Rapid Prototyping, Rapid Tooling and Reverse Engineering: From Biological Models to 3D Bioprinters / Edition 1 available in Hardcover
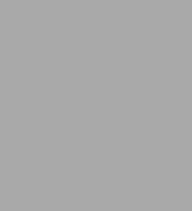
Rapid Prototyping, Rapid Tooling and Reverse Engineering: From Biological Models to 3D Bioprinters / Edition 1
- ISBN-10:
- 3110663244
- ISBN-13:
- 9783110663242
- Pub. Date:
- 06/08/2020
- Publisher:
- De Gruyter
- ISBN-10:
- 3110663244
- ISBN-13:
- 9783110663242
- Pub. Date:
- 06/08/2020
- Publisher:
- De Gruyter
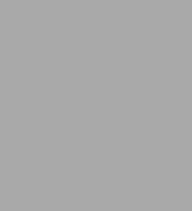
Rapid Prototyping, Rapid Tooling and Reverse Engineering: From Biological Models to 3D Bioprinters / Edition 1
Hardcover
Buy New
$210.00-
SHIP THIS ITEMIn stock. Ships in 1-2 days.PICK UP IN STORE
Your local store may have stock of this item.
Available within 2 business hours
Overview
The first methods for rapid prototyping became available in the late 1980s and were used to produce models and prototype parts. Today, they are used for a wide range of applications and are used to manufacture production-quality parts in relatively small numbers if desired without the typical unfavorable short-run economics. This economy has encouraged online service bureaus for early product realization or physical products for actual testing.
This book is expected to contain Seven Chapters. Chapter 1 would explain product life cycle and the product development phase in the same, introducing role of Rapid Prototyping Techniques in Product development phase. Chapter 2 would deals with the concept, origin and working cycle of Rapid Prototyping Processes. Chapter 3 would concentrates on the applications of Rapid Prototyping Technology. Apart from elaboration of engineering and non-engineering applications, it also elaborates on recent applications like Bio-Medical Models for Surgical Planning, Molecular Models, Architectural Models, Sculptured Models, Psycho-Analysis Models etc. Chapter 4 would introduce the various Rapid Prototyping systems available worldwide. The chapter also introduces the technique of generating human organs from live cells/tissues of the same human named 3D BIO PRINTERS hence ensuring low rejection rate by human body. As the Rapid Prototyping Techniques are for tailor made products and not for mass manufacturing hence Chapter 5 would elaborates on the mass manufacturing of rapid prototyped products. This includes Casting and Rapid Tooling. Chapter 6 would deal with Reverse Engineering and the role played by Rapid Prototyping Techniques towards the same. As the product realization is primarily dependent on various softwares which are required to be understood for better accuracy so the concluding chapter of the book i.e. Chapter 7 would explain some software associated with the various techniques.Product Details
ISBN-13: | 9783110663242 |
---|---|
Publisher: | De Gruyter |
Publication date: | 06/08/2020 |
Series: | Advanced Mechanical Engineering , #5 |
Pages: | 173 |
Product dimensions: | 6.69(w) x 9.45(h) x (d) |
Age Range: | 18 Years |
About the Author
Table of Contents
Preface v
About the authors vii
Chapter 1 Product life cycle 1
1.1 Introduction 1
1.2 Product development phase in product life cycle 3
1.2.1 Phase 1: conceive 5
1.2.1.1 Meaning: idea generation, specify, plan and innovate 5
1.2.2 Phase 2: design 6
1.2.2.1 Delineate, define, develop, test, analyze and validate 6
1.2.3 Phase 3: realize 6
1.2.3.1 Fabricate, make, develop, procure, sell and deliver 6
1.2.4 Phase 4: service 7
1.2.4.1 Utilize, operate, maintenance, support, sustain, phase-out, obsolete, recycle and disposal 7
1.3 Rapid prototyping technology in product development and realization 7
1.4 Conclusion 9
Chapter 2 Rapid prototyping processes 11
2.1 Introduction 11
2.2 Origins of rapid prototyping 12
2.3 Design process 13
2.3.1 The concept 13
2.3.2 Preliminary designs 14
2.3.3 Preliminary prototype fabrication 14
2.3.4 Short-run production 14
2.3.5 Final production 15
2.4 Rapid prototyping cycle 15
Chapter 3 Applications of rapid prototyping processes 17
3.1 Introduction 17
3.2 Engineering application 17
3.2.1 Prototype for concept evaluation 17
3.3 Nonengineering applications 19
3.3.1 Biomedical models for surgical planning 19
3.3.1.1 Steps in production of rapid prototyping models 19
3.3.1.2 Design evaluation and surgical planning 19
3.3.1.3 Additive manufacturing and production of the model 20
3.3.14 Surgical simulation and virtual planning 20
3.3.2 Development of prosthesis and implants 21
3.3.3 Molecular models 21
3.3.3.1 Design of physical models 22
3.3.3.2 Fabrication of models 23
3.3.3.3 Augmented reality interface 24
3.3.3.4 Examples 25
3.3.3.5 HIV protease 25
3.3.3.6 Superoxide dismutase 26
3.3.3.7 Ribosome 26
3.3.4 Architectural models 26
3.3.4.1 Architectural needs 26
3.3.4.2 Models and architectural designs 26
3.3.4.3 Limitations of models 27
3.3.4.4 Representation of models 28
3.3.4.5 Digital models for representations 29
3.3.4.6 Rapid prototyping 29
3.3.5 Sculptured models 30
3.3.6 Food article models 34
3.3.6.1 Rapid prototyping food and beverage packaging 34
3.3.6.2 3D printing and food 35
3.3.6.3 Applications of 3D printed food 35
3.3.7 Models for NEMS/MEMS applications 36
3.3.7.1 Evolution and rise of MEMS 36
3.3.7.2 Impact in medicine 37
3.3.7.3 MEMS evolving manufacturing alternatives 37
3.3.7.4 Tools for modeling and simulation 38
3.3.7.5 Prototyping and MEMS 38
3.3.7.6 Virtual reality prototyping and MEMS 41
3.3.8 Models for toys 42
3.3.8.1 The challenge of toy design 42
3.3.9 Psychoanalysis models 43
3.3.9.1 Rapid prototyping 43
3.3.9.2 Nuclear magnetic resonance imaging 44
3.3.9.3 Procedure 44
3.4 Conclusion 45
Chapter 4 Rapid prototyping/manufacturing processes 47
4.1 Introduction 47
4.2 Liquid-based processes 48
4.2.1 Stereolithography 49
4.2.1.1 The stereolithography apparatus 49
4.2.1.2 Stereolithography apparatus operation 50
4.2.1.3 Relation to other rapid prototyping technologies 51
4.2.1.4 Advantages and disadvantages 51
4.2.2 Jetting systems 52
4.2.3 Direct light processing technologies 52
4.2.4 High-viscosity jetting 53
4.2.5 The Maple process 53
4.3 Powder-based processes 54
4.3.1 Selective laser sintering (polymers) 54
4.3.2 Selective laser sintering (ceramics and metals) 55
4.3.3 Direct metal laser sintering 55
4.3.4 Three-dimensional printing 56
4.3.5 Fused metal deposition systems 56
4.3.6 Electron beam melting 56
4.3.7 Selective laser melting 57
4.3.7.1 Process 57
4.3.7.2 Advantages of SLM 58
4.3.8 Selective mask sintering 58
4.3.9 Electrophotographic layered manufacturing 58
4.3.10 High-speed sintering 59
4.4 Solid-based processes 60
4.4.1 Fused deposition modeling 60
4.4.1.1 FDM process parameters 61
4.4.2 Sheet stacking technologies 62
4.4.2.1 System hardware 62
4.4.2.2 Process 64
4.4.2.3 Software 64
4.4.2.4 Part orientation 64
4.4.2.5 Crosshatching 65
4.4.2.6 System parameters 65
4.4.2.7 Technique 66
4.4.2.8 Finishing 68
4.4.2.9 Advantages and disadvantages 68
4.5 Bioprinter 69
4.5.1 Three-dimensional bioprinting techniques 70
4.5.1.1 Ink-jet-based printing 70
4.5.1.2 Extrusion-based printing 73
4.5.1.3 Laser direct write 74
4.6 Conclusion 76
Chapter 5 Mass manufacturing from rapid prototyped products 77
5.1 Introduction 77
5.2 Casting processes 77
5.2.1 Investment casting 77
5.2.1.1 The process 77
5.2.1.2 Investment casting design parameters 78
5.2.1.3 Advantages and disadvantages of investment casting 84
5.2.2 Sand casting 85
5.2.2.1 Pattern 86
5.2.2.2 Types of pattern 89
5.2.2.3 Parting line 90
5.2.2.4 Core and core box 90
5.2.2.5 Binders 91
5.2.2.6 Molding material 91
5.2.2.7 Molding sands 92
5.2.2.8 Refractory sands 93
5.2.3 Permanent mold casting processes 94
5.2.3.1 Pressure die casting process 94
5.2.3.2 Squeeze casting 95
5.2.3.3 Centrifugal casting 95
5.2.3.4 Continuous casting 95
5.3 Rapid tooling 96
5.3.1 Direct rapid prototyped tooling 96
5.3.1.1 30 printing (Z402 system) 97
5.3.1.2 Laser engineered net shaping 100
5.3.2 Silicone rubber tooling 101
5.3.2.1 Process 102
5.3.2.2 Dimensional accuracy of products manufactured using silicone rubber tooling 102
5.3.3 Investment-cast tooling 103
5.3.4 Powder metallurgy tooling 103
5.3.4.1 3D Keltool 103
5.3.5 Spray metal tooling 104
5.3.6 Desktop machining 105
5.4 Conclusion 105
Chapter 6 Reverse engineering using rapid prototyping 107
6.1 Introduction 107
6.2 Process 108
6.2.1 Phase 1 - Scanning 108
6.2.1.1 Contact scanners 108
6.2.1.2 Noncontact scanners 109
6.2.2 Phase 2 - point processing 109
6.2.3 Phase 3 - Application geometric model development 110
6.2.4 Integration of RE and RP for layer-based model generation 110
6.2.4.1 The adaptive slicing approach for cloud data modeling 111
6.2.4.2 Planar polygon curve construction for a layer 112
6.2.4.3 Initial point determination 113
6.2.4.4 Constructing the first line segment 114
6.2.4.5 Constructing the remaining line segments (Si) 116
6.2.4.6 Determination of adaptive layer thickness 117
6.3 Other reverse engineering applications 117
6.3.1 Reverse engineering and the automotive industry 117
6.3.1.1 Reverse engineering - workflow for automotive body design 118
6.3.2 Reverse engineering in the aerospace industry 119
6.3.2.1 Reducing costs of hard tooling 119
6.3.3 Reverse engineering and the medical device industry 121
6.3.3.1 Reverse engineering - A better knee replacement 121
6.4 Conclusion 122
Chapter 7 3D bioprinting 124
7.1 Introduction 124
7.2 Extrusion-based bioprinting 125
7.3 Laser-assisted bioprinting 128
7.4 Stereolithography-based bioprinting 129
7.5 Challenges, applications and future perspective 131
7.6 Conclusion 132
Glossary 135
Bibliography 149
Index 159