Machine Designers Reference / Edition 1 available in Hardcover, eBook
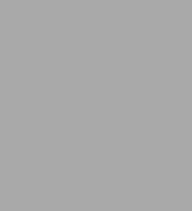
- ISBN-10:
- 0831134321
- ISBN-13:
- 9780831134327
- Pub. Date:
- 10/21/2011
- Publisher:
- Industrial Press, Inc.
- ISBN-10:
- 0831134321
- ISBN-13:
- 9780831134327
- Pub. Date:
- 10/21/2011
- Publisher:
- Industrial Press, Inc.
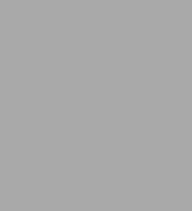
Buy New
$119.95Overview
The author’s pragmatic intention with Machine Designers Reference is a volume that supports and compliments today’s software programs and the Internet links most commonly relied upon by mechanical designers in the field. At the same time, the book is exceptionally useful to mechanical engineering students and fresh graduates seeking to excel at the curriculum or advance their career in design. Machine Designers Reference complements the coverage offered by standard textbooks in the field. It serves effectively as a bridge between the academic experience and practical design employment in the industry.
Features
- One-of-a-kind tool speeds mechanical design work
- Selection, sizing and tolerances for mechanical parts and assemblies
- Concise best practices for mechanical design, supported by charts and tables
- U.S. and metric units are presented for reader convenience
- Thorough representation of metric hardware
Product Details
ISBN-13: | 9780831134327 |
---|---|
Publisher: | Industrial Press, Inc. |
Publication date: | 10/21/2011 |
Pages: | 672 |
Product dimensions: | 8.20(w) x 10.10(h) x 1.50(d) |
Age Range: | 18 Years |
About the Author
Read an Excerpt
EXCERPT from CHAPTER 10 BEARINGS10.1 Plain Bearings Plain bearings provide sliding contact between two surfaces. The most common type of plain bearing is the sleeve bearing or bushing. Plain bearings are often chosen over rolling element bearings due to cost or space limitations. They are also more rigid and quieter in operation than rolling element bearings. The main disadvantages of plain bearings are their higher potential to wear (as compared to rolling element bearings) as well as their relative vulnerability to contaminants. This section serves as a general introduction to plain bearings, with a focus on sleeve bearings used in rotary motion applications with boundary lubrication conditions. Please consult the recommended resources for more information and calculation methods for other types of lubrication. Plain bearings used in linear motion applications are discussed in Section 10.3.Lubrication of Plain Bearings Plain bearings must be lubricated in order to have long life and low friction. There are four types of lubrication conditions under which plain bearings are run: hydrostatic lubrication (full film), hydrodynamic lubrication (full film), mixed film lubrication, and boundary lubrication (thin film). Full film lubrication occurs when the lubricant layer between surfaces is thick enough to prevent any surface contact. Boundary lubrication occurs when the lubricant layer is present but not thick enough to prevent contact between surfaces. A graph showing relative coefficients of friction for the different types of lubrication are shown in Figure 10-1. The horizontal axis is a function of lubricant viscosity (Z), journal speed (N), and bearing pressure (P).
Recommended Resources • R. Mott, Machine Elements in Mechanical Design, 5th Ed., Pearson/Prentice Hall, Inc., Upper Saddle River, NJ, 2012 • R. L. Norton, Machine Design: An Integrated Approach, 4th Ed., Prentice Hall, Upper Saddle River, NJ, 2011 • Oberg, Jones, Horton, Ryffel, Machinery’s Handbook, 28th Ed., Industrial Press, New York, NY, 2008
Hydrostatic lubrication is full film lubrication, and occurs when high pressure lubricant is used to force the sliding surfaces apart. Plain bearings with hydrostatic lubrication can accommodate heavy loads at low speeds. Hydrostatic lubrication is normally used in planar or linear bearings rather than in sleeves.
Design of an assembly using hydrostatic lubrication is extremely complex and must focus on lubricant feeding and containment.
Hydrodynamic lubrication is full film lubrication, and is most commonly employed with high-speed rotating shafts in plain sleeve bearings. Bearings with hydrodynamic lubrication are often called journal bearings. A wedge of lubricant is caught between the rotating shaft and bearing surface, providing sufficient pressure to carry the applied load. The shaft rides on a film of oil and does not contact the bearing except during periods of low speed or stasis. Typical coefficients of friction range from 0.002 to 0.010. Oil is typically used as the lubricant, and it must be supplied from a reservoir to maintain hydrodynamic lubrication. The lubricant also cools the bearing, and lubricant leakage and circulation enhances the cooling effect. Lubricant viscosity and temperature are important parameters in hydrodynamic lubrication performance, and temperature control is recommended. Hydrodynamically lubricated bearings go through periods of boundary lubrication during startup and shutdown periods. In light industrial machinery, relatively low speeds and/or intermittent movements mean that boundary lubrication of plain bearings is more common than hydrodynamic lubrication. Hydrodynamically lubricated journal bearings are beyond the scope of this text, but are detailed in the recommended resources.Figure 10-1: Plain Bearing Lubrication vs. Coefficient of Friction
Table of Contents
Introduction
Chapter 1: Design and Analysis
- Design of Machinery Units
- Equations
Chapter 2: Erogonomics and Machine Safety (Co-written with E. Smith Reed PE)
- Ergonomics
- Machine Safety
- Machine Safeguarding
- Other Safety Issues
- Recommended Resources
Chapter 3: Dimensions & Tolerances
- Limits, Fits, and Tolerance Grades
- Tolerances on Drawings
- Tolerance Stack-Ups (Written by Charles Gillis PE)
Chapter 4: Precision Locating Techniques (Written by Charles Gillis PE)
Chapter 5: Pins, Keys, and Retaining Rings
Chapter 6: Pipe Threads, Threaded Fasteners, and Washers
- Pipe and Port Threads
- Threaded Fasteners and Washers
Chapter 7: Welds and Weldments
Chapter 8: Materials, Surfaces, and Treatments
- Materials
- Surface Finish
- Heat Treatment
- Surface Treatment
Chapter 9: Force Generators
- Springs
- Pneumatics
- Electric Motors
Chapter 10: Bearings
- Plain Bearings
- Rolling Element Bearings
- Linear Bearings
Chapter 11: Power Transmission Devices
- Shafts
- Shaft Couplings
- Gears (Written by Gregory Aviza)
- Gearboxes
- Belts and Chains
- Lead, Ball, and Roller Screws