Etching, Engraving and Other Intaglio Printmaking Techniques
Intaglio printmaking involves engraving or incising a figure in stone or other hard material to obtain an impression from the subsurface design. In this thorough handbook, a noted printmaker and teacher offers complete up-to-date coverage of etching, engraving, drypoint, and other well-known intaglio techniques, as well as such less-familiar methods as tuilegraphs, collagraphs, and transfers.
The first part of the book is devoted to a thorough introduction to materials and tools, printing equipment, papers, presses—even how to set up your workshop for maximum safety and efficiency. In Part Two, the author proceeds to a detailed discussion of etching techniques, including formulas for grounds and inks, aquatint, white ground, hard ground, soft ground, sugar lift, and acids.
Once familiar with basic etching techniques, the student is then given precise illustrated instructions in printing techniques, including basic printing, double intaglio printing (the author's own method); color printing and embossing, the viscosity method, and viscosity and aquatint. For each procedure, clear, step-by-step directions cover the process itself, materials and equipment required, and cleanup. An especially helpful "what went wrong" section at the end of each chapter diagnoses problems and offers solutions.
In Part 4 Ms. Leaf details other mediums and methods: drypoint, notable for its characteristic velvety dark lines; engraving, one of the earliest forms of expression known to man, dating back to prehistoric times; collagraphs, plates made in the same way as collages and then printed; and the Blake Transfer Method, adapted from a technique developed by the English artist and poet William Blake (1757–1827).
A final Appendix treats such ancillary topics as framing and matting prints, storage, agents, and where to sell and show your work. Enhanced with over 220 illustrations, including works by Rembrandt, Callot, Dürer, Goya, and Brueghel, and a wealth of illustrative figures and photographs, this precise and detailed manual belongs at the side of any serious printmaker, novice, or ink-stained veteran.
"Excellent, comprehensive . . . superbly organized." — AB Bookman's Weekly.
1000262996
The first part of the book is devoted to a thorough introduction to materials and tools, printing equipment, papers, presses—even how to set up your workshop for maximum safety and efficiency. In Part Two, the author proceeds to a detailed discussion of etching techniques, including formulas for grounds and inks, aquatint, white ground, hard ground, soft ground, sugar lift, and acids.
Once familiar with basic etching techniques, the student is then given precise illustrated instructions in printing techniques, including basic printing, double intaglio printing (the author's own method); color printing and embossing, the viscosity method, and viscosity and aquatint. For each procedure, clear, step-by-step directions cover the process itself, materials and equipment required, and cleanup. An especially helpful "what went wrong" section at the end of each chapter diagnoses problems and offers solutions.
In Part 4 Ms. Leaf details other mediums and methods: drypoint, notable for its characteristic velvety dark lines; engraving, one of the earliest forms of expression known to man, dating back to prehistoric times; collagraphs, plates made in the same way as collages and then printed; and the Blake Transfer Method, adapted from a technique developed by the English artist and poet William Blake (1757–1827).
A final Appendix treats such ancillary topics as framing and matting prints, storage, agents, and where to sell and show your work. Enhanced with over 220 illustrations, including works by Rembrandt, Callot, Dürer, Goya, and Brueghel, and a wealth of illustrative figures and photographs, this precise and detailed manual belongs at the side of any serious printmaker, novice, or ink-stained veteran.
"Excellent, comprehensive . . . superbly organized." — AB Bookman's Weekly.
Etching, Engraving and Other Intaglio Printmaking Techniques
Intaglio printmaking involves engraving or incising a figure in stone or other hard material to obtain an impression from the subsurface design. In this thorough handbook, a noted printmaker and teacher offers complete up-to-date coverage of etching, engraving, drypoint, and other well-known intaglio techniques, as well as such less-familiar methods as tuilegraphs, collagraphs, and transfers.
The first part of the book is devoted to a thorough introduction to materials and tools, printing equipment, papers, presses—even how to set up your workshop for maximum safety and efficiency. In Part Two, the author proceeds to a detailed discussion of etching techniques, including formulas for grounds and inks, aquatint, white ground, hard ground, soft ground, sugar lift, and acids.
Once familiar with basic etching techniques, the student is then given precise illustrated instructions in printing techniques, including basic printing, double intaglio printing (the author's own method); color printing and embossing, the viscosity method, and viscosity and aquatint. For each procedure, clear, step-by-step directions cover the process itself, materials and equipment required, and cleanup. An especially helpful "what went wrong" section at the end of each chapter diagnoses problems and offers solutions.
In Part 4 Ms. Leaf details other mediums and methods: drypoint, notable for its characteristic velvety dark lines; engraving, one of the earliest forms of expression known to man, dating back to prehistoric times; collagraphs, plates made in the same way as collages and then printed; and the Blake Transfer Method, adapted from a technique developed by the English artist and poet William Blake (1757–1827).
A final Appendix treats such ancillary topics as framing and matting prints, storage, agents, and where to sell and show your work. Enhanced with over 220 illustrations, including works by Rembrandt, Callot, Dürer, Goya, and Brueghel, and a wealth of illustrative figures and photographs, this precise and detailed manual belongs at the side of any serious printmaker, novice, or ink-stained veteran.
"Excellent, comprehensive . . . superbly organized." — AB Bookman's Weekly.
The first part of the book is devoted to a thorough introduction to materials and tools, printing equipment, papers, presses—even how to set up your workshop for maximum safety and efficiency. In Part Two, the author proceeds to a detailed discussion of etching techniques, including formulas for grounds and inks, aquatint, white ground, hard ground, soft ground, sugar lift, and acids.
Once familiar with basic etching techniques, the student is then given precise illustrated instructions in printing techniques, including basic printing, double intaglio printing (the author's own method); color printing and embossing, the viscosity method, and viscosity and aquatint. For each procedure, clear, step-by-step directions cover the process itself, materials and equipment required, and cleanup. An especially helpful "what went wrong" section at the end of each chapter diagnoses problems and offers solutions.
In Part 4 Ms. Leaf details other mediums and methods: drypoint, notable for its characteristic velvety dark lines; engraving, one of the earliest forms of expression known to man, dating back to prehistoric times; collagraphs, plates made in the same way as collages and then printed; and the Blake Transfer Method, adapted from a technique developed by the English artist and poet William Blake (1757–1827).
A final Appendix treats such ancillary topics as framing and matting prints, storage, agents, and where to sell and show your work. Enhanced with over 220 illustrations, including works by Rembrandt, Callot, Dürer, Goya, and Brueghel, and a wealth of illustrative figures and photographs, this precise and detailed manual belongs at the side of any serious printmaker, novice, or ink-stained veteran.
"Excellent, comprehensive . . . superbly organized." — AB Bookman's Weekly.
24.95
In Stock
5
1
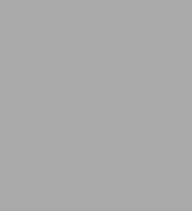
Etching, Engraving and Other Intaglio Printmaking Techniques
240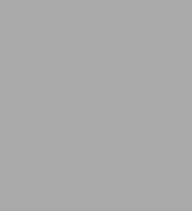
Etching, Engraving and Other Intaglio Printmaking Techniques
240
24.95
In Stock
Product Details
ISBN-13: | 9780486139241 |
---|---|
Publisher: | Dover Publications |
Publication date: | 06/14/2012 |
Series: | Dover Art Instruction |
Sold by: | Barnes & Noble |
Format: | eBook |
Pages: | 240 |
File size: | 29 MB |
Note: | This product may take a few minutes to download. |
About the Author
From the B&N Reads Blog