The Portal to Lean Production: Principles and Practices for Doing More with Less
The Portal to Lean Production: Principles and Practices for Doing More with Less describes the steps, difficulties, and rewards of implementing lean production. The book moves beyond concepts to address practical matters. The authors provide enough information for you to begin implementing lean production within your organization.
This book applies a model-the Portal to Lean Production-to illustrate principles and practices. The model reappears at the start of every chapter and serves to connect the concepts of each chapter with those in other chapters, and with basic lean production principles.
This volume contains short vignettes that appear in every chapter of actual lean production implementations. Following these real-world examples, the text provides expanded coverage of topics to enable you to learn and apply concepts and principles. The authors enable you to see the context, application, and practical issues associated with lean production concepts and methods before learning details. The vignettes, based upon the work experience of co-author Avi Soni, help connect the concepts and tie them to practical examples.
1111242092
This book applies a model-the Portal to Lean Production-to illustrate principles and practices. The model reappears at the start of every chapter and serves to connect the concepts of each chapter with those in other chapters, and with basic lean production principles.
This volume contains short vignettes that appear in every chapter of actual lean production implementations. Following these real-world examples, the text provides expanded coverage of topics to enable you to learn and apply concepts and principles. The authors enable you to see the context, application, and practical issues associated with lean production concepts and methods before learning details. The vignettes, based upon the work experience of co-author Avi Soni, help connect the concepts and tie them to practical examples.
The Portal to Lean Production: Principles and Practices for Doing More with Less
The Portal to Lean Production: Principles and Practices for Doing More with Less describes the steps, difficulties, and rewards of implementing lean production. The book moves beyond concepts to address practical matters. The authors provide enough information for you to begin implementing lean production within your organization.
This book applies a model-the Portal to Lean Production-to illustrate principles and practices. The model reappears at the start of every chapter and serves to connect the concepts of each chapter with those in other chapters, and with basic lean production principles.
This volume contains short vignettes that appear in every chapter of actual lean production implementations. Following these real-world examples, the text provides expanded coverage of topics to enable you to learn and apply concepts and principles. The authors enable you to see the context, application, and practical issues associated with lean production concepts and methods before learning details. The vignettes, based upon the work experience of co-author Avi Soni, help connect the concepts and tie them to practical examples.
This book applies a model-the Portal to Lean Production-to illustrate principles and practices. The model reappears at the start of every chapter and serves to connect the concepts of each chapter with those in other chapters, and with basic lean production principles.
This volume contains short vignettes that appear in every chapter of actual lean production implementations. Following these real-world examples, the text provides expanded coverage of topics to enable you to learn and apply concepts and principles. The authors enable you to see the context, application, and practical issues associated with lean production concepts and methods before learning details. The vignettes, based upon the work experience of co-author Avi Soni, help connect the concepts and tie them to practical examples.
130.0
In Stock
5
1
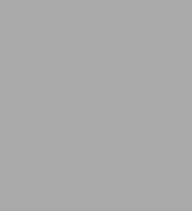
The Portal to Lean Production: Principles and Practices for Doing More with Less
342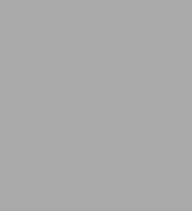
The Portal to Lean Production: Principles and Practices for Doing More with Less
342Hardcover(New Edition)
$130.00
130.0
In Stock
Product Details
ISBN-13: | 9780849350313 |
---|---|
Publisher: | Taylor & Francis |
Publication date: | 11/02/2005 |
Series: | Resource Management , #36 |
Edition description: | New Edition |
Pages: | 342 |
Product dimensions: | 6.12(w) x 9.19(h) x (d) |
About the Author
From the B&N Reads Blog