Fatigue of Materials and Structures: Application to Damage and Design / Edition 1 available in Hardcover, eBook
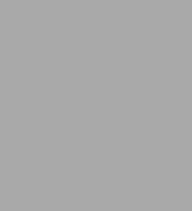
Fatigue of Materials and Structures: Application to Damage and Design / Edition 1
- ISBN-10:
- 1848212674
- ISBN-13:
- 9781848212671
- Pub. Date:
- 02/21/2011
- Publisher:
- Wiley
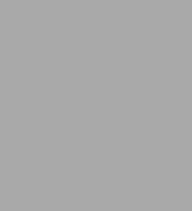
Fatigue of Materials and Structures: Application to Damage and Design / Edition 1
Buy New
$190.95-
SHIP THIS ITEMIn stock. Ships in 6-10 days.PICK UP IN STORE
Your local store may have stock of this item.
Available within 2 business hours
Overview
The book deals with crack initiation, crack growth, low-cycle fatigue, gigacycle fatigue, shorts cracks, fatigue micromechanisms and the local approach to fatigue damage, corrosion fatigue, environmental effects and variable amplitude loadings, and will be an important and much used reference for students, practicing engineers and researchers studying fracture and fatigue in numerous areas of mechanical, structural, civil, design, nuclear, and aerospace engineering as well as materials science.
Product Details
ISBN-13: | 9781848212671 |
---|---|
Publisher: | Wiley |
Publication date: | 02/21/2011 |
Series: | ISTE Series , #537 |
Pages: | 512 |
Product dimensions: | 6.00(w) x 9.30(h) x 0.90(d) |
About the Author
André Pineau is Professor at Mines ParisTech and a member of the French Academy of Engineering. He has published about 300 papers in international journals and edited or co-edited 10 books. His main research fields are phase transformations, fatigue and fracture of metallic materials.
Table of Contents
Foreword Stephen D. Antolovich xi
Chapter 1 High Temperature Fatigue Stephen D. Antolovich André Pineau 1
1.1 Introduction and overview 1
1.1.1 Introductory remarks 1
1.1.2 A little history 2
1.1.3 High temperature testing closed-loop control and extensometry 5
1.1.4 Damage mechanisms and interactions in high-temperature fatigue 5
1.1.5 Organization of this chapter 6
1.1.6 Goals 7
1.2 9 to 12% Cr steels 7
1.2.1 Introduction 7
1.2.2 Microstructures of 9-12% Cr steels 9
1.2.3 Mechanical behavior 11
1.2.4 Damage 16
1.2.5 Damage model and life prediction 20
1.3 Austenitic stainless steels 22
1.3.1 Introduction 22
1.3.2 Mechanical behavior and microstructure 24
1.3.3 Life and damage 27
1.3.4 Physically-based damage modeling of creep-fatigue interactions 34
1.4 Fatigue of superalloys 40
1.4.1 Microstructure and processing of superalloys 40
1.4.2 Deformation mechanisms 45
1.4.3 Cyclic deformation and microstructure 46
1.4.4 High-temperature low-cycle fatigue 55
1.4.5 Fatigue crack propagation (FCP) of superalloys 75
1.4.6 Concluding remarks on Ni-base alloys 104
1.5 Lifespan prediction in high-temperature fatigue 104
1.5.1 Introduction 104
1.5.2 Physically-based models 105
1.5.3 Phenomenological models 108
1.6 Conclusions 114
1.7 Acknowledgments 118
1.8 Bibliography 118
Chapter 2 Analysis of Elasto-plastic Strains and Stresses Near Notches Subjected to Monotonic and Cyclic Multiaxial Loading Paths Gregory Glinka 131
2.1 Introduction 131
2.2 Multiaxial fatigue parameters 134
2.2.1 Equivalent parameter methods 134
2.2.2 Critical plane methods 137
2.2.3 Mean stress effects in multiaxial fatigue 139
2.2.4 Predictive capabilities of multiaxial parameter W 141
2.3 Elasto-plastic notch-tip stress-strain calculation methods 146
2.3.1 Uniaxial strain or plane strain states at the notch tip 146
2.3.2 Multiaxial stress states 151
2.4 Comparison of notch stress-strain calculations with numerical data 164
2.4.1 Monotonic proportional loading 164
2.4.2 Monotonic non-proportional loading 167
2.4.3 Proportional multiaxial cyclic loading 170
2.5 Conclusion 173
2.6 Bibliography 173
2.7 Symbols 176
Chapter 3 Fatigue of Composite Materials Claude Bathias 179
3.1 Introduction 179
3.2 Drastic differences between the fatigue of composites and metals 183
3.2.1 Damage at the microscopic level 184
3.2.2 Role of plasticity and nonlinear behavior 188
3.2.3 Shape of the endurance curves of composite materials 189
3.2.4 Role of the fibers and the matrix 190
3.3 Notch effect on fatigue strength 191
3.4 Effect of a stress on composite fatigue 193
3.4.1 Fatigue under compression 193
3.4.2 Fatigue under bending conditions 195
3.4.3 Effect of tensile over-loading 197
3.5 Fatigue after impact 198
3.6 Fatigue damage criteria 199
3.6.1 Variation of rigidity 199
3.6.2 Variation of residual strength after fatigue 201
3.7 Conclusion 202
3.8 Bibliography 203
Chapter 4 Fatigue of Polymers and Elastomers Claude Bathias 205
4.1 Introduction 205
4.2 Life of Polymers 206
4.3 Crack propagation within polymers 207
4.4 Damaging mechanisms of polymers 208
4.5 Specific case of the fatigue of elastomers 210
4.6 The life of natural rubbers 211
4.6.1 Wöhler law with crystallizable rubbers 212
4.7 Crack propagation in natural rubber 213
4.7.1 Crack growth curve - influence of ratio R 214
4.7.2 Influence of the test temperature 215
4.7.3 Influence of the environment and combined environment-temperature effects 216
4.8 Propagation mechanisms of cracks in natural rubber 217
4.9 Multiaxial fatigue of rubbers 219
4.10 Cavitation of rubbers 221
4.11 Conclusion 222
4.12 Bibliography 222
Chapter 5 Probabilistic Design of Structures Submitted to Fatigue Bruno Sudret 223
5.1 Introduction 223
5.2 Treatment of hazard in mechanical models 224
5.2.1 General scheme 224
5.2.2 Probabilistic model of the input parameters 225
5.2.3 Uncertainty propagation methods 226
5.2.4 Conclusion 228
5.3 Plotting probabilistic S-N curves 229
5.3.1 Introduction 229
5.3.2 ESOPE method 229
5.3.3 Guédé-Perrin-Pascual-Meeker method (GPPM) 231
5.3.4 Validation of the assumptions 234
5.3.5 Application example 234
5.3.6 Conclusion 235
5.4 Probabilistic design with respect to crack initiation 237
5.4.1 Introduction 237
5.4.2 Deterministic model 237
5.4.3 Probabilistic modeling of uncertainties 239
5.4.4 Random cumulative damage 240
5.4.5 Application: probabilistic design of a pipe under thermal fatigue conditions 242
5.4.6 Conclusion 245
5.5 Probabilistic propagation models 245
5.5.1 Introduction 245
5.5.2 Deterministic model 246
5.5.3 Probabilistic model of the data 247
5.5.4 Propagation prediction 247
5.5.5 Bayesian updating of crack propagation models 249
5.5.6 General conclusion 252
5.6 Conclusion 252
5.7 Appendix A: probability theory reminder 253
5.7.1 Random variables 253
5.7.2 Expected value, moments, and quantiles 255
5.7.3 Maximum likelihood 255
5.7.4 Bayesian inference 257
5.7.5 Reliability analysis and FORM method 258
5.8 Bibliography 259
Chapter 6 Prediction of Fatigue Crack Growth within Structures Jean Lemaitre 265
6.1 Prediction problems 265
6.1.1 Structures 267
6.1.2 Loading 267
6.1.3 Material 268
6.2 Crack growth laws 268
6.2.1 Mechanical definition of the cracking variables 268
6.2.2 Fatigue crack growth laws 274
6.2.3 Bifurcation criteria 279
6.2.4 Three-dimensional elements 281
6.3 Calculation of cracking variables 282
6.3.1 Two-dimensional problems under linear elasticity and simple loading conditions 283
6.3.2 Three-dimensional problems 287
6.3.3 Issues under plastic and visco-plastic conditions 288
6.4 Resolution method of the cracking equations 289
6.4.1 Identification of the crack growth laws 289
6.4.2 Simple and constant cyclic loading 290
6.4.3 Loadings with a complex history 292
6.4.4 Random loading 295
6.4.5 Non-simple loading 295
6.5 New directions 296
6.6 Bibliography 296
List of Authors 299
Index 301