5
1
9780198085492
Engineering Metrology and Measurements available in Paperback
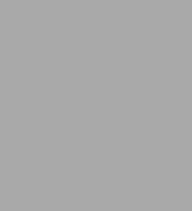
Engineering Metrology and Measurements
by Raghavendra, Krishnamurthy
Raghavendra
- ISBN-10:
- 0198085494
- ISBN-13:
- 9780198085492
- Pub. Date:
- 10/01/2013
- Publisher:
- Oxford University Press
- ISBN-10:
- 0198085494
- ISBN-13:
- 9780198085492
- Pub. Date:
- 10/01/2013
- Publisher:
- Oxford University Press
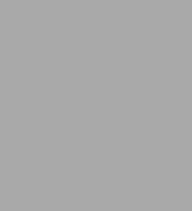
Engineering Metrology and Measurements
by Raghavendra, Krishnamurthy
Raghavendra
Paperback
$39.95
Current price is , Original price is $39.95. You
Buy New
$39.95
$39.95
-
SHIP THIS ITEM— Temporarily Out of Stock Online
-
PICK UP IN STORE
Your local store may have stock of this item.
Available within 2 business hours
Temporarily Out of Stock Online
39.95
Out Of Stock
Overview
Engineering Metrology and Measurements is a textbook designed for students of mechanical, production and allied disciplines to facilitate learning of various shop-floor measurement techniques and also understand the basics of mechanical measurements.
With a conventional introduction to the principles and standards of measurement, the book in subsequent chapters takes the reader through the important topics of metrology such as limits, fits and tolerances, linear measurements, angular measurements, comparators, optical measurements. The last few chapters discuss the measurement concepts of simple physical parameters such as force, torque, strain, temperature, and pressure, before introducing the contemporary information on nanometrology as the last chapter.
Adopting an illustrative approach to explain the concepts, the book presents solved numerical problems, practice problems, review questions, and multiple choice questions.
With a conventional introduction to the principles and standards of measurement, the book in subsequent chapters takes the reader through the important topics of metrology such as limits, fits and tolerances, linear measurements, angular measurements, comparators, optical measurements. The last few chapters discuss the measurement concepts of simple physical parameters such as force, torque, strain, temperature, and pressure, before introducing the contemporary information on nanometrology as the last chapter.
Adopting an illustrative approach to explain the concepts, the book presents solved numerical problems, practice problems, review questions, and multiple choice questions.
Product Details
ISBN-13: | 9780198085492 |
---|---|
Publisher: | Oxford University Press |
Publication date: | 10/01/2013 |
Pages: | 676 |
Product dimensions: | 7.20(w) x 9.40(h) x 0.90(d) |
About the Author
Raghavendra, N V, Krishnamurthy, L
Dr N V Raghavendra is a professor, Department of Mechanical Engineering, National Institute of Engineering, Mysore. Prof. Raghavendra was a member of the Implementation Committee of the prestigious VTU-Bosch Rexroth Centre of Automation Technology, Mysore. He also served as the Special Officer of the VTU-Bosch Rexroth Centre from September 2007 to December, 2008. Presently he is the Coordinator of CNC Training Centre of the Institute and Director of NIE-Eicher Centre for Automobile Technology.
Dr L Krishnamurthy is a professor, Department of Mechanical Engineering, National Institute of Engineering, Mysore. He co-investigates the research project titled "Characterization of Composite Materials and Application of Nanomaterials for Sustainable Energy", sanctioned by Nano Mission, Department of Science and Technology, Government of India.
Dr N V Raghavendra is a professor, Department of Mechanical Engineering, National Institute of Engineering, Mysore. Prof. Raghavendra was a member of the Implementation Committee of the prestigious VTU-Bosch Rexroth Centre of Automation Technology, Mysore. He also served as the Special Officer of the VTU-Bosch Rexroth Centre from September 2007 to December, 2008. Presently he is the Coordinator of CNC Training Centre of the Institute and Director of NIE-Eicher Centre for Automobile Technology.
Dr L Krishnamurthy is a professor, Department of Mechanical Engineering, National Institute of Engineering, Mysore. He co-investigates the research project titled "Characterization of Composite Materials and Application of Nanomaterials for Sustainable Energy", sanctioned by Nano Mission, Department of Science and Technology, Government of India.
Table of Contents
1. b1.1 Introduction1.2 Metrology Defined1.3 Need for Inspection1.4 Accuracy and Precision1.4.1 Accuracy and Cost1.5 Objectives of Metrology and Measurements1.6 General Measurement Concepts1.6.1 Calibration of Measuring Instruments1.7 Error in Measurements1.7.1 Systematic and Controllable Errors1.7.2 Random Errors1.8 Methods of Measurement2. b2.1 Introduction2.2 Standards and their Roles2.3 Evolution of Standards2.4 The National Physical Laboratory (NPL)2.5 Material Standard2.5.1 Yard2.5.2 Metre2.5.3. Disadvantages of Material Standard2.6 Wavelength Standard2.6.1 The Modern Metre2.7 Subdivisions of Standards2.8 Line and End Measurement2.8.1 Characteristics of Line Standards2.8.2 Characteristics of End Standards2.8.3 Transfer from Line Standard to End Standard2.9 Brookes Level Comparator2.10 Displacement Method2.11 Calibration of End Bars3. b3.1 Introduction3.2 Principle of Interchangeability3.2.1 Selective Assembly Approach3.3 Tolerances3.3.1 Computer Aided Modelling3.3.2 Manufacturing Cost and Work Tolerance3.3.3 Classification of Tolerances3.4 Maximum and Minimum Metal Conditions3.5 Fits3.5.1 Allowance3.5.2 Hole Basis and Shaft Basis System3.6 Systems of Limits and Fits3.6.1 General Terminologies3.6.2 Limit Gauging3.6.3 Classification of Gauges3.6.4 Taylor's Principle3.6.5 Important guidelines for gauge design3.6.6 Material for Gauges3.6.7 Gauge Tolerance3.6.8 Wear Allowance3.6.9 Methods of Tolerance Specification on Gauges3.7 Plain Plug Gauges3.8 Snap Gauges4. b4.1 Introduction4.2 Design of Linear Measurement Instruments4.3 Surface Plate4.4 V Blocks4.5 Graduated Scales4.6 Scaled Instruments4.6.1 Depth Gauge4.6.2 Combination Set4.6.3 Calipers4.7 Vernier Instruments4.7.1 Vernier Calipers4.7.2 Vernier Depth Gauge4.7.3 Vernier Height Gauge4.8 Micrometer Instruments4.8.1 Outside Micrometer4.8.2 Vernier Micrometer4.8.3 Digital Micrometer4.8.4 Inside Micrometer Caliper4.8.5 Inside Micrometer4.8.6 Depth Micrometer4.8.7 Floating Carriage Micrometer4.9 Slip Gauges4.9.1 Gauge Block Shapes, Grades and Sizes4.9.2 Wringing of Slip Gauges4.9.3 Manufacture of Slip Gauges4.9.4 Calibration of Slip Gauges5. b5.1 Introduction5.2 Protractor5.2.1 Universal Bevel Protractor5.2.2 Optical Bevel Protractor5.3 Sine Bar5.3.1 Sine Blocks, Sine Plates, and Sine Tables5.3.2 Sine Centre5.4 Angle Gauges5.4.1 Uses of Angle Gauges5.4.2 Manufacture and calibration of angle gauges5.4.3 True Square5.5 Spirit Level5.5.1 Clinometer5.6 Optical Instruments for Angular Measurement5.6.1 Autocollimator5.6.2 Autocollimator Applications5.6.3 Angle Dekkor6. b6.1 Introduction6.2 Functional Requirements6.3 Classification of Comparators6.4 Mechanical Comparators6.4.1 Dial Indicators6.4.2 Johansson Microkator6.4.3 Sigma Comparator6.5 Mechanical Optical Comparator6.5.1 Zeiss Ultra Optimeter6.5.2 Optical Projector6.6 Electrical and Electronic Comparators6.6.1 LVDT6.6.2 Electronic Comparator6.7 Pneumatic Comparator6.7.1 Free Flow Air Gauge6.7.2 Back Pressure Gauge6.7.3 Solex Pneumatic Gauge6.7.4 Applications of Pneumatic Comparators7. b7.1 Introduction7.2 Optical Measurement Techniques7.2.1 Tool Maker's Microscope7.2.2 Profile Projector7.2.3 Optical Squares7.3 Optical Interference7.4 Interferometry7.4.1 Optical Flats7.5 Interferometers7.5.1 The NPL Flatness Interferometer7.5.2 Pitter-NPL Gauge Interferometer7.5.3 Laser Interferometers7.6 Scales, Grating, and Reticles7.6.1 Scales7.6.2 Gratings7.6.3 Reticles8. b8.1 Introduction8.2 Gear Terminology8.3 Error in Spur Gears8.4 Measurement of Gear Elements8.5 Composite Method of Gear Inspection8.5.1 Parkinson Gear Tester8.6 Measurement of Screw Threads8.7 Screw Thread Terminology8.8 Measurement of Screw Thread Elements8.8.1 Measurement of Major Diameter8.8.2 Measurement of Minor Diameter8.8.3 Measurement of Effective Diameter8.8.4 Measurement of Pitch8.9 Thread Gauges9. b9.1 Introduction9.2 Surface Metrology Concepts9.3 Terminologies9.4 Analysis of Surface Traces9.4.1 Ten Point Height Average Value9.4.2 Root Mean Square Value9.4.3 Central Line Average Value9.5 Specification of Surface Texture Characteristics9.6 Methods of Measuring Surface Finish9.7 Stylus System of Measurement9.7.1 The Stylus and Datum9.8 Stylus Probe Instruments9.8.1 Tomlinson Surface Meter9.8.2 Taylor-Hobson Talysurf9.8.3 Profilometer9.9 Wavelength, Frequency, and Cutoff9.10 Other Methods of Measuring Surface Roughness9.10.1 Pneumatic Method9.10.2 Light Interference Microscope9.10.3 Mecrin Instrument10. b10.1 Introduction10.2 Precision Instrumentation based on Laser Principles10.3 Coordinate Measuring Machines (CMM)10.3.1 Structure of CMM10.3.2 Modes of Operation10.3.3 The Probe10.3.4 Operation of CMM10.3.5 Major Applications of CMM10.4 Machine Tool Metrology10.4.1 Straightness, Flatness, Parallelism, Squareness, Roundness, Cylindricity, and Runout10.4.2 Acceptance Test for Machine Tools10.5 Automated Inspection10.6 Machine Vision10.6.1 Stages of Machine Vision10.6.2 Applications of Machine Vision in Inspection11. b11.1 Introduction11.2 Inspection11.3 Specifying the Limits of Variability11.4 Dimensions and Tolerances11.5 Selection of Gauging Equipment11.6 Gauge Control11.7 Quality Control and Quality Assurance11.8 Statistical Quality Control11.8.1 Process Variability11.8.2 Importance of Sampling11.8.3 SQC by Attributes11.8.4 SQC by Variables11.9 Total Quality Management11.9.1 Customer Focus11.9.2 Continuous Improvement11.9.3 Employee Empowerment11.9.4 Use of Quality Tools11.9.5 Product Design11.9.6 Process Management11.9.7 Managing Supplier Quality11.10 Six Sigma11.10.1 Six Sigma Approach11.10.2 Training for Six Sigma11.11 Quality Standards11.11.1 Quality Management Principles of ISO 900011.11.2 Implementing ISO Standards12. b12.1 Introduction12.2 Some Basic Definitions12.2.1 Hysteresis in Measurement Systems12.2.2 Linearity in Measurement Systems12.2.3 Resolution of Measuring Instruments12.2.4 Threshold12.2.5 Drift12.2.6 Zero Stability12.2.7 Loading Effects12.2.8 System Response12.3 Functional Elements of Measurement Systems12.4 Primary Detector-Transducer Stage12.5 The Intermediate Modifying Stage12.6 The Output or Terminating Stage13. b13.1 Introduction13.2 Transfer Efficiency13.3 Classification of Transducers13.3.1 Primary and Secondary Transducers13.3.2 Based on Principles of Transduction13.3.3 Active and Passive Transducers13.3.4 Analog and Digital Transducers13.3.5 Transducers and Inverse Transducers13.3.6 Null and Deflection Type Transducers13.4 Quality Attributes for Transducers13.5 Intermediate Modifying Devices13.5.1 Inherent Problems in Mechanical Systems13.5.2 Kinematic Linearity13.5.3 Mechanical Amplification13.5.4 Reflected Frictional Amplification13.5.5Reflected Inertial Amplification13.5.6 Amplification of Backlash and Elastic Deformation13.5.7 Tolerance Problems13.5.8 Temperature Problems13.6 Electrical Intermediate Modifying Devices13.6.1 Input Circuitry13.6.2 Simple Current Sensitive Circuit13.6.3 Ballast Circuit13.6.4 Electronic Amplifiers13.6.5 Telemetry13.7 Advantages of Electrical Intermediate Modifying Devices13.8 Terminating Devices13.8.1 Metering Indicators13.8.2 Mechanical Counters13.8.3 Cathode Ray Oscilloscope (CRO)13.8.4 Oscillographs13.8.5 X-Y Plotters13.8.6 Stroboscopic Measurements14. b14.1 Introduction14.2 Measurement of Force14.2.1 Direct Methods14.3 Elastic Members14.3.1 Load Cells14.3.2 Cantilever Beams14.3.3 Proving Rings14.3.4 Differential Transformers14.4 Measurement of Torque14.4.1 Torsion Bar Dynamometer14.4.2 Servo Controlled Dynamometers14.4.3 Absorption Dynamometers14.5 Measurement of Strain14.5.1 Mechanical Strain Gauges14.5.2 Electrical Strain Gauges14.6 Strain Gauge Materials14.7 Backing or Carrier Materials14.9 Adhesives14.10 Protective Coatings14.11 Bonding of Gauges14.12 Gauge Factor14.13 Theory of Strain Gauges14.14 Methods of Strain Measurements14.15 Strain Gauge Bridge Arrangement14.16 Temperature Compensation in Strain Gauges14.16.1 Adjacent Arm Compensating Gauges14.16.2 Self Temperature Compensation15. b15.1 Introduction15.2 Methods of Measuring Temperature15.3 Thermocouples15.3.1 Law of Thermocouples15.3.2 Thermocouple Materials15.3.3 Thermopiles15.4 Resistance Temperature Detectors (RTD)15.5 Thermistors15.6 Liquid In Glass Thermometers15.7 Pressure Thermometers15.8 Bimetallic Strip Thermometers15.9 Pyrometry15.9.1 Total Radiation Pyrometer15.9.2 Optical Pyrometer15.9.3 Fibre Optic Pyrometers16. b16.1 Introduction16.2 Pressure Measurement Scales16.3 Methods of Pressure Measurement16.3.1 Static Pressure Measurement16.3.2 Classification of Pressure Measuring Devices16.3.3 Manometers for Pressure Measurement16.4 Ring Balance16.5 Inverted Bell Manometer16.6 Elastic Transducers16.7 Elastic Pressure Transducers16.7.1 Resistance Type Transducers16.7.2 Potentiometer Devices16.7.3 Inductive Type Transducer16.7.4 Capacitive Type Pressure Transducer16.7.5 Piezo Electric Type Pressure Transducer16.7.6 Varying Pressure Measurement16.8 Dead Weight Pressure Gauge16.9 Measurement of Vacuum16.9.1 McLeod Gauge16.9.2 Pirani Gauge16.9.3 Ionization Gauge16.9.4 Knudsen Gauge16.10 Measurement of High Pressure17. b17.1 Introduction17.2 Nanotechnology17.2.1 Importance of Nano Dimension17.2.1 Classification of Nanostructures17.2.3 Applications17.3 Importance of Nanometrology17.4 Introduction to Microscopy17.4.1 Transmission Electron Microscope (TEM)17.4.2 Scanning Electron Microscope (SEM)17.4.3 Scanning Tunnelling Microscope (STM)17.4.4 Atomic Force Microscope (AFM)17.5 X-ray Diffraction System (XRD)iAppendix A: Universal Measuring Machine/iiAppendix B: Fluid Flow Measurements/iiAppendix C: Laboratory Manual/iiAppendix D: Quality Control Charts/iFrom the B&N Reads Blog
Page 1 of