminated with microorganisms. No matter how the infection manifests itself, the consumer does not want to purchase a product that has the above issues.
Many different species of microorganisms have been responsible for paints spoiling. Recently, it has been observed that the most prevalent species are from the Pseudomonas, Burkholderia, and Glucanacetobacter genera.
(Continues...)
Excerpted from Additives in Water-borne Coatings by Gerry Davison, Bruce Lane. Copyright © 2003 The Royal Society of Chemistry. Excerpted by permission of The Royal Society of Chemistry.
All rights reserved. No part of this excerpt may be reproduced or reprinted without permission in writing from the publisher.
Excerpts are provided by Dial-A-Book Inc. solely for the personal use of visitors to this web site.
Table of Contents
Additives in Coatings - A Necessary Evil?; Biocide Review; Cellulose Ether Thickeners - Key Elements for Complete Rheology Solutions; Water Based Dispersants - The High Performance Challenge; Additive Rules: The Classification and Selection of Additives for Coatings; Practical Aspects of Formulating with Associative Thickeners; Matting Agents for the Millennium; Antifoams; Silicone Surface Active Agents; Subject Index