Go to resource on all the furnaces that made Alabama internationally significant in the iron and steel industry
This work is the first and remains the only source of information on all blast furnaces built and operated in Alabama, from the first known charcoal furnace of 1815 (Cedar Creek Furnace in Franklin County) to the coke-fired giants built before the onset of the Great Depression. Woodward surveys the iron industry from the early, small local market furnaces through the rise of the iron industry in support of the Confederate war effort, to the giant internationally important industry that developed in the 1890s. The bulk of the book consists of individual illustrated histories of all blast furnaces ever constructed and operated in the state, furnaces that went into production and four that were built but never went into blast.
Written to provide a record of every blast furnace built in Alabama from 1815 to 1940, this book was widely acclaimed and today remains one of the most quoted references on the iron and steel industry.
Go to resource on all the furnaces that made Alabama internationally significant in the iron and steel industry
This work is the first and remains the only source of information on all blast furnaces built and operated in Alabama, from the first known charcoal furnace of 1815 (Cedar Creek Furnace in Franklin County) to the coke-fired giants built before the onset of the Great Depression. Woodward surveys the iron industry from the early, small local market furnaces through the rise of the iron industry in support of the Confederate war effort, to the giant internationally important industry that developed in the 1890s. The bulk of the book consists of individual illustrated histories of all blast furnaces ever constructed and operated in the state, furnaces that went into production and four that were built but never went into blast.
Written to provide a record of every blast furnace built in Alabama from 1815 to 1940, this book was widely acclaimed and today remains one of the most quoted references on the iron and steel industry.
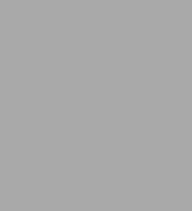
Alabama Blast Furnaces
176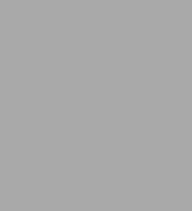
Alabama Blast Furnaces
176eBook
Available on Compatible NOOK devices, the free NOOK App and in My Digital Library.
Related collections and offers
Overview
Go to resource on all the furnaces that made Alabama internationally significant in the iron and steel industry
This work is the first and remains the only source of information on all blast furnaces built and operated in Alabama, from the first known charcoal furnace of 1815 (Cedar Creek Furnace in Franklin County) to the coke-fired giants built before the onset of the Great Depression. Woodward surveys the iron industry from the early, small local market furnaces through the rise of the iron industry in support of the Confederate war effort, to the giant internationally important industry that developed in the 1890s. The bulk of the book consists of individual illustrated histories of all blast furnaces ever constructed and operated in the state, furnaces that went into production and four that were built but never went into blast.
Written to provide a record of every blast furnace built in Alabama from 1815 to 1940, this book was widely acclaimed and today remains one of the most quoted references on the iron and steel industry.
Product Details
ISBN-13: | 9780817381011 |
---|---|
Publisher: | University of Alabama Press |
Publication date: | 09/26/2008 |
Series: | Library of Alabama Classics |
Sold by: | Barnes & Noble |
Format: | eBook |
Pages: | 176 |
File size: | 14 MB |
Note: | This product may take a few minutes to download. |
About the Author
James R. Bennett is Commissioner of the State of Alabama Department of Labor, Chair of the Board or Trustees of Jacksonville State University, and author of Tannehill and the Growth of the Alabama Iron Industry.
Read an Excerpt
Alabama Blast Furnaces
By Joseph H. Woodward II
The University of Alabama Press
Copyright © 1940 The University of Alabama PressAll rights reserved.
ISBN: 978-0-8173-8101-1
CHAPTER 1
PIONEER ERA
1815-1861
In 1815—four years before Alabama was admitted to the Union—the first blast furnace was erected in the state.
So closely integrated with community life was this and other blast furnaces built during this pioneer era of Alabama's iron industry, that any chronicle of these iron makers must be set against the frontier background of this early period in the state's history.
In 1815, and for many years thereafter, North Alabama was a frontier where life was crude and extremely simple. Much of this section of the state was then a wilderness. Cherokee, Chickasaw and Creek Indians still roamed the forests. Such settlements as had come into existence were largely along navigable rivers. These were self-contained communities in most of which were found a blacksmith shop, a tanyard and a general store. Transportation was largely by river, despite floods and drought. Such roads as existed were impassable during much of the year to all but the man on horseback. Steamboats plied upstream to bring the products of civilization and returned downstream with raw materials from the frontier. As early as 1824 they carried cargoes up the Tennessee river to the shoals at Florence. An interesting sidelight on the price of importations from New Orleans is furnished by this price list of commodities, published in the "Enquirer" of Tuscumbia in 1824:
Flour &8.00 bbl.
Salt 1.50 bu.
Whiskey .40 gal.
Sugar .15 lb.
Coffee .40 lb.
Iron .10 lb.
Steel .31 lb.
Also interesting as an index of the population characteristics of the period is the census of Tuscumbia in 1827 which listed:
White males over 21 365
White males under 21 185
White females over 21 183
Blacks 403
1320
From 1815 to 1861, life ran on in Alabama like a slow moving stream. Settlements expanded, population grew, scattered industries came into existence, virgin forests gave way to farms. But on the whole, this entire period brought little basic change to the pattern of life in Alabama or the status of the state's iron industry.
Like the life in Alabama, blast furnaces of this early era were very simple in design. All had certain similarities of construction.
Most of these early isolated operations had forges. Here the cold blast charcoal iron was beaten into plow points, fire dogs and other domestic implements. If the plant was far enough removed from other settlements, a sawmill and grist mill were usually built. One such early plant boasted a machine shop "capable of executing the finest workmanship." As a rule, however, the ingenious blacksmith was more than capable of making and maintaining the simple machinery of the furnace.
These early blast furnaces were owned either by individuals or partnerships, rarely by a stock company. Despite this individuality of ownership, Alabama never had a "mansion furnace," so common in Virginia, where the furnace was usually operated in conjuction with a plantation; in Alabama the furnace was the main object.
A furnace 30 feet high with a 6 foot diameter bosh was capable of producing from three to eight tons of pig iron a day, depending largely on the grade of ore. If the owner was not an iron-master, he hired an operator who was paid according to the tonnage of iron produced. These early iron manufacturers had no knowledge of chemistry, no analysis of the ore or charcoal; they depended on some ancient formula which they altered to suit local conditions. The ironmaster stood on the top of his little stone stack amid the pulsating billows of smoke and sparks and gauged by eye the amounts of ore, fuel and limestone required.
At casting time he stood in the high arch covering the iron notch and directed the cast. From the forehearth the iron was tapped into small sand beds or, if hollowware was being cast, the iron was ladled directly into the molds. When a sufficient quantity of domestic and agricultural implements had been cast, they were hauled by wagon throughout the surrounding country and sold or bartered to the farmers and small store owners. Quite often these wares were rafted down some river to larger towns. Most of the pig iron was shipped to small foundries, forges, gin manufacturers and other small users of iron.
The usual shape of the furnace was that of a truncated pyramid built of stone blocks around a hollow chamber, the height ranging from 19 to 40 feet and the bosh (the widest portion of the chamber) from 4 to 8 feet in diameter. The location of the furnace depended upon four equally important factors: first, the proximity of an ore bed (usually surface ore); second, a stream sufficient to furnish water power for blowing; third, an abundance of wood for burning into charcoal; and fourth, a hillside against which to build the stack. This last requisite was essential for the charging of the raw material into the furnace top. For this purpose a bridge was built to connect the furnace top and the hill.
By comparison with the modern blast furnace plant, the old furnace seems a marvel of simplicity. It must be remembered, however, that virtually all of the material as well as the appurtenances of the plant had to be obtained locally. As a rule the large limestone blocks, forming the outer portion of the stack, had to be cut and hewn by hand, then hauled by oxen to the furnace site. It may be assumed that a large part of the manual labor was performed by slaves. That does not imply that the furnace owner (iron-master) was himself a slave holder. The practice was to hire slaves from local owners on a yearly basis. The operator, by contract, housed, fed, clothed, and guarded the slaves, a practice which continued until the end of the Civil War.
Due to the necessity of locating the furnace near the ore, the plants were often some distance from the nearest settlement. Under such circumstances, little self-contained communities arose in the furnace neighborhood. Log houses first were built to house the labor, then usually a small store was operated by the iron-master to supply the essential commodities.
Between 1815 and 1860 only two improvements of importance were made in blast furnace practice. In 1854 the first hot blast pipe stove was installed in Alabama. It is interesting to note that this innovation was declared a failure by the first man to use it. The second innovation was the substitution of steam driven blowers for the older water power. With water power, the operation of the plant depended on the supply of water, consequently during times of drought or flood, the furnace was idle. Therefore, this latter improvement enabled the furnace to operate a much greater portion of the year.
Prior to the Civil War seven (and possibly eight) stone blast furnaces were built in Alabama. We are accustomed to the veneration of anything historical; in fact, we think of the pioneer as a hero. In a certain measure the pioneer ironmaster was a courageous man but in his own eyes (from the evidence of his records) he was simply a business man working under somewhat annoying handicaps. These little furnaces were nevertheless the stepping stones to our modern plants.
CHAPTER 2THE CIVIL WAR ERA
1861-1865
Over the peaceful scene in Alabama, long-hovering war clouds broke in 1861. One by one the Southern States seceded, the Confederacy was formed, the tragic Civil War ensued. At the outset both the Union and Confederacy anticipated a brief war and a decisive victory. During the first year of hostilities, importations from abroad provided a large part of the Confederate army ordnance. But when the war entered its second year, the military needs of the South became increasingly apparent as the Union blockade grew more effective. Soon the South realized that immediate development of its manufacturing facilities was imperative. As the conflict wore on, "iron and more iron" became the pressing cry of the Confederacy.
On April 11, 1862, the Confederate Government established the Nitre and Mining Bureau to foster the production of raw materials for its various arsenals. At the commencement of the Civil War there were six, or possibly seven blast furnaces operating in Alabama. The total daily capacity of all these furnaces could not have exceeded 40 tons and was probably less. As the war dragged on, the armies in the field demanded more and more supplies of shot and shell. More and more iron became an absolute necessity and the Nitre and Mining Bureau put forth increasing effort to supply the deficiency. Finally the shortage of materials became so acute that the Confederate Congress, on June 16, 1863, passed an act empowering the Nitre and Mining Bureau to impress all manufacturing.
Between 1862 and 1865 thirteen new blast furnaces were built in Alabama. The Confederate government advanced either all or part of the funds necessary for these projects. Amounts up to $100,000 were provided and, in return, the operators were required to furnish definite percentages of the furnace output to the arsenals and shipbuilding yards. Under the stress of war conditions, the Nitre and Mining Bureau dictated the operating policies of the blast furnace industry. Owners, operators, labor—both skilled and unskilled—were pressed into service.
Governmental regulations multiplied and became most stringent. Reports of every kind had to be filled in and filed; the detailed information required was almost endless. Added to these difficulties was the continued scarcity of operating essentials such as labor. The Confederate government pressed thousands of slaves into service to dig trenches and perform similar tasks in the combat areas. Union raids freed thousands more. The labor shortage became acute.
Horses, mules and oxen could be obtained only through government orders. Staple food supplies, such as meat, corn and hay had to be brought in from Florida and other distant points. Due to the lack of labor and supplies, furnaces often had to shut down for weeks at a time.
Financial difficulties also beset the furnace operator during this period. At the beginning of the war the price of iron ranged between $25 and $30 a ton. Slave hire was $125 to $175 per year. As the war progressed the credit of the Confederacy weakened, inflation of the currency took place and by 1865 iron was quoted at $500 per ton, a meaningless figure since the currency was practically valueless.
By that date slaves had almost disappeared and the lot of the iron-master was far from a happy one. In the the end it mattered little; profiteers and patriots suffered the same fate.
In spite of these odds and difficulties, during the war years two notable experiments were made by Alabama furnacemen. Pig iron was produced in Shelby County using raw bituminous coal as fuel, the result being pronounced "the equal of hot blast charcoal iron." In Jefferson County the first coke pig iron in Alabama was produced, the experiment being proclaimed "a success." That neither experiment was carried further was due to the lack of a coal supply. A permanent advance made during the war years was the first installation in Alabama of a manually operated bell and hopper on the furnace top.
Following is a list of the furnaces known to have supplied pig iron to the Confederacy:
Furnaces
Cane 1
Shelby Iron Co. 2
Round Mountain 1
Choccolocco Iron Works (Knight) 1
Roup's Valley Iron Works (Tannehill) 3
Hale & Murdock Iron Works 1
Red Mountain Iron & Coal Co. (Oxmoor) 1
Cahawba Iron Works (Irondale) 1
Bibb Naval Furnaces 2
Salt Creek Iron Works (Jenifer) 1
Oxford Iron Co. 1
Cornwall Iron Works 1
Little Cahaba Iron Works 1
17
Dut to the many irregularities of operation at this time it is impossible to estimate the tonnage produced. A report of the Nitre and Mining Bureau to the Confederate Congress states that twelve furnaces operating in Alabama delivered to the government in the nine month period ended Sept. 30, 1864, a total of 5913.7 gross tons of pig and rolled iron. And the total iron delivered to the government from Jan. 1, 1863 to Sept. 30, 1864 amounted to only 12,354.8 gross tons. Another report, dated Nov. 20, 1864, to the Chief of the Nitre and Mining Bureau states:
"In one case the government furnace in Bibb County, Alabama, averaged through the month thirteen tons of iron per day, and at another furnace an average of ten tons per day was obtained for one month. From many disturbing causes incident to the war much time has been lost at the Alabama furnaces and the daily average would scarcely exceed, if equal, four tons per day."
Despite the smallness of this amount, Alabama delivered to the Confederacy more iron than the rest of the Southern States combined.
Gen. Robert E. Lee surrendered on April 9, 1865 and the war was practically over. In the deep South, however, Union raids still continued. At Munford, April 25, 1865, the last shot was fired in defense of Alabama. The Home Guard was overcome and a momument now marks the spot of the last Alabama casualty. Two miles farther the raiders came upon the little furnace on Salt Creek and destroyed it. Only one of Alabama's 17 furnaces was left intact. Dark indeed seemed the future of the iron industry in Alabama.
CHAPTER 3THE RECONSTRUCTION ERA
1866-1879
The years which followed in the wake of the Civil War have been called the "tragic era" in the South's history. That four-year conflict left Alabama and other Southern states stripped of wealth and resources, with almost every industry paralyzed and prostrate. To this bitter cup of defeat was added military rule and martial law with "carpet bag" and "scalawag" control of state governments to impede further restoration and recovery.
For eight years after the war's end, the iron industry of Alabama lay practically dormant. But then within a single year, four new companies were formed and four furnaces were built, largely with Northern capital. During this Reconstruction Era, there was also introduced a new type of furnace construction, employing iron or steel shells with iron supporting columns instead of the old type of stone furnace, only two of which were built after the war. In this new type furnace, sandstone hearths and open tops continued to be used at first, but these were soon changed to fire brick hearth and lining and closed tops, of the bell and hopper type. Steam driven elevators took the place of the old hillside method of filling. Steam blowing engines replaced the old water driven blowers. Oxen could no longer be employed to transport the larger quantities of base material and increased volume of products. Railroads were built and new markets were opened. At last the industrial star of Alabama seemed to be in the ascendency, when suddenly the panic of 1873 descended on the nation. Southern enterprises suffered a severe setback. Hopes fell and the fight against vast odds seemed once more hopeless. Not all men despaired, however, and from the panic of 1873 came an experiment that finally turned the tide of fortune for the iron industry of Alabama.
The cost of charcoal iron, even in 1873, was too high to compete with cheaper Northern coke iron. Only for specialized castings was charcoal iron used. And too, with each succeeding year charcoal became scarcer and more expensive as forests surrounding furnaces were gradually depleted.
In the Fall of 1875 it was decided to use Alabama coke to smelt Alabama red hematite ore. Perhaps the iron-masters had forgotten the experiment during the Civil War. At any rate there was divided opinion on the practicability of this new move. In February, 1876, however the first cast of coke iron was made. Opinion still remained divided; some declared the iron a success, others ridiculed the attempt. Northern iron-masters proclaimed the coke iron a "wretched product;" the Southern press replied with glowing forecasts for the future of Alabama's iron industry. Finally after four years experience with production of coke iron in the Birmingham district, further capital was attracted and confidence was established. Two modern furnaces were started. The Reconstruction Era was over and the Alabama "Iron Boom" was under way.
(Continues...)
Excerpted from Alabama Blast Furnaces by Joseph H. Woodward II. Copyright © 1940 The University of Alabama Press. Excerpted by permission of The University of Alabama Press.
All rights reserved. No part of this excerpt may be reproduced or reprinted without permission in writing from the publisher.
Excerpts are provided by Dial-A-Book Inc. solely for the personal use of visitors to this web site.