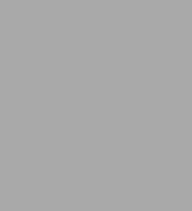
Heat Capacities: Liquids, Solutions and Vapours
524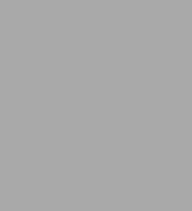
Heat Capacities: Liquids, Solutions and Vapours
524Hardcover
-
SHIP THIS ITEMNot Eligible for Free ShippingPICK UP IN STORE
Your local store may have stock of this item.
Available within 2 business hours
Related collections and offers
Overview
Product Details
ISBN-13: | 9780854041763 |
---|---|
Publisher: | RSC |
Publication date: | 08/16/2010 |
Pages: | 524 |
Product dimensions: | 6.15(w) x 9.20(h) x (d) |
About the Author
Read an Excerpt
Nanocasting
A Versatile Strategy for Creating Nanostructured Porous Materials
By An-Hui Lu, Dongyuan Zhao, Ying Wan
The Royal Society of Chemistry
Copyright © 2010 An-Hui Lu, Dongyuan Zhao and Ying WanAll rights reserved.
ISBN: 978-1-84755-986-9
CHAPTER 1
Principles of Nanocasting
1.1 Nanocasting Concept
Casting is a 6000-year-old manufacturing process. The oldest surviving casting is a copper frog from 3200 bc. In the casting process, a liquid or a fluid material is poured into a mold, which contains a hollow cavity of the desired shape, and is then allowed to solidify (Figure 1.1). The solid casting is then ejected or broken out to complete the process. Casting is most frequently used for making complex shapes that would be otherwise difficult or uneconomical to produce by other methods. The casting process is divided into two distinct subgroups: expendable and non-expendable mold casting. Expendable mold casting is a generic classification that includes sand, plastic, shell, plaster and investment (lost-wax technique) moldings. Non-expendable mold casting differs from expendable processes in that the mold does not need to be reformed after each production cycle.
However, the above-mentioned old casting techniques are constrained to large size with a limitation in the centimeter range. If the casting procedure is scaled down to the nanometer scale, 'nanocasting' is a suitable word to describe this process. In recent years, nanocasting started emerging and developing with the demand for creating nanomaterial arrays and nanopores. Nanocasting can also be used for making complex shapes in nanoscale that cannot be prepared or fabricated by other methods. The earliest 'nanocasting' process was utilized to produce nanowire arrays using porous anodic aluminum oxide (AAO) as a template (Figure 1.2). However, the templating process is actually not a 'nanocasting' due to the fact that the diameter of AAO is normally in the sub-micrometer range. From this viewpoint, the first 'nanocasting' technique was adopted by Kyotani and coworkers. The 'nanocasting' technique was first adopted by Kyotani and other researchers to fabricate microporous carbons using ultra-stable zeolite Y (USY) as a hard template. They fabricated microporous carbons with large surface areas (>2000m2 g-1 and large microporosity via a nanocasting process. Microporous carbon replicas exhibited very high adsorption capacities.
In 1998, Göltner and coworkers first proposed the concept termed as 'nanocasting' in mesoporous materials. They used a mesoporous silica monolith with the interconnective pore system as a confined hard template via the 'two-step' nanocasting to prepare mesoporous organic polymer networks with well-defined nanostructure. From then on, the hard templating and nanocasting processes have attracted more and more attention and become one of the most important approaches for the synthesis of porous materials, especially mesoporous materials.
Microporous carbons cast by zeolite Y normally should have the negative structure of the template. Unfortunately, the produced carbons cannot fully duplicate their parent zeolites' structure due to the fact that the pore size of the zeolite template is too small for carbon precursors to infiltrate. Kyotani and coworkers had made tremendous efforts to control nanocasting; however, partial 'zeolite' framework structure with a low periodic regularity can only be observed in a small domain of the obtained carbon products. Another reason for unsuccessful duplication of zeolitic structures is the large amount of defects caused by crystalline aluminosilicates in amorphous carbons. Since this work, nanocasting has been successfully employed in the synthesis of ordered mesoporous materials. The earliest example could be traced back to 1999 when mesoporous carbons were synthesized by using mesoporous silica as a hard template via the nanocasting strategy (Figure 1.3). Two Korean research groups independently reported the nanocasting synthesis of mesoporous carbons. Thereafter, the synthesis of ordered mesoporous materials from nanocasting strategy became a hot topic in the research field of mesostructured materials, especially for non-silicious mesostructures.
1.2 Hard Templates: Ordered Mesoporous Materials
Porous materials have both continuous skeletons and voids that can be randomly arranged (disordered pore system) or highly regular (ordered pore system) with large surface areas. According to the definition of IUPAC (International Union of Pure and Applied Chemistry), porous materials can be divided into microporous (with pore diameter < 2nm), mesoporous (pore size in the range of 2–50 nm) and macroporous materials (pore size >50nm). Among them, microporous mesoporous materials are the most widely studied for applications of sensors, shape-selective catalysis, chemical separations and electronic applications. The presence of micro- or mesopore channels allows for molecules that are accessible to the large internal surface areas and the internal active sites, enhancing shape selectivity and sorption properties.
Generally, inorganic microporous materials like zeolites or molecular sieves are often in crystalline form with narrow pore-size distributions, large surface areas and high ion exchangeable properties, which make them suitable for application in adsorption and catalysis. However, the small pore size of zeolites limits their further application in heavy oil products and the synthesis/ separation of large molecules.
1.2.1 Synthesis of Mesoporous Materials
In spite of the considerable efforts that have been made toward making large and regular pore systems, ordered mesoporous materials still remained elusive until the discovery of MCM-41 in 1992. The researchers of Mobil Company first reported a family of mesoporous silicate molecular sieves (M41S) with large surface areas (up to 1400m2 g-1) and narrow pore-size distribution (in the range of 1.5–10nm). The MCM-41 materials process 2-D hexagonal mesostructures with uniform pore size, but their silicate pore walls are amorphous. MCM-41 can be easily synthesized under the 'hydrothermal condition' in the presence of alkyltrimethylammonium surfactant cations with an alkyl chain length ranging from 8 to 22 carbon atoms. The synthesis mechanism of MCM-41 was proposed, for the first time, as the true 'template' concept, which brought out a novel concept for the scientific domain. As a consequence, a large number of ordered mesoporous silicate materials like SBA-n, KIT-n, FDU-n and HMS-n with various structures have been obtained one after another following the 'surfactant templating' method.
1.2.2 Ordered Mesoporous Materials Prepared from Soft-templating
Soft-templating is defined as a process in which organic molecules serve as a 'mold' and around which a framework is built up. The removal of these organic molecules results in a cavity which retains the same morphology and structure of the organic molecules (Figure 1.4).
The 'soft' templates are usually in the molten or liquid state. Their macroscopic mechanical properties present 'soft' characteristics, such as the fluid property under certain conditions, which is very different with the casting molds. An ample variety of ordered structures can be formed by the soft-templating method through the non-covalence intermolecular interaction (short-distance repulsion and long-distance attraction), which is situated between the solid crystal structure and the liquid state structure. Another characteristic of soft templates is the resulting periodic structure restricted in the nanometer scale. Plenty of soft templates, including cationic, anionic and non-ionic surfactants, and mixed surfactant systems, such as cationic–cationic, cationic–anionic and non-ionic mixed surfactant systems, have been utilized to synthesize highly ordered mesoporous materials. During the soft-templating processes, the sol-gel or evaporation induced self-assembly (EISA) processes are typically involved in the synthesis of ordered mesoporous materials. This route is suitable for the preparation of mesoporous silica, because the hydrolysis and condensation rates of silicates can be easily controlled by adjusting reaction parameters such as pH value and temperature. Many excellent reviews have been reported for the use of the soft-templating method to synthesize ordered mesoporous materials. These papers can assist readers in understanding both the synthesis of ordered mesoporous materials by the self-assembly approach and also the contents of the following chapters.
1.2.3 Formation Mechanism
A large number of studies have been carried out to investigate the formation and assembly mechanism of periodical mesostructures and to understand the roles of surfactants. The initial liquid-crystal template mechanism was first proposed by Mobil's scientists, which covers almost all of the possibilities. On the basis of recent developments, two main pathways, i.e. cooperative self-assembly and the 'true' liquid-crystal templating process, are seemingly efficient to synthesize ordered mesostructures from the soft-templating method, as shown in Figure 1.4.
1.2.3.1 Cooperative Surfactant-templating Assembly with Inorganic Oligomers
This pathway is based on the interactions occurring between surfactants and inorganic species such as silicates to form inorganic–organic mesostructured composites. Silicate polyanions such as oligomers interact with positively charged groups of surfactants driven by Coulomb forces. The silicate species at the interface cooperatively polymerize and cross-link, and further change the charge density of inorganic layers. With the reaction, the cooperative arrangements of surfactants and the charge density between inorganic and organic species influence each other. Hence the compositions of inorgani–corganic hybrids differ to some degree. The matching of charge density at the surfactant/inorganic interfaces governs the assembly process. The final mesophase is the ordered 3-D arrangement with the lowest energy.
Elaborate investigations on mesoporous materials have been focused on understanding and utilizing the inorganic–organic interactions. Stucky and coworkers proposed four general synthetic routes which are S+ I-, S-I+, S+X-I+ and S-X+I- (S+ = surfactant cations, S-= surfactant anions, I+ = inorganic precursor cations, I- = inorganic precursor anions, X+ = cationic counterions and X- = anionic counterions), respectively. A series of ordered non-siliceous mesostructured solids were successfully prepared. Moreover, mesoporous silica can be synthesized under strong acidic conditions. To yield mesoporous materials, it is important to adjust the chemistry of surfactant heads which can fit inorganic components. Under a basic solution, silicate anions (I-) match with surfactant cations (S+) through Coulomb forces (S+I-). The assembly of polyacid anions and surfactant cations to 'salt'-like mesostructures also belongs to the S+I- interaction. The organic–inorganic assembly of surfactants and inorganic precursors with the same charge is also possible in which counter ions are necessary as the bridge. For example, in the syntheses of mesoporous silicates by the S+X-I+ interaction, S+ and I+ are cationic surfactants and precursors, and X- can be halogen ions (Cl-, Br- and I-). In a strong acid medium, the initial S+ X-I+ interaction through Coulomb forces or, more exactly, double-layer hydrogen bonding interactions gradually transforms to the (IX)-S+ interaction.
1.2.3.2 Liquid-Crystal Template Pathway
In this pathway, true or semi-liquid-crystal mesophases are involved in the soft- templating assembly to synthesize ordered mesoporous solids using high-concentration surfactants as templates. The condensation of inorganic precursors is improved by reaction of the confined growth around the surfactants, forming ceramic-like frameworks. After condensation, the organic templates can be removed by either calcination or extraction, or by other methods. The inorganic materials 'nanocast' the mesostructures, pore sizes and symmetries from the liquid-crystal scaffolds.
The high concentration of surfactant can be achieved by inducing solvent evaporation, therefore this process is called an EISA. The EISA method is believed to be a powerful and versatile strategy for the synthesis of ordered mesoporous materials with diverse components and various morphologies, especially for the efficacious synthesis of ordered mesoporous metal oxides. Detailed and systematic studies on the EISA-based syntheses of inorganic species-surfactant hybrid composite films have been carefully carried out by Sanchez and coworkers. Beginning with inorganic precursors of a low polymerization degree in volatile polar solvents, the assembly on an organic–inorganic interface can be improved and moldable organic–inorganic frameworks can be formed. Inorganic precursors further hydrolyze and cross-link during the solvent evaporation process. At the final stage of solvent evaporation, high-content surfactants form liquid-crystal phases in the presence of inorganic oligomers. The organized mesostructures are possibly transferred from the first generated disordered intermediate phase. Finally, ordered mesophases are solidified to form a rigid inorganic framework. Afterwards, the surfactants can be removed by calcination. The final mesostructures are affected by several factors such as hydrolysis rate, cross-linking degree and surfactant/precursor ratio, in a similar way to the syntheses in the aqueous systems. In addition, it was found that some apparently noticeable parameters, such as water concentration, processing humidity, evaporating temperature and rate, and substrates greatly influence the regularity of final materials.
An excellent example for the application of the EISA process is the synthesis of mesoporous carbon frameworks reported recently by Zhao's group. The synthesis procedure includes five major steps: the preparation of resol precursors, the formation of ordered hybrid mesophases by organic–organic self-assembly during the solvent evaporation, thermopolymerization of the resols around the templates to solidify the ordered mesophases, the removal of templates and carbonization of the resin polymer frameworks to the homologous carbons.
The initial homogenous solution is prepared by dissolving triblock copolymers and resol precursors in ethanol. Resol precursors have a low molecular weight (M = 200-500), and are water- and alcohol-soluble. These kinds of precursors have plenty of hydroxyl groups (-OH) which can strongly interact with the PEO segment of triblock copolymer templates via hydrogen bonds. The assembly of phenolic resins and copolymer templates occurs readily to form ordered mesostructures without macrophase separation. The preferential evaporation of ethanol progressively enriches the concentration of block copolymers and drives the organization of resol–copolymer composites into ordered liquid-crystalline mesophases. The mesostructures are dependent upon the hydrophilic/hydrophobic ratios in the resol-surfactant mesophases. The resol nanoparticles with sizes less than 1 nm are self-organized around the amphiphilic block copolymer templates instead of water. Cross-linkage of the resol nanoparticles may not be involved in this step, because resols are difficult to polymerize at room temperature under neutral conditions. Furthermore, the ordered resol–copolymer mesophases are thermopolymerized by the cross-linkage of resols, but without changing mesostructures. The 3-D network resin polymer nanostructures are formed via benzyl hydroxyl groups and non-substituted ortho- or para-carbons of benzene rings with covalent bonds. The PEO-PPO-PEO copolymer templates with high oxygen contents exhibit low thermal stability. By comparison, the stability of phenolic resins is much higher owing to the 3D network structures constructed by covalent bonds. Mesoporous polymers with large porosities are therefore obtained upon calcination at 350-500°C to remove templates. Further increasing the temperature leads to a framework transformation from polymers to carbons with ordered homologous mesostructures. This EISA strategy skillfully avoids the cooperatively assembling process between the precursor and surfactant template which facilitates the surfactant-templating assembly. It is quite different with the cooperative formation assembly mechanism, where the surfactant-templating assembly and polymerization of inorganic oligomers occur cooperatively and simultaneously.
1.2.4 Typical Ordered Mesoporous Silicas
1.2.4.1 2-D Hexagonal Mesoporous Silica Structures
The 2-D mesostructured materials with hexagonal symmetry are the most easily produced, the classical products being MCM-41, FSM-16, SBA-3 and SBA-15. The ideal models of basic structures are hexagonally closed packing cylindrical pore channels, belonging to the space group p6mm. Figure 1.5A shows the hexagonally symmetric pore arrays.
MCM-41 is one of the most simple and fully researched mesoporous silicates which can be synthesized in a wide range in a basic solution (pH = 9 - 13, optimal 11.5). The most used surfactant templates are cationic surfactants, i.e. long-chain alkyl ammonium, Cn H2n+1N(CH3)3+X- (n = 8-22, X = Br, Cl).
(Continues...)
Excerpted from Nanocasting by An-Hui Lu, Dongyuan Zhao, Ying Wan. Copyright © 2010 An-Hui Lu, Dongyuan Zhao and Ying Wan. Excerpted by permission of The Royal Society of Chemistry.
All rights reserved. No part of this excerpt may be reproduced or reprinted without permission in writing from the publisher.
Excerpts are provided by Dial-A-Book Inc. solely for the personal use of visitors to this web site.
Table of Contents
Chapter 1: Heat Capacities: Introduction, Concepts and Selected Applications; Chapter 2: Calorimetric Methods for Measuring Heat Capacities of Liquids and Liquid Solutions; Chapter 3: An Exact Analysis of Conductive Heat Losses in a Flow Calorimeter for Heat capacity Measurement; Chapter 4: Excess Heat Capacities and Related Properties of Liquid mixtures; Chapter 5: Heat Capacity of Non-Electrolyte Solutions; Chapter 6: Heat Capacities and Related Properties of Vapours and Vapour Mixtures; Chapter 7: Heat Capacity of Electrolyte Solutions; Chapter 8: Scanning Transitiometry and its Use to Determine Heat Capacities of Liquids at High Pressures; Chapter 9: Chapter 9 Sound Speed Measurements and Heat Capacities of gases; Chapter 10: Speed of Sound Measurements and Heat Capacities of Liquid Systems at High Pressure; Chapter 11: Heat Capacities and Brillouin Scattering in Liquids; Chapter 12: Photothermal Techniques for Heat Capacities; Chapter 13: High Resolution Adiabatic Scanning Calorimetry and Heat Capacities; Chapter 14: Heat Capacities in the Critical Region; Chapter 15: Heat Capacity of Polymeric Systems; Chapter 16: Protein Heat Capacity; Chapter 17: Specific Heat in Liquid Crystals; Chapter 18: Heat Capacities and Phase Transitions for the Dynamic Chemical Systems: Conformers, Tautomers, Plastic Crystals and Ionic Liquids; Chapter 19: The Estimation of Heat Capacities of Pure Liquids; Chapter 20: Computer Simulation Studies of Heat Capacity Effects Associated with Hydrophobic Effects; Chapter 21: Partial Molar Heat Capacities of Gases Dissolved in Liquid; Chapter 22: Heat Capacities of Molten SaltsWhat People are Saying About This
"This book features 22 chapters from an international team of acknowledged experts from a variety of disciplines who describe the current state of the art in heat capacities related to liquids, solutions and vapours."