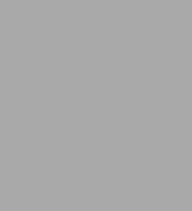
Natural Rubber Materials: Volume 2: Composites and Nanocomposites
856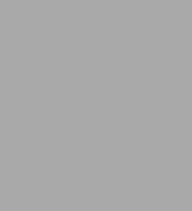
Natural Rubber Materials: Volume 2: Composites and Nanocomposites
856Hardcover
-
SHIP THIS ITEMNot Eligible for Free ShippingPICK UP IN STORECheck Availability at Nearby Stores
Available within 2 business hours
Related collections and offers
Overview
Volume 1 covers different types of natural rubber-based blends and IPNs as well as manufacturing methods, thermo mechanical characterization techniques, life cycle analysis and their applications. Volume 2 focuses on natural rubber-based composites and Nanocomposites including the different types of fillers, the filler-matrix reinforcement mechanisms, manufacturing techniques, and applications.
This is the first book to consolidate the current state of the art information on natural rubber based materials with contributions from established international experts in the field. The book provides a "one stop" reference resource for professionals, researchers, industrial practitioners, graduate students, and senior undergraduates in the fields of polymer science and engineering, materials science, surface science, bioengineering and chemical engineering.
About the Author
Read an Excerpt
Natural Rubber Materials Volume 2
Composites and Nanocomposites
By Sabu Thomas, Hanna J. Maria, Jithin Joy, Chin Han Chan, Laly A. Pothen
The Royal Society of Chemistry
Copyright © 2014 The Royal Society of ChemistryAll rights reserved.
ISBN: 978-1-84973-631-2
CHAPTER 1
Natural Rubber-Based Composites and Nanocomposites: State of the Art, New Challenges and Opportunities
C. H. CHAN, JITHIN JOY, HANNA J. MARIA AND S. THOMAS
1.1 Introduction
Natural rubber (NR) is also known as cis-1,4-poly(isoprene) and has the chemical structure illustrated in Figure 1.1 (a). NR is an elastomer originally derived from a milky colloidal suspension from the sap of some plants, called NR latex. Only the sap cultivated from the Hevea brasiliensis tree is of commercial importance (see Figure 1.1(b)). Hevea is native to Brazil and produces a high molecular weight of ~ 97% cis-1,4-poly(isoprene) (roughly 20,000 units of isoprene). This signifies that the NR polymer chain continues on the same side of the double bond. Hevea yields high-quality latex over a sustainable period and is amenable to tapping for approximately 30 years. The typical compositions of NR latex, dry NR and deproteinized dry NR (DPNR) are tabulated in Table 1.1. DPNR latex is a premier NR latex, treated with special enzymes or complexed with other chemicals to break down the naturally-occurring proteins. DPNR has improved resistance to fatigue failure for engineering applications.
The double bonds along the backbone of NR allow the attachment of pendant groups and/or provide chemically reactive sites for crosslinking or grafting. Naturally, NR is a soft and sticky solid with low tensile strength and low elasticity due to the weak van der Waals forces of its intermolecular attraction and occasional crosslinking. It softens at room temperature in tropical countries but hardens in cold weather and it is highly crystallizable upon stretching. It is soluble in some organic solvents, e.g. tetrahydrofuran, toluene, chloroform, methyl ethyl ketone, acetone, 2-butanone, n-hexane, benzene, etc. The properties of NR deteriorate drastically by sunlight, ozone and oxygen due to its high level of unsaturation, and such a material is of minimal interest in industry. The properties of pure NR are tabulated in Table 1.2. Addition of carbon black (CB), and antiozonants and waxes, to NR enhances its resistance to UV and ozone, respectively.
In 1496, Christopher Columbus returned from his second voyage and brought back the first NR balls from the West Indies to the Iberian Peninsula. In 1736, Charles Marie de La Condamine introduced NR samples and reported the properties of NR to the Academie Royale des Sciences of France. He proposed that NR could be used as flexible tubes. Later, in 1770, Joseph Priestley, an English chemist, suggested the possibility of using NR as an eraser because of its ability to rub pencil marks off paper. This is the first recorded use of NR. Samuel Peal patented a method of waterproofing cloth by coating the cloth with a solution of NR in turpentine in 1791. In 1820, Nadier, a British industrialist, produced NR threads for clothing accessories. In London, Thomas Hancock invented a mastication machine to mix and soften NR, enabling it to be shaped. In 1823, Charles Macintosh produced waterproof garments by coating cloth with a solution of NR in benzene in a plant in Glasgow.
However, NR did not attain any commercial value until nearly a century later. The first important chemical modification of NR was vulcanization in 1839, which is generally credited independently to Charles Goodyear (USA) and Thomas Hancock (England). Crosslinks are introduced into NR chains in the process of vulcanization by heating up the NR with addition of sulfur, accelerator, fillers and antioxidants (see Figure 1.2). Vulcanization turns NR into a hard and non-sticky polymeric material with improved tensile strength and higher resistance to organic solvents. This landmark in the history of NR has led to multibillion global NR industries.
In modern vulcanization processes, NR is generally compounded (either under high or low temperature) with 0.5 to 1 wt% of accelerators, different concentrations of CBs (which act as a filler) (up to 45 wt% for tyre manufacturing), low concentrations of aromatic amines and phenols for antioxidation purposes and 5–8 wt% of sulfur. These types of vulcanized NR are commonly known as NR composites (when the filler dimension is on the micro-scale) or NR nanocomposites (when the filler dimension is on the nanoscale). NR-based composites or nanocomposites will be discussed in more detail in the following sections.
The vulcanized NR is elastic and flexible, but the process of vulcanization is irreversible. The properties of vulcanized NR are shown in Table 1.2. Since the 1980s there has been much attention paid to the disposal of used NR goods in an eco-friendly way. To address this environmental problem, recent years have seen scientific research into reversible chemical changes of NR, as well as the replanting of NR trees to enable a sustainable and renewable source of supply for NR production, whereas synthetic rubber (SR) is produced from depleting oil reserves. The discovery of vulcanization of NR, led to a blossoming of NR industries, fuelled by additional supplies of NR from South-East Asia.
In 1876, Sir Henry Wickham transported 70,000 NR seedlings from the Amazon Basin to the Royal Botanic Gardens at Kew, of which only 2397 germinated. Some 1900 of these 2397 germinated seedlings were shipped on to Ceylon and Singapore (22 seedlings). Nine of the 22 seedlings from the Singapore Botanic Gardens were brought to Kuala Kangsar, Perak, Malaysia. These seedlings formed the nucleus of the NR industries in South-East Asia, which accounts for around 75% of all cultivated NR trees. Also at about this time, Sir Henry Nicholas Ridley (Director of the Singapore Botanic Gardens from 1888 to 1911) developed tapping techniques for the harvesting of NR latex from Hevea. Early industrial applications of vulcanized NR are shown in Table 1.3. NR trees were first grown in 1873 at the Royal Botanic Gardens, Calcutta, India, and the first commercial NR plantations were established at Thattekadu in Kerala in 1902.
1.2 Supply and Demand of NR as Compared to SR
After a number of important scientific discoveries related to NR from the 1870s onwards, there was a quantum leap in terms of progress in the industrial applications of NR. The commercial production of automobiles by Karl Benz began in 1888 and later, from 1908 onwards, the mass production of cars by Henry Ford, increased the demand for pneumatic tyres, which were made exclusively from NR. The use of vehicles during World War I, coupled with the peace-time demand for motorized vehicles, was a golden age in terms of demand for NR. Before World War II, rubber products used 100% NR. Even today, around 60% of NR is used in the production of tyres.
During World War II, Japan's occupation of most of the countries of South-East Asia blockaded the supply of NR to industries in the West. This was a cause for concern and these countries responded vigorously, by investigating synthetic substitutes for NR and searching for large-scale supply of NR from other continents. The efforts to cultivate rubber trees in other countries did not actually pose a serious threat to the NR industries in South-East Asia. However, the development of SR, which was initiated politically and was strategically motivated, has emerged as the most serious threat to NR. SR production technology is intensive and is less dependent on a large and low-cost supply of labour compared to the production of NR latex on estates. Examples of SR are polybutadiene, ethylene/propylene copolymers, styrene butadiene rubber, etc. The production of SR was prompted by cheap and relatively constant supplies of petrochemical feedstock. In addition, the development of emulsion and stereoregular polymerization, new polymerization techniques, the availability of a wide range of suitable monomers, introduction of new monomers, and so on, has unveiled unprecedented opportunities and increased the competitive strengths of SR as compared to NR, as summarized in Table 1.4. The early priority for Asian countries in terms of research was to increase the productivity of NR trees and to reduce the cost of production. However, new dimensions to position NR in the world rubber market have to be strategized, from agricultural commodity to specialized industrial raw material, as highlighted in Table 1.4. Trade statistics for the world consumption of NR and SR from 1825 to 1970 (see Table 1.5) illustrate the threat of SR to NR.
The increase in demand for NR over SR, which has dominated the world scene since World War II, is related to widespread concerns about global warming, deteriorating ecosystems and depleting sources of fossil fuels. Hevea is one of the most effective trees for generating oxygen from carbon dioxide via photosynthesis. In general, planting one tree eliminates 1 ton of CO2/year. An ecosystem of 33-year-old NR trees produces 450 tons/ha/year of biomass as compared to 475–664 tons/ha/year in Malaysian rainforests and 295–475 tons/ ha/year in Brazilian and Thai rainforests. However, it should also be noted that as industries urge towards sustainable farming practices for NR as demand rises, this may on the other hand drive deforestation.
Total world NR latex consumption gradually increased from 170,000 tons to 300,000 tons between 1960 and 1980. In the mid-1980s, total demand for NR latex took off, subsequently growing exponentially (see Figure 1.3). This marks the critical juncture of the transition of NR latex industries from the West to the East. The take-off was precipitated by prevention of transmission of human immunodeficiency virus (HIV) and hepatitis B with the increase in the use of NR latex gloves. At first, gloves were mainly used during surgery, but nowadays examination gloves are used in virtually all contacts with patients, the driving force being the fear of transmittable diseases through physical contact. In addition the large-scale production of electronic parts and higher hygienic standards in food production accelerated the usage of gloves during this period as well. There has been a marked increase in the demand for condoms, with their usage of condoms gradually diversifying from the prevention of pregnancy to the prevention of sexually transmitted diseases.
World consumption and production of NR and SR from 1926 to 2011 are summarized in Table 1.6 and Figure 1.3. In 2011, the world consumption of NR accounts for 42.3%, compared to SR at 57.7%. In 2011, 30% of NR was consumed by China. According to the former Secretary General of the International Rubber Study Group (IRSG) (Dr S. Evans), the projections for NR consumption and production in 2020 are 16.5 and 15.2 million tons, respectively. In other words, a deficit of 1.3 million tons of NR demand is expected. The major consumers of global NR production will be China (~ 7 million tons), followed by India (2.7 million tons), Europe, the USA and Japan. SR consumption in 2020 is expected to be 19.3 million tons.
1.3 Challenges and Opportunities for NR Industries
1.3.1 Challenges to Increase the Yield of NR Latex
Early research and development efforts on NR primarily focused on the increase in the yield of NR latex. As shown in Table 1.5, the maximum yield of NR latex increased from 500 to 3000 kg/ha/year from the 1920s to the 1970s. Conventional horticultural techniques of plant breeding, selection of parents, selection of progenies from nurseries and selection of materials are the early attempts. However, this route demands long investigation period of 20 years by 1960s. New techniques, for examples gene manipulation and mutation breeding used in combination proven workhorse of tissue culture may push the yield of NR to the theoretical limit, up to 9000 kg/ha/year. By 1984, RRIM 900 series' clones of NR trees could produce around 5000 kg/ha/year under ideal soil and terrain conditions for small- and pilot-scale plantings (Figure 1.4). However, a yield of NR latex of around 3000 kg/ha/year under ideal conditions is still common. This figure is still far below the theoretical yielding potential of NR trees (9000 kg/ha/year). Sustainable improvements in the yield of NR through plant breeding can only be achieved with the accessibility of a large genetic base, especially for countries outside Amazon basin.
In Malaysia, the yield of NR from small stakeholders (two-thirds of the total planting area for NR trees) is still around 1500 kg/ha/year. The common challenges of the small stakeholders include their increasing age and the lack of interest of the younger generation in NR plantations, old NR trees, and worker shortages. These lead to mature NR trees not being not tapped properly, and only around 4% of the NR trees from the small stakeholders use stimulants (e.g. ethereal) to increase the yield of NR latex. On the other hand, the yield of NR in plantations is around 2000 kg/ha/year. One of the targets is to increase the yield of NR from small stakeholders to 1960 kg/ha/year by 2020.
Bridgestone Americas Center for Research and Technology successfully decoded the main genome sequence for Hevea, the data of which is expected to facilitate the development of improved breeding technologies and growing method of NR. Bridgestone expects to develop and improve Hevea clones with higher yield and quality.
NR latex flows out from the latex vessels of NR trees after tapping. Best NR yield can be obtained for tapping at around 2 am. The latex vessels become plugged with particles after clotting is initiated by the flow of NR latex after several hours. When the cut is reopened on the following day, NR latex flows out again. The NR latex is collected daily for further processes. The production of NR latex is labour intensive in most countries and the common practice to solve this predicament is by importing/recruiting indentured cheap labour. Generally, one tapper is needed for every 4 ha of NR plantation. However, this strategy serves as the short-term solution for the economic NR production. Regrettably, this common approach has delayed innovative discoveries for higher production of NR latex with minimal of manpower. By using gaseous stimulant (e.g. G-flex stimulant), 20–25 g NR/tap/day can be collected. The use of etherel (as stimulant) to prolong the flow of NR latex from a tapping cut and the use of chemical-contained polybag (to prevent premature coagulation of NR latex) may lead to the 10-day interval for the collection of NR latex from the polybag under ideal situation. However, issues of collection of NR latex from polybags (in some cases up to ~ 1 kg) by unauthorized people remain unsolved in unfenced NR plantations. Roughly 10% slurry of Ethrels in palm oil is applied by hand with a paint brush on the NR bark near the tapping panel. Within days, hydrolysis of Ethrel® occurs and liberates ethylene and the absorption of ethylene within the NR tree tissues causes a dramatic increase in NR yield. Ethrel® can be reapplied at 2-month intervals.
(Continues...)
Excerpted from Natural Rubber Materials Volume 2 by Sabu Thomas, Hanna J. Maria, Jithin Joy, Chin Han Chan, Laly A. Pothen. Copyright © 2014 The Royal Society of Chemistry. Excerpted by permission of The Royal Society of Chemistry.
All rights reserved. No part of this excerpt may be reproduced or reprinted without permission in writing from the publisher.
Excerpts are provided by Dial-A-Book Inc. solely for the personal use of visitors to this web site.