- Helps you reduce your liability by showing why building envelopes fail and how they can be designed to endure.
- Moves from theory to actual construction by including hundreds of building envelope details from a broad array of projects and climates.
- Integrates numerous contemporary case studies, including Frank Gehry's Experiential Music Center in Seattle (thin skins), Renzo Piano's Rue de Meaux housing in Paris (terra cotta cladding), and Mario Botta's San Francisco Museum of Modern Art (prefabricated brick panels).
Designing the Exterior Wall is a must-have book, whether you're an architect or a student. Order your copy today.
- Helps you reduce your liability by showing why building envelopes fail and how they can be designed to endure.
- Moves from theory to actual construction by including hundreds of building envelope details from a broad array of projects and climates.
- Integrates numerous contemporary case studies, including Frank Gehry's Experiential Music Center in Seattle (thin skins), Renzo Piano's Rue de Meaux housing in Paris (terra cotta cladding), and Mario Botta's San Francisco Museum of Modern Art (prefabricated brick panels).
Designing the Exterior Wall is a must-have book, whether you're an architect or a student. Order your copy today.
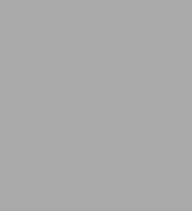
Designing the Exterior Wall: An Architectural Guide to the Vertical Envelope
400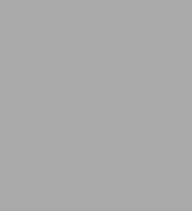
Designing the Exterior Wall: An Architectural Guide to the Vertical Envelope
400Hardcover
-
SHIP THIS ITEMIn stock. Ships in 6-10 days.PICK UP IN STORE
Your local store may have stock of this item.
Available within 2 business hours
Related collections and offers
Overview
- Helps you reduce your liability by showing why building envelopes fail and how they can be designed to endure.
- Moves from theory to actual construction by including hundreds of building envelope details from a broad array of projects and climates.
- Integrates numerous contemporary case studies, including Frank Gehry's Experiential Music Center in Seattle (thin skins), Renzo Piano's Rue de Meaux housing in Paris (terra cotta cladding), and Mario Botta's San Francisco Museum of Modern Art (prefabricated brick panels).
Designing the Exterior Wall is a must-have book, whether you're an architect or a student. Order your copy today.
Product Details
ISBN-13: | 9780471451914 |
---|---|
Publisher: | Wiley |
Publication date: | 06/20/2005 |
Pages: | 400 |
Product dimensions: | 8.60(w) x 11.10(h) x 1.30(d) |
About the Author
Read an Excerpt
Designing the Exterior Wall
By Linda Brock
John Wiley & Sons
ISBN: 0-471-45191-6Chapter One
Water Barriers and Flashings
2.1 MANAGING WATER
Water deteriorates materials-it rots wood, oxidizes metals, and provides a growth medium for mold and mildew. Wet components such as fiberglass batt insulation do not function as well. Water causes swelling or expansion of some materials and can transport pollutants and dissolved substances such as the salts that cause efflorescence. Continual freezing and thawing of wet materials adds additional forces-water increases 4 percent in volume when it freezes. Corrosion of steel also produces forces, as the iron oxide takes up more volume than the steel it replaced. In the worst case, water ingress may threaten life safety, as when the steel anchoring system of a cladding begins to corrode.
Water can enter a wall from rain or snow or ice melt. Improperly adjusted sprinkler heads that direct water to the exterior wall and poorly functioning or designed gutter systems and scuppers are other sources of water entry. The form or articulation of the vertical envelope can help or hinder the control of the water flow down the face of the exterior wall. Air pressure differentials and capillary suction across the wall can draw water through the wall. Condensation of vapor from interior or exterior sources produces water. Wet construction applications-such as pouring concrete floor toppings, dry-walling, and some sprayed-on insulation such as cellulose-add moisture to a wall. Water may enter wall components during manufacturing, transporting, or storing of the materials. Using gas heaters during construction adds moisture to the interior. Stopping water is critical. As noted in "ASTM Practices for Increased Durability of Building Constructions Against Water-Induced Damage" (E241), "except for structural errors, about 90% of all building construction problems are associated with water in some way."
2.2 WATER MANAGEMENT SYSTEMS
Moisture trapped in the wall during construction can be limited with the active onsite involvement of the architect, especially when backed by carefully written specifications and detailed drawings. Air barrier systems, thermal insulation, and vapor retarders all play a role in controlling condensation of water vapor in a wall. Water management systems prevent the entry of water from the exterior.
The four basic systems used to manage water are:
face-sealed barrier walls internal drainage plane walls drainage cavity walls pressure-equalized rain-screen walls
They are described below in order of their relative cost and effectiveness. With cladding materials such as metal, which is watertight, the management of water ingress occurs at the joints between the cladding units. These joints can be face-sealed, two-stage drained joints, pressure-equalized joints, or open joints.
2.2.1 Face-Sealed Barrier Walls
A face-sealed barrier wall implies that a cladding or exterior finish stops all water at the outside face of the wall. The cladding or coating is the water management system-there is no redundancy. Traditionally, the term barrier wall referred to a solid masonry or mass wall that formed a weather barrier because of its thickness. It leaked. It was just a much slower process, and one hoped that the wall dried before the moisture got to the interior. Today, poured-in-place concrete walls and concrete masonry walls are the most common true barrier walls. Concrete can take on a certain amount of water without detrimental effects, making these barrier walls an option that depends also on climate and exposure.
2.2.2 Internal Drainage Plane Walls
Most claddings allow for some passage of water, either through the material itself or at the joints. A secondary line of defense is required to stop any water that passes through the cladding and drain any condensed vapor. An internal drainage plane wall has a drainage plane up to 3/8 inch (10 mm) in depth as well as a water barrier and weep holes. The redundancy offered by the water barrier provides much more protection than the face-sealed barrier wall.
2.2.3 Drainage Cavity Walls
The drainage cavity wall-consisting of a cavity and a water barrier-has openings or weep holes at the base for drainage of any water that passes through the cladding and vapor that condenses in the cavity. It may or may not have additional openings to promote drying through air circulation. The cavity must be of sufficient width to stop water from bridging the gap-3/8 inch (10 mm) is the dividing line used in this book. A larger dimension may be necessary to compensate for construction tolerances and workmanship.
2.2.4 Pressure-Equalized Rain-Screen Walls
True pressure-equalized rain-screen walls are rare. A metal and glass curtain wall is an example of such a wall; but even this shows only moderate success. A report by Rick Quirouette, written for Canada Mortgage and Housing Corporation (CMHC) noted that "the most advanced rainscreen system design is the metal and glass curtain wall." But measurements in the field would appear to indicate substantially less than 25 percent pressure equalization in a spandrel even during low-pressure winds. However, Quirouette comments that even with these pressure differences, there did not appear to be any leakage during a "moderately severe storm."
2.3 SELECTING THE RIGHT WATER MANAGEMENT SYSTEM
On low-rise buildings, particularly those with overhangs and in protected areas, a less efficient water management system may be acceptable. The Partnership for Advancing Technology in Housing (PATH), a collaboration of U.S. Housing and Urban Development (HUD) and the Federal Housing Administration (FHA), states that face-sealed barrier walls are effective in climates with less than 30 inches (762 mm) of annual precipitation whereas internal drainage plane walls are effective in areas with annual precipitation, from 30 to 50 inches (762-1270 mm). Drainage cavity walls are suggested for climates with less than 60 inches (1524 mm) of rain a year. Over this amount, a pressure-equalized rain screen (PER) is recommended. It should be noted that, for the most part, the recommendations are for small, one to two story residences that are more likely to have overhangs and be protected from winds. (According to the U.S. Census Bureau, only about 7 percent of the housing units in the United States were higher than three stories and less than 16 percent were in buildings with five or more attached units in 2001.) The Builder's Guides, published by the Building Science Corporation, recommend only using face-sealed walls in climates with less than 20 inches (508 mm) of annual precipitation-a more conservative and safe recommendation. Again, these are recommendations for homes and smaller buildings.
This book recommends the following minimums in areas where water penetration is of concern and a long exterior wall life is desired:
A secondary line of defense in the form of a water barrier A flashed cavity of a constructable dimension to drain interstitial water to the exterior and break capillary action between the cladding and the backup wall, taking construction tolerances into consideration As complete an air barrier system as constructable and affordable
2.3.1 Deflect, Drain, or Dry? Vent or Ventilate?
An important part of managing water is ensuring that wet components dry before any damage occurs. Ventilating a drainage cavity accelerates the drying of components within the wall through evaporation. The amount of ventilation must be balanced between the drying potential and the increased potential for water entering the wall through the additional openings. In areas with high indices of wind-driven rain and long cool-wet periods, which slow drying, such as in the Pacific Northwest, it may be prudent to reduce the number of openings to only those required for drainage.
The surest way to stop water ingress is not to let the materials get wet in the first place. Deflection of water, by using overhangs and drips on flashings, will reduce the amount of water that flows down the wall. Drainage of water is equally important, be it from a cavity, the roof, the adjacent hard or soft landscaping, or any other potential "catch basin," however small or large. Venting, as opposed to ventilating, helps stop water from entering the wall by minimizing air pressure differences across the cladding. A pressure-equalized rain screen does not promote ventilation of the cavity-in fact, it does the opposite. The National Research Council of Canada (NRCC) recommends that vent holes be located at the same height, to reduce airflow through the compartment.
2.3.2 Forces that Move Water
If water cannot be diverted, the only option left is to eliminate the forces that move water through a wall. The force of gravity can be a problem with any components that are not vertical. (However, wind on the exterior wall can cause water to flow uphill on vertical surfaces, particularly at building corners and parapets.) Any nonvertical surface exposed to water should be treated as a roof. This simple reasoning would do much to alleviate leakage in buildings. A sloping sill is not a wall; it is a roof and should be clad with materials appropriate for a roof. Surface tension, capillary suction, and momentum can be stopped through simple geometry. Minimizing air pressure differences across the cladding, with a PER, eliminates the final force.
2.4 WATER BARRIERS AND THEIR PLACEMENT
2.4.1 Building Wraps
Microporous plastic water barriers that stop water and air but are permeable to vapor are called building wraps or "housewraps." Dupont developed the first in the late 1970s-a nonperforated, nonwoven, spun-bonded polyethylene called Tyvek HouseWrap-and a generic term was born. Today Tyvek water barriers are made of spun-bonded polyolefin and include HomeWrap, CommercialWrap, and also StuccoWrap. Another nonperforated building wrap is Typar HouseWrap, which is a coated spun-bonded polypropylene. The permeability of these products comes from the manufacturing process. Some plastic building wraps are mechanically punched or perforated for permeability. The term SBPO (spun-bonded polyolefin) is reserved for materials such as Tyvek that are made of nonperforated, nonwoven, spun-bonded polyolefin.
The perforated building wraps generally allow more water to pass than the nonperforated. Also many perforated building wraps are not classified as air barriers. Nonperforated building wraps are commonly used as an air barrier, the function for which they were originally marketed. Nonperforated building wraps generally have good vapor permeability. Tear resistance varies from product to product. Available in story-high widths, building wraps can be used to "weatherproof" a wall quickly. There is much research in this area, with new products continually coming on the market, some nonperforated. Dow has introduced Styrofoam Weathermate and Owens Corning has PinkWrap, both building wraps with some transparency. Self-draining building wraps, such as the nonperforated StuccoWrap, have a textured surface with small rivulets or channels for water drainage. More discussion on building wraps can be found in Chapter 3 under "Air Barrier Systems."
2.4.2 Building Paper and Felt
The conventional water barrier is building paper, an asphalt saturated Kraft paper, or felt. The common product is #15 or #30 felt, or Grade D building paper, with 20-, 30-, or 60-minute ratings. While sharing some similarities, building paper and felt also have different characteristics. Felt today is made from recycled paper fiber from corrugated boxes and newspapers. These cellulose fibers result in a material that is thicker and less dense than the Kraft paper used for building paper. The more open pore structure of the felt allows a high percentage of asphalt impregnation. The result is a thick, stiff material that has high water resistance but tends to crack when folded around corners. Building papers use cellulose fiber made from wood pulp, resulting in a dense, strong fiber mat. The tighter pore structure reduces the percentage of asphalt that can be impregnated. The result is a less saturated paper that is still water resistant but more vapor permeable and pliable around corners. Because building paper is substantially thinner than felt, two layers are often recommended to obtain a double drainage plane-for example, using two layers of 30-minute paper in place of one layer of 60-minute paper.
Both building paper and felt come in widths of 36 to 40 inches. Although air movement is decreased, they are not considered air barriers even with the seams taped. Both building paper and felt will absorb some moisture. Their vapor permeability increases when saturated, helping wet materials dry to the exterior. If any water leakage occurs to the inside of the building paper or felt, they can absorb the water, allowing it to pass to the exterior through evaporation.
As with all components, building paper and felt have evolved over the years. The new generations include a 30-minute double-ply building paper with 2-inch (50 mm) wide asphalt mastic strips at 16-inch (400 mm) intervals to increase water protection at nail and staple holes, a proprietary product of Hal Industries. Fortafiber has a two-ply paper with a 150-minute water holdout rating. Hal Industries also produces a corrugated two-ply building paper with a 150-minute water holdout rating.
2.4.3 Building Wrap or Felt?
A reputed problem with some building wraps, primarily the perforated ones, is that surfactants (surface-active contaminants) can reduce the surface tension of the water, making it easier for the water to pass through a smaller opening. Surfactants can be found in lignin from wood, such as cedar and redwood, and in substances such as soap, which is sometimes used though not recommended as a plasticizer with stucco. Other stucco additives can work as surfactants, leading some building envelope specialists to advise against using building wraps with stucco. These same surfactants have caused less severe problems with paper and felt. A good recommendation is to ensure that any material in direct contact with the water barrier will not create problems by asking the manufacturer to address the issue in writing.
Paul Fisette (of the University of Massachusetts), in an article titled, "Housewrap vs. Felt," discussed the problems with surfactants. He concluded that soaps and extractives from cedar do have an effect on the water resistance of building wrap. Testing by Fisette further suggested that nonperforated building wrap displayed better water resistance. Felt may seal better around nails and staples, depending on the thickness and asphalt content. However, in the end, Fisette decided that it does not matter "a whole lot" whether you choose a building wrap or felt if you get the flashing details right and are careful with installation. In general, felt costs less than building wrap, but the installation cost is higher. Felt, and to some extent building paper, is manufactured by a large number of companies and rarely identified as a product. Felts are governed by a host of codes, from which the manufacturers can pick and choose, making it difficult to compare one to another. Building wraps are identified as products. However, comparisons are also difficult with building wraps, as different manufacturers may use different testing methods.
2.4.4 Sheet Membranes
Adhered sheet membranes can be hot- or cold-applied. In general, any roofing material suitable for a vertical application can be used as a water barrier if the substrate, attachment, and method of installation is acceptable-some are torched-in-place, creating a potential fire hazard during installation.
2.4.5 Self-Adhesive Membranes, or "Peel-and-Stick"
The newest water barriers are self-adhesive sheet membranes, descriptively called peel-and-stick. They are manufactured by laminating a rubberized asphalt compound to a polyethylene film. Though the membrane is self-adhesive, many substrates require careful priming. Proper installation is critical, including lapping at edges and ends. It may be prudent to also attach the membrane mechanically-this can often occur in tandem with the fastening of another component such as rigid insulation to the exterior of the peel-and-stick. A popular combination is using products such as Grace Perm-a-Barrier or Bakor Blueskin over nonpaper faced gypsum sheathing. This combination requires a specific primer to bond with the moisture-resistant fibers of the sheathing. Peel-and-stick comes in widths from 4 to 36 inches (100-910 mm); the narrower widths are used to seal joints and for flashing.
In addition to stopping water, peel-and-stick is an air barrier and usually a vapor retarder, making placement potentially problematic, depending on the location of the thermal insulation and the climate. Bakor has introduced a peel-and-stick called Blueskin Breather that is vapor permeable.
(Continues...)
Excerpted from Designing the Exterior Wall by Linda Brock Excerpted by permission.
All rights reserved. No part of this excerpt may be reproduced or reprinted without permission in writing from the publisher.
Excerpts are provided by Dial-A-Book Inc. solely for the personal use of visitors to this web site.
Table of Contents
Preface.Acknowledgments.
Using This Book.
PART 1: CHOOSING THE COMPONENTS.
Chapter 1: Decisions That Affect the Exterior Wall.
1.1 Introduction to the Building Envelope.
1.2 Decisions Affecting Aesthetics, Function, Durability, and the Budget.
1.3 Climate and the Exterior Wall.
1.4 Function of the Exterior Wall.
1.5 Cladding Systems.
1.6 “Whole-Wall” Design.
1.7 Selecting and Positioning the Barriers and Retarders.
CHECKLIST: Preliminary Design Information and Decisions.
Chapter 2: Water Barriers and Flashings.
2.1 Managing Water.
2.2 Water Management Systems.
2.3 Selecting the Right Water Management System.
2.4 Water Barriers and Their Placement.
2.5 Installation.
2.6 Flashings.
2.7 Testing and Measuring Water Leakage.
2.8 Quick Notes: Water Ingress.
Chapter 3: Air Barrier Systems, Vapor Retarders, and Insulation.
3.1 Stopping Air and Controlling Thermal and Vapor Transfer.
3.2 Air Movement: Loss of Conditioned and Vapor-Laden Air.
3.3 Vapor Transmission by Diffusion.
3.4 Heat Transfer by Conduction And Radiation.
Chapter 4: Sealant Joints.
4.1 Structural Forces and Differential Movement.
4.2 Expansion and Control Joints.
4.3 Joint Design.
4.4 Construction Tolerances.
4.5 Joint Components.
4.6 Installation of Liquid Sealants.
4.7 Maintenance.
4.8 Testing Sealants.
4.9 Quick Notes: Sealant Joints.
CHECKLIST: Selecting and Positioning Barriers and Retarders.
PART II: DETAILING FOR DURABILITY.
Chapter 5: Curtain Walls.
5.1 The Development of Curtain Walls.
5.2 Aluminum Glass Curtain Walls.
5.3 Metal- and Stone-Panel Curtain Walls.
5.4 Designing Curtain Walls with Glass, Metal, and Stone Panels.
5.5 Case Study.
5.6 Precast Concrete and Glass-Fiber Reinforced Concrete Panels.
5.7 How to Stay Out of Trouble When Designing Curtain Walls.
5.8 References.
Chapter 6: Anchored Brick Veneer.
6.1 Brick Veneer Anchored to the Steel-Stud Backup Walls of a Four- to Twenty-Story Building.
6.2 Wall Type A: Brick Veneer Anchored To Steel-Stud Backup.
6.3 Climate.
6.4 Is ABV/SS Risky Business?
6.5 Reducing Risk.
6.6 Repelling Water.
6.7 Accommodating Differential Movement with Expansion Joints.
6.8 Designing Parapet Veneer Panels: A Special Case.
6.9 Supplemental Information On ABV/SS Components.
6.10 ABV Details.
6.11 Case Study.
6.12 Other Systems.
6.13 References.
Chapter 7 Exterior Insulation Finish System (EIFS) and Concrete Masonry Walls.
7.1 Concrete Masonry Walls.
7.2 Single-Wythe Concrete Masonry: Face-Sealed Barrier Wall.
7.3 Exterior Insulation Finish System (EIFS).
7.4 Wall Type B: EIFS with Internal Drainage Plane on Concrete Masonry Wall.
7.5 EIFS Design.
7.6 EIFS Installation.
7.7 Maintenance.
7.8 EIFS Concerns.
7.9 Details: EIFS.
7.10 EIFS over Light-Gauge Steel or Wood Stud Walls.
7.11 Case Study.
7.12 Case Study.
7.13 References.
Chapter 8: Wood-Frame Construction, Stucco, and Fiber-Cement Siding.
8.1 Wood-Frame Construction.
8.2 Stucco.
8.3 Wall Type C: Three-Coat Stucco on Wood Frame with Internal Drainage Plane.
8.4 Stucco Design.
8.5 Stucco Application.
8.6 Maintenance.
8.7 Concerns with Stucco.
8.8 Details: Stucco.
8.9 Fiber-Cement Cladding.
8.10 Wall Type D: Fiber-Cement Board Siding with Drainage Cavity.
8.11 Fiber-Cement Siding Design.
8.12 Fiber-Cement Siding Installation.
8.13 Maintenance.
8.14 Concerns with Fiber-Cement Claddings.
8.15 Details: Fiber-Cement Siding.
8.16 Case Study.
8.17 References.
PART III: ADVANCING THE ENVELOPE.
Chapter 9: Terra-Cotta, EIFS, Stone, and Brick: Are They Durable?
9.1 Truth In Materials.
9.2 The Great Impostors: EIFS and Terra-Cotta.
9.3 Aesthetics and Durability: Can You Have Both with Carrara Marble?
9.4 Build It Right The First Time or Repair It Quickly: Anchored Brick Veneer Failures.
Chapter 10: Architect’s Design Kit: Form, Surface, Color, and Thick and Thin Walls.
10.1 The Exterior Wall.
10.2 Aesthetic Kit: Form, Surface, and Color.
10.3 Westin New York at Times Square.
10.4 Experience Music Project, Seattle, Gehry Partners.
10.5 Comparisons: Mondrian Planes and Swoopy Forms.
10.6 Functional Kit: Thick and Thin Walls.
10.7 Vitra Conference Pavilion: Thicker Walls in Germany.
10.8 San Francisco Museum of Modern Art: Thin Brick That Works.
10.9 Are Two Walls Better than One?
10.10 Seattle Justice Center.
Chapter 11: Wood-Frame Construction: Designing for the Climate and the Future.
11.1 Durability—The Linchpin of Sustainability.
11.2 Vancouver, British Columbia: “The Look That Didn’t Last”.
11.3 Seattle: “When It Rains, It Pours In”.
11.4 What Can Be Learned from the Leaky Condos?
11.5 How To Do It Right: Two Countries, Two Climates, and Two Solutions.
11.6 Home 2000 and Winter Rains of Vancouver, British Columbia.
11.7 KST-Hokkaido House and Heavy Snow Loads of Northern Japan.
11.8 What Can Be Learned from the Two Houses?
Appendix A: Hygrothermal Maps.
Appendix B: Building Form.
Notes.
Bibliography and Resources.
Index.