Damage Mechanics in Metal Forming: Advanced Modeling and Numerical Simulation / Edition 1 available in Hardcover, eBook
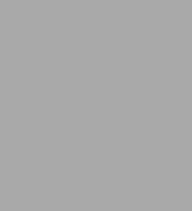
Damage Mechanics in Metal Forming: Advanced Modeling and Numerical Simulation / Edition 1
- ISBN-10:
- 1848213484
- ISBN-13:
- 9781848213487
- Pub. Date:
- 05/21/2012
- Publisher:
- Wiley
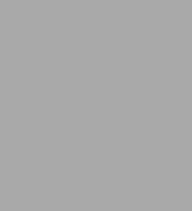
Damage Mechanics in Metal Forming: Advanced Modeling and Numerical Simulation / Edition 1
Buy New
$303.95Overview
Contents
1. Elements of Continuum Mechanics and Thermodynamics.2. Thermomechanically-Consistent Modeling of the Metals Behavior with Ductile Damage.3. Numerical Methods for Solving Metal Forming Problems.4. Application to Virtual Metal Forming.
Product Details
ISBN-13: | 9781848213487 |
---|---|
Publisher: | Wiley |
Publication date: | 05/21/2012 |
Series: | ISTE Series , #614 |
Pages: | 544 |
Product dimensions: | 6.40(w) x 9.20(h) x 1.40(d) |
About the Author
Table of Contents
Preface xiii
Principle of Mathematical Notations xix
Chapter 1 Elements of Continuum Mechanics and Thermodynamics 1
1.1 Elements of kinematics and dynamics of materially simple continua 2
1.1.1 Homogeneous transformation and gradient of transformation 2
1.1.1.1 Homogeneous transformation 2
1.1.1.2 Gradient of transformation and its inverse 4
1.1.1.3 Polar decomposition of the transformation gradient 5
1.1.2 Transformation of elementary vectors, surfaces and volumes 5
1.1.2.1 Transformation of an elementary vector 6
1.1.2.2 Transformation of an elementary volume: the volume dilatation 6
1.1.2.3 Transformation of an oriented elementary surface 7
1.1.3 Various definitions of stretch, strain and strain rates 8
1.1.3.1 On some definitions of stretches 8
1.1.3.2 On some definitions of the strain tensors 10
1.1.3.3 Strain rates and rotation rates (spin) tensors 15
1.1.3.4 Volumic dilatation rate, relative extension rate and angular sliding rate 17
1.1.4 Various stress measures 19
1.1.5 Conjugate strain and stress measures 23
1.1.6 Change of referential or configuration and the concept of objectivity 23
1.1.6.1 Impact on strain and strain rates 24
1.1.6.2 Impact on stress and stress rates 26
1.1.6.3 Impact on the constitutive equations 29
1.1.7 Strain decomposition into reversible and irreversible parts 30
1.2 On the conservation laws for the materially simple continua 33
1.2.1 Conservation of mass: continuity equation 33
1.2.2 Principle of virtual power: balance equations 34
1.2.3 Energy conservation. First law of thermodynamics 36
1.2.4 Inequality of the entropy. Second law of thermodynamics 37
1.2.5 Fundamental inequalities of thermodynamics 38
1.2.6 Heat equation deducted from energy balance 39
1.3 Materially simple continuum thermodynamics and the necessity of constitutive equations 39
1.3.1 Necessity of constitutive equations 40
1.3.2 Some fundamental properties of constitutive equations 41
1.3.2.1 Principle of determinism or causality axiom 42
1.3.2.2 Principle of local action 42
1.3.2.3 Principle of objectivity or material indifference 42
1.3.2.4 Principle of material symmetry 43
1.3.2.5 Principle of consistency 43
1.3.2.6 Thermodynamic admissibility 44
1.3.3 Thermodynamics of irreversible processes. The local state method 44
1.3.3.1 A presentation of the local state method 44
1.3.3.2 Internal constraints 52
1.4 Mechanics of generalized continua. Micromorphic theory 55
1.4.1 Principle of virtual power for micromorphic continua 58
1.4.2 Thermodynamics of micromorphic continua 59
Chapter 2 Thermomechanically-Consistent Modeling of the Metals Behavior with Ductile Damage 63
2.1 On the main schemes for modeling the behavior of materially simple continuous media 64
2.2 Behavior and fracture of metals and alloys: some physical and phenomenological aspects 69
2.2.1 On the microstructure of metals and alloys 69
2.2.2 Phenomenology of the thermomechanical behavior of polycrystals 70
2.2.2.1 Linear elastic behavior 71
2.2.2.2 Inelastic behavior 72
2.2.2.3 Inelastic behavior sensitive to the loading rate 74
2.2.2.4 Initial and induced anisotropies 76
2.2.2.5 Other phenomena linked to the shape of the loading paths 77
2.2.3 Phenomenology of the inelastic fracture of metals and alloys 82
2.2.3.1 Micro-defects nucleation 84
2.2.3.2 Micro-defects growth 85
2.2.3.3 Micro-defects coalescence and final fracture of the RVE 85
2.2.3.4 A first definition of the damage variable 86
2.2.3.5 From ductile damage at a material point to the total fracture of a structure by propagation of macroscopic cracks 89
2.2.4 Summary of the principal phenomena to be modeled 90
2.3 Theoretical framework of modeling and main hypotheses 91
2.3.1 The main kinematic hypotheses 91
2.3.1.1 Choice of kinematics and compliance with the principle of objectivity 92
2.3.1.2 Decomposition of strain rates 94
2.3.1.3 On some rotating frame choices 99
2.3.2 Implementation of the local state method and main mechanical hypotheses 102
2.3.2.1 Choice of state variables associated with phenomena being modeled 103
2.3.2.2 Definition of effective variables: damage effect functions 108
2.4 State potential: state relations 113
2.4.1 State potential in case of damage anisotropy 114
2.4.1.1 Formulation in strain space: Helmholtz free energy 114
2.4.1.2 Formulation in stress space: Gibbs free enthalpy 121
2.4.2 State potential in the case of damage isotropy 124
2.4.2.1 Formulation in strain space: Helmholtz free energy 124
2.4.2.2 Formulation in stress space: Gibbs free enthalpy 128
2.4.3 Microcracks closure: quasi-unilateral effect 129
2.4.3.1 Concept of micro-defect closure: deactivation of damage effects 129
2.4.3.2 State potential with quasi-unilateral effect 132
2.5 Dissipation analysis: evolution equations 139
2.5.1 Thermal dissipation analysis: generalized heat equation 140
2.5.1.1 Heat flux vector: Fourier linear conduction model 141
2.5.1.2 Generalized heat equation 141
2.5.2 Intrinsic dissipation analysis: case of time-independent plasticity 143
2.5.2.1 Damageable plastic dissipation: anisotropic damage with two yield surfaces 144
2.5.2.2 Damageable plastic dissipation: anisotropic damage with a single yield surface 157
2.5.2.3 Incompressible and damageable plastic dissipation: isotropic damage with two yield surfaces 162
2.5.2.4 Incompressible and damageable plastic dissipation: single yield surface 169
2.5.3 Intrinsic dissipation analysis: time-dependent plasticity or viscoplasticity 174
2.5.3.1 Damageable viscoplastic dissipation without restoration: anisotropic damage with two viscoplastic potentials 176
2.5.3.2 Viscoplastic dissipation with damage: isotropic damage with a single viscoplastic potential and restoration 182
2.5.4 Some remarks on the choice of rotating frames 186
2.5.5 Modeling some specific effects linked to metallic material behavior 189
2.5.5.1 Effects on non-proportional loading paths on strain hardening evolution 190
2.5.5.2 Strain hardening memory effects 191
2.5.5.3 Cumulative strains or ratchet effect 191
2.5.5.4 Yield surface and/or inelastic potential distortion 192
2.5.5.5 Viscosity-hardening coupling: the Piobert-Lüders peak 192
2.5.5.6 Accounting for the material microstructure 193
2.5.5.7 Some specific effects on ductile fracture 193
2.6 Modeling of the damage-induced volume variation 194
2.6.1 On the compressibility induced by isotropic ductile damage 195
2.6.1.1 Concept of volume damage 195
2.6.1.2 State coupling and state relations 196
2.6.1.3 Dissipation coupling and evolution equations 197
2.7 Modeling of the contact and friction between deformable solids 200
2.7.1 Kinematics and contact conditions between solids 201
2.7.1.1 Impenetrability condition 203
2.7.1.2 Equilibrium condition of contact interface 204
2.7.1.3 Contact surface non-adhesion condition 205
2.7.1.4 Contact unilaterality condition 205
2.7.2 On the modeling of friction between solids in contact 206
2.7.2.1 Time-independent friction model 206
2.8 Nonlocal modeling of damageable behavior of micromorphic continua 215
2.8.1 Principle of virtual power for a micromorphic medium: balance equations 217
2.8.2 State potential and state relations for a micromorphic solid 218
2.8.3 Dissipation analysis: evolution equations for a micromorphic solid 221
2.8.4 Continuous tangent operators and thermodynamic admissibility for a micromorphic solid 223
2.8.5 Transformation of micromorphic balance equations 224
2.9 On the micro-macro modeling of inelastic flow with ductile damage 226
2.9.1 Principle of the proposed meso-macro modeling scheme 227
2.9.2 Definition of the initial RVE 230
2.9.3 Localization stages 230
2.9.4 Constitutive equations at different scales 233
2.9.4.1 State potential and state relations 233
2.9.4.2 Intrinsic dissipation analysis: evolution equations 235
2.9.5 Homogenization and the mean values of fields at the aggregate scale 239
2.9.6 Summary of the meso-macro polycrystalline model 240
Chapter 3 Numerical Methods for Solving Metal Forming Problems 243
3.1 Initial and boundary value problem associated with virtual metal forming processes 244
3.1.1 Strong forms of the initial and boundary value problem 245
3.1.1.1 Posting a fully coupled problem 245
3.1.1.2 Some remarks on thermal conditions at contact interfaces 250
3.1.2 Weak forms of the initial and boundary value problem 252
3.1.2.1 On the various weak forms of the IBVP 252
3.1.2.2 Weak form associated with equilibrium equations 254
3.1.2.3 Weak form associated with heat equation 257
3.1.2.4 Weak form associated with micromorphic damage balance equation 258
3.1.2.5 Summary of the fully coupled evolution problem 258
3.2 Temporal and spatial discretization of the IBVP 259
3.2.1 Time discretization of the IBVP 259
3.2.2 Spatial discretization of the IBVP by finite elements 260
3.2.2.1 Spatial semi-discretization of the weak forms of the IBVP 260
3.2.2.2 Examples of isoparametric finite elements 266
3.3 On some global resolution scheme of the IBVP 270
3.3.1 Implicit static global resolution scheme 272
3.3.1.1 Newton-Raphson scheme for the solution of the fully coupled IBVP 273
3.3.1.2 On some convergence criteria 275
3.3.1.3 Calculation of the various terms of the tangent matrix 276
3.3.1.4 The purely mechanical consistent Jacobian matrix 280
3.3.1.5 Implicit global resolution scheme of the coupled IBVP 282
3.3.2 Dynamic explicit global resolution scheme 284
3.3.2.1 Solution of the mechanical problem 284
3.3.2.2 Solution of thermal (parabolic) problem 286
3.3.2.3 Solution of micromorphic damage problem 288
3.3.2.4 Sequential scheme of explicit global resolution of the IBVP 288
3.3.3 Numerical handling of contact-friction conditions 291
3.3.3.1 Lagrange multiplier method 293
3.3.3.2 Penalty method 295
3.3.3.3 On the search for contact nodes 296
3.3.3.4 On the numerical handling of the incompressibility condition 300
3.4 Local integration scheme: state variables computation 304
3.4.1 On numerical integration using the Gauss method 304
3.4.2 Local integration of constitutive equations: computation of the stress tensor and the state variables 305
3.4.2.1 On the numerical integration of first-order ODEs 306
3.4.2.2 Choice of constitutive equations to integrate 308
3.4.2.3 Integration of time-independent plastic constitutive equations: the case of a von Mises isotropic yield criterion 313
3.4.2.4 Integration of time-independent plastic constitutive equations: the case of a Hill quadratic anisotropic yield criterion 326
3.4.2.5 Integration of the constitutive equation in the case of viscoplastic flow 328
3.4.2.6 Calculation of the rotation tensor: incremental objectivity 333
3.4.2.7 Remarks on the integration of the micromorphic damage equation 335
3.4.3 On the local integration of friction equations 335
3.5 Adaptive analysis of damageable elasto-inelastic structures 337
3.5.1 Adaptation of time steps 339
3.5.2 Adaptation of spatial discretization or mesh adaptation 341
3.6 On other spatial discretization methods 347
3.6.1 An outline of non-mesh methods 348
3.6.2 On the FEM-meshless methods coupling 353
Chapter 4 Application to Virtual Metal Forming 355
4.1 Why use virtual metal forming? 356
4.2 Model identification methodology 359
4.2.1 Parametrical study of specific models 360
4.2.1.1 Choosing typical constitutive equations 360
4.2.1.2 Isothermal uniaxial tension (compression) load without damage 364
4.2.1.3 Accounting for ductile damage effect 383
4.2.1.4 Accounting for initial anisotropy in inelastic flow 396
4.2.2 Identification methodologies 413
4.2.2.1 Some general remarks on the issue of identification 414
4.2.2.2 Recommended identification methodology 416
4.2.2.3 Illustration of the identification methodology 422
4.2.2.4 Using a nonlocal model 429
4.3 Some applications 431
4.3.1 Sheet metal forming 431
4.3.1.1 Some deep drawing processes of thin sheets 432
4.3.1.2 Some hydro-bulging test of thin sheets and tubes 441
4.3.1.3 Cutting processes of thin sheets 447
4.3.2 Bulk metal forming processes 463
4.3.2.1 Classical bulk metal forming processes 463
4.3.2.2 Bulk metal forming processes under severe conditions 476
4.4 Toward the optimization of forming and machining processes 484
Appendix: Legendre-Fenchel Transformation 493
Bibliography 499
Index 515