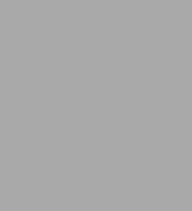
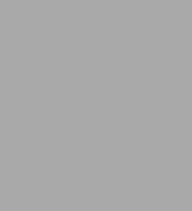
Paperback(2nd ed.)
-
PICK UP IN STORECheck Availability at Nearby Stores
Available within 2 business hours
Related collections and offers
Overview
Product Details
ISBN-13: | 9783110418033 |
---|---|
Publisher: | De Gruyter |
Publication date: | 05/24/2016 |
Series: | De Gruyter Textbook |
Edition description: | 2nd ed. |
Pages: | 352 |
Product dimensions: | 6.69(w) x 9.45(h) x (d) |
Age Range: | 18 Years |
About the Author
Table of Contents
About the authors v
1 Risk management is not only a matter of financial risk 1
References 7
2 Introduction to engineering and managing risks 9
2.1 Managing risks and uncertainties - an introduction 9
2.2 The complexity of risks and uncertainties 13
2.3 Hazards and risks 17
2.4 Simplified interpretation of (negative) risk 19
2.5 Hazard and risk mapping 22
2.6 Risk perception and risk attitude 25
2.7 ERM - main steps 27
2.8 Objectives and importance of ERM 33
2.9 The Black Swan (type III events) 34
2.10 Conclusions 36
References 36
3 Risk management principles 39
3.1 Introduction to risk management 39
3.2 Integrated risk management 41
3.3 Risk management models 43
3.3.1 Model of the accident pyramid 43
3.3.2 The P2T model 46
3.3.3 The Swiss cheese model and the domino theory 46
3.4 The anatomy of an accident: SIFs and SILs 49
3.5 Individual risk, societal risk, physical description of risk 57
3.5.1 Location-based (individual) risk 57
3.5.2 Societal risk or group risk 58
3.5.3 Physical description of risk 62
3.5.3.1 Static model of an accident 64
3.5.3.2 Dynamic model of an accident 64
3.6 Safety culture and safety climate 66
3.6.1 Organizational culture and climate 66
3.6.2 Safety culture models 68
3.6.3 The P2T model revisited and applied to safety and security culture 71
3.6.4 The Egg Aggregated Model (TEAM) of safety culture 73
3.7 Strategic management concerning risks and continuous improvement 75
3.8 The IDEAL S&S model 77
3.8.1 Performance indicators 82
3.9 Continuous improvement of organizational culture 86
3.10 High reliability organizations and systemic risks 88
3.10.1 Systems thinking 88
3.10.1.1 Reaction time or retard ant effect 88
3.10.1.2 Law of communicating vessels 88
3.10.1.3 Non-linear causalities 89
3.10.1.4 Long-term vision 89
3.10.1.5 Systems thinking conclusions 89
3.10.2 Normal accident theory (NAT) and high reliability theory (HRT) 90
3.10.3 High reliability organization (HRO) principles 92
3.10.3.1 HRO principle 1: targeted at disturbances 93
3.10.3.2 HRO principle 2: reluctant for simplification 93
3.10.3.3 HRO principle 3: sensitive towards implementation 93
3.10.3.4 HRO principle 4: devoted to resiliency 94
3.10.3.5 HRO principle 5: respectful for expertise 94
3.10.4 Risk and reliability 94
3.11 Accident reporting 96
3.12 Conclusions 98
References 99
4 Risk diagnostic and analysis 103
4.1 Introduction to risk assessment techniques 103
4.1.1 Inductive and deductive approaches 104
4.1.2 General methods for risk analysis 105
4.1.3 General procedure 111
4.1.4 General process for all analysis techniques 113
4.2 SWOT 114
4.3 Preliminary hazard analysis 117
4.4 Checklist 119
4.4.1 Methodology 119
4.4.2 Example 120
4.4.2.1 Step 1a: Critical difference, effect of energies failures 121
4.4.2.2 Step 1b: Critical difference, deviation from the operating procedure 121
4.4.2.3 Step 2: Establish the risk catalogue 122
4.4.2.4 Step 3: risk mitigation 123
4.4.3 Conclusion 123
4.5 HAZOP 123
4.5.1 HAZOP inputs and outputs 124
4.5.2 HAZOP process 125
4.5.3 Example 126
4.5.4 Conclusions 128
4.6 FMECA 131
4.6.1 FMECA inputs and outputs 132
4.6.2 FMECA process 132
4.6.2.1 Step 1: Elaboration of the hierarchical model, functional analysis 134
4.6.2.2 Step 2: Failure mode determination 135
4.6.2.3 Step 3: The criticality determination 136
4.6.3 Example 137
4.6.4 Conclusions 140
4.7 Fault tree analysis and event tree analysis 141
4.7.1 Fault tree analysis 141
4.7.2 Event tree analysis 146
4.7.3 Cause-consequence-analysis (CCA): a combination of FTA and ETA 147
4.8 The risk matrix 151
4.9 Quantitative risk assessment (QRA) 156
4.10 Layer of protection analysis 158
4.11 Bayesian networks 161
4.12 Conclusion 165
References 166
5 Risk treatment/reduction 169
5.1 Introduction 169
5.2 Prevention 174
5.2.1 Seveso Directive as prevention means for chemical plants 175
5.2.2 Seveso company tiers 179
5.3 Protection and mitigation 180
5.4 Risk treatment 184
5.5 Risk control 189
5.6 STOP principle 192
5.7 Resilience 195
5.8 Conclusion 198
References 199
6 Event analysis 201
6.1 Traditional analytical techniques 202
6.1.1 Sequence of events 203
6.1.2 Multilinear events sequencing 203
6.1.3 Root cause analysis 204
6.2 Causaltree analysis 205
6.2.1 Method description 205
6.2.2 Collecting facts 207
6.2.3 Event investigation good practice 209
6.2.4 Building the tree 210
6.2.5 Example 213
6.2.6 Building an action plan 214
6.2.7 Implementing solutions and follow-up 215
6.3 Conclusions 215
References 216
7 Major industrial accidents and teaming from accidents 217
7.1 Link between major accidents and legislation 217
7.2 Major industrial accidents; examples 219
7.2.1 Feyzin, France, January 1966 219
7.2.2 Flixborough, UK, June 1974 220
7.2.3 Seveso, Italy, July 1976 221
7.2.4 Los Alfaques, Spain, July 1978 221
7.2.5 Mexico City, Mexico, November 1984 222
7.2.6 Bhopal, India, December 1984 222
7.2.7 Chernobyl, Ukraine, April 1986 223
7.2.8 Piper Alpha, North Sea, July 1988 223
7.2.9 Pasadena, Texas, USA, October 1989 224
7.2.10 Enschede, The Netherlands, May 2000 224
7.2.11 Toulouse, France, September 2001 224
7.2.12 Ath, Belgium, July 2004 225
7.2.13 Houston, Texas, USA, March 2005 225
7.2.14 St Louis, Missouri, USA, June 2005 225
7.2.15 Buncefield, UK, December 2005 226
7.2.16 Port Wenworth, Georgia, USA, February 2008 226
7.2.17 Deepwater Horizon, Gulf of Mexico, April 2010 227
7.2.18 Fukushima, Japan, March 2011 227
7.2.19 West, Texas, USA, April, 2013 228
7.2.20 La Porte, Texas, USA, November, 2014 228
7.2.21 Tianjin, China, August, 2015 229
7.3 Learning from accidents 229
7.4 Conclusions 232
References 232
8 Crisis management 235
8.1 Introduction 236
8.2 The steps of crisis management 238
8.2.1 What to do when a disruption occurs 239
8.2.2 Business continuity plan 244
8.3 Crisis evolution 245
8.3.1 The pre-crisis stage or creeping crisis 246
8.3.2 The acute-crisis stage 247
8.3.3 The post-crisis stage 247
8.3.4 Illustrative example of a crisis evolution 247
8.4 Proactive or reactive crisis management 249
8.5 Crisis communication 250
8.6 Conclusions 251
References 252
9 Economic issues of safety 253
9.1 Accident costs and hypothetical benefits 255
9.2 Prevention costs 259
9.3 Prevention benefits 260
9.4 The degree of safety and the minimum total cost point 261
9.5 Safety economics and the two different types of risks 262
9.6 Cost-effectiveness analysis and cost-benefit analysis for occupational (type I) accidents 264
9.6.1 Cost-effectiveness analysis 264
9.6.2 Cost-benefit analysis 265
9.6.2.1 Decision rule, present values and discount rate 267
9.6.2.2 Disproportion factor 270
9.6.2.3 Different cost-benefit ratios 271
9.6.2.4 Cost-benefit analysis for safety measures 271
9.6.3 Risk acceptability 272
9.6.4 Using the event tree to decide about safety investments 276
9.6.5 Advantages and disadvantages of analyses based on costs and benefits 277
9.7 Optimal allocation strategy for the safety budget 278
9.8 Loss aversion and safety investments - safety as economic value 279
9.9 Conclusions 280
References 280
10 Risk governance 283
10.1 Introduction 283
10.2 Risk management system 285
10.3 A framework for risk and uncertainty governance 290
10.4 The risk governance model (RGM) 296
10.4.1 The "considering?" layer of the risk governance model 297
10.4.2 The "results?" layer of the risk governance model 299
10.4.3 The risk governance model 299
10.5 A risk governance PDCA 300
10.6 Risk governance deficits 302
10.7 Conclusions 304
References 305
11 Examples of practical implementation of risk management 307
11.1 The MICE concept 308
11.1.1 The management step 309
11.1.2 The information and education step 309
11.1.3 The control step 310
11.1.4 The emergency step 310
11.2 Application to chemistry research and chemical hazards 310
11.3 Application to physics research and physics hazards 312
11.3.1 Hazards of liquid cryogens 313
11.3.2 Asphyxiation 316
11.4 Application to emerging technologies 317
11.4.1 Nanotechnologies as illustrative example 320
11.5 Conclusions 323
References 325
12 Concluding remarks 327
Index 331