Having edited "Journal of Materials Processing Technology" (previously entitled "Journal of Mechanical Working Technology") for close on 25 years, I have seen the many dramatic changes that have occurred in the materials processing field. Long gone are the days when the only "materials processing" carried out was virtually the forming of conventional metals and alloys, and when the development of a new product or process in a great number of cases called for several months of repetitive trial-and-error,' with many (mostly intuition- or experience-based) expensive and time-consuming modifications being made to the dies, until success was achieved. Even when a 'successful' product was formed, its mechanical properties, in terms of springback and dimensional accuracy, thickness variations, residual stresses, surface finish, etc. , remained to be determined. Bulk-forming operations usually required expensive machining to be carried out on the product to impart the required dimensional accuracy and surface fmish. Over the years, the experience-based craft of metal forming has given way to the science of materials processing. With the use of the computer, forming operations can be simulated with accuracy, to determine the best forming route and the associated forming loads and die stresses, and to predict the mechanical properties of the formed product, even down to its surface texture.
1020666207
Computer Applications in Near Net-Shape Operations
Having edited "Journal of Materials Processing Technology" (previously entitled "Journal of Mechanical Working Technology") for close on 25 years, I have seen the many dramatic changes that have occurred in the materials processing field. Long gone are the days when the only "materials processing" carried out was virtually the forming of conventional metals and alloys, and when the development of a new product or process in a great number of cases called for several months of repetitive trial-and-error,' with many (mostly intuition- or experience-based) expensive and time-consuming modifications being made to the dies, until success was achieved. Even when a 'successful' product was formed, its mechanical properties, in terms of springback and dimensional accuracy, thickness variations, residual stresses, surface finish, etc. , remained to be determined. Bulk-forming operations usually required expensive machining to be carried out on the product to impart the required dimensional accuracy and surface fmish. Over the years, the experience-based craft of metal forming has given way to the science of materials processing. With the use of the computer, forming operations can be simulated with accuracy, to determine the best forming route and the associated forming loads and die stresses, and to predict the mechanical properties of the formed product, even down to its surface texture.
54.99
In Stock
5
1
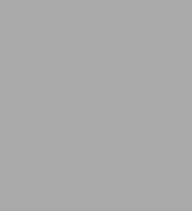
Computer Applications in Near Net-Shape Operations
322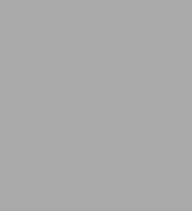
Computer Applications in Near Net-Shape Operations
322Paperback(Softcover reprint of the original 1st ed. 1999)
$54.99
54.99
In Stock
Product Details
ISBN-13: | 9781447111597 |
---|---|
Publisher: | Springer London |
Publication date: | 10/13/2012 |
Series: | Advanced Manufacturing |
Edition description: | Softcover reprint of the original 1st ed. 1999 |
Pages: | 322 |
Product dimensions: | 6.10(w) x 9.25(h) x 0.03(d) |
From the B&N Reads Blog