Best Practices Guide to Residential Construction: Materials, Finishes, and Details / Edition 1 available in Hardcover
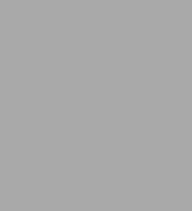
Best Practices Guide to Residential Construction: Materials, Finishes, and Details / Edition 1
- ISBN-10:
- 0471648361
- ISBN-13:
- 9780471648369
- Pub. Date:
- 11/18/2005
- Publisher:
- Wiley
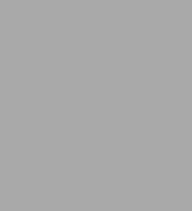
Best Practices Guide to Residential Construction: Materials, Finishes, and Details / Edition 1
Hardcover
Buy New
$103.95Buy Used
$68.51-
-
SHIP THIS ITEM
Temporarily Out of Stock Online
Please check back later for updated availability.
-
Overview
Product Details
ISBN-13: | 9780471648369 |
---|---|
Publisher: | Wiley |
Publication date: | 11/18/2005 |
Pages: | 320 |
Product dimensions: | 8.60(w) x 11.00(h) x 1.00(d) |
About the Author
Read an Excerpt
Best Practices Guide to Residential Construction
By Steve Bliss
John Wiley & Sons
ISBN: 0-471-64836-1Chapter One
Roofing
ASPHALT SHINGLES
Asphalt shingles, which cover 80 to 90% of residential roofs, have undergone much change in the last 20 to 30 years. Until the late 1970s, all asphalt shingles were manufactured from a heavy organic felt mat that had established a reputation for both strength and flexibility and generally outlasted their 15- to 20-year life expectancy. Since their introduction in the late 1970s, fiberglass shingles have come to dominate the market, accounting for over 90% of shingles sold today. However, premature failure of some fiberglass shingles in the 1980s and 1990s tarnished the product's reputation and spawned a number of lawsuits and resulted in a toughening of standards and a general improvement in fiberglass shingle quality.
Shingle styles have changed as well. The common three-tab shingles of the 1950s and 1960s are now joined by no-cutout shingles, multitab shingles, and laminated "architectural" shingles (Table 2-1). Laminated shingles provide deep shadow lines and a heavily textured appearance, some simulating wood or slate. These now account for over half the shingles sold.
Shingle Quality
Shingle quality is often difficult to determine visually since it is based largely on hidden factors such as the strength of the reinforcing mat (organic felt or fiberglass), the strength and flexibility of the asphalt, and the amount and type of fillers used. In most cases, however, the guidelines outlined below can help to select shingles that perform as promised.
Organic Felt vs. Fiberglass. Organic shingles are built around a thick inner mat made from wood fibers or recycled paper saturated with soft asphalt. Fiberglass shingles, on the other hand, use a lightweight nonwoven fiberglass held together with phenolic resin. Both shingles are then coated on top with a layer of harder asphalt and fillers and topped with colored stone to create a decorative surface and protect against ultraviolet light. A thin layer of asphalt on the bottom is coated with a nonsticking dusting that keeps the shingles from sticking in the bundle. Each type has its pros and cons (Table 2-2).
Organic. In general, organic shingles have better tear resistance and resistance to nail pull-through than fiberglass shingles, making them less likely to blow away during a cold weather installation when they have not yet had a chance to seal. Also, some roofers find that organic shingles are more pliable and easier to work with in cold weather. On the downside, the organic mat is neither fireproof nor waterproof. Organic shingles therefore typically carry only a Class C fire rating.
Although uncommon, manufacturing defects that allow water penetration into the mat can lead to premature curling and cupping of organic shingles. Blistering and curling in warm climates has also been occasionally reported. Organic shingles cost more than comparable fiberglass shingles, but remain popular in colder regions and throughout Canada. With organic shingles, shingle weight tends to be a good predictor of performance and longevity since the added weight usually indicates a thicker mat saturated with more soft asphalt.
Fiberglass. Fiberglass shingles, built on a thin nonwoven fiberglass core, were first introduced in the late 1970s and now account for over 90% of the shingles sold. Because they use less asphalt, they are lighter and generally less expensive than organic shingles. Because fiberglass mats are more fire-resistant and moisture-resistant than felt, most fiberglass shingles carry a Class A (severe exposure) fire rating and are less prone to cupping and curling from moisture damage. On the downside, fiberglass shingles are generally not as tear-resistant as organic shingles, making them more prone to blow-offs in cold weather when the shingles have not properly sealed. After they have sealed, they can still tear from movement in the sheathing, since fiberglass shingles have little give, unlike organic shingles. In this situation, if the bond strength of the adhesive strip exceeds the tear strength on a lightweight shingle, the shingles can crack.
Premature failure of some fiberglass shingles due to splitting or cracking led to a number of class-action lawsuits in the 1980s and 1990s. The problems were primarily with lower-end shingles with lightweight mats, types that have been largely eliminated from the market. But it still pays to buy ASTM-rated products from a reputable company that provides a good warranty.
Laminated Shingles. Also called "architectural" or "dimensional" shingles, these have two layers laminated together at the lower half of the shingle, giving the roof a thicker textured appearance with deeper shadow lines. Depending on the shape and size of the cutouts, half or more of the exposed shingle area is triple thickness and the rest double. With the added thickness and without the tabs, which typically wear out first in three-tab shingles, most laminated shingles carry longer warranties as well as higher wind ratings, some as high as 120 mph.
While not immune to the problems of other shingles, such as premature cracking, it is reasonable to expect good performance from a reputable brand. One problem unique to laminated shingles is the loosening of the bottommost piece of the shingle caused, in part, by nailing above the line where the double thickness ends (Figure 2-1).
On many laminated shingles, nails must be precisely placed so they are high enough to stay hidden while still penetrating both layers.
Wind Resistance. Most shingles carry a wind-resistance rating of 60 miles per hour as tested under ASTM 3161 or UL 997, while specialty shingles may be rated to as much as 130 miles per hour. While laboratory tests may not predict actual performance in a storm, a higher rated shingle will likely perform better than a lower rated one. Shingles rated at over 100 mph are often special-order items and typically require six rather than the usual four nails per shingle. Adding two extra nails and extra dabs of plastic roofing cement to a regular shingle can also increase its performance in high-wind conditions (see "Fastening," page 58, and "Manual Sealing," page 57).
A wind-resistance rating is not the same as a warranty. Shingles that carry a wind-resistance warranty generally require that the shingle tabs have been adequately sealed to the adhesive strip and most limit wind coverage to five or ten years from installation. In cold, cloudy weather or on a steep north-facing slope, manual sealing with roofing cement may be necessary.
Algae Resistance. Black streaks on shingles caused by algae or fungal growth used to be limited to warm, humid climates, but now this can be seen on houses as far north as Canada. Some experts attribute the spread to the increased use of crushed limestone as a filler material in asphalt shingles. Limestone is economical and makes a durable shingle, but the calcium carbonate in the limestone supports algae growth. In algae-resistant (AR) shingles, zinc or copper granules are mixed in with the colored stone topping. When the shingles get wet, the zinc or copper is released, inhibiting algae growth. Warranties for algae resistance are usually for less than 10 years since the protection ends when the mineral washes away. Some shingles have longer lasting protection than others due to a higher percentage of AR granules.
Manufacturing Standards. Fiberglass shingles are covered by ASTM D3462, which includes a tear test as well as a new nail-pull-through test added after fiberglass shingle failures started occurring in the late 1980s. A new pliability test was also added in recent years. Organic asphalt shingles are covered under their own standard, ASTM D255. In the past, most companies did their own testing, but under pressure from contractors' associations and others, most now use independent certifiers such as UL. With fiberglass shingles, look for the UL label next to the ASTM D3462 certification. This is not the same as a UL listing for a fire rating, which is printed on most fiberglass shingle packages. More and more jurisdictions are requiring compliance with ASTM standards, but discount shingles are still available with no certification.
As with many consensus standards, the ASTM D3462 requirement for tear strength of fiberglass shingles is considered by many experts to be a bare minimum rather than a guarantee of high quality. Also, once installed the shingles' strength will likely diminish. So finding products that exceed the minimum is recommended for demanding applications.
Warranties. Shingle warranties run from 20 to over 50 years. Although products with longer warranties are usually of higher quality, in some cases, the longer warranties are more of a marketing strategy than an accurate predictor of shingle life. While the specific terms of the warranty are important, more important is the manufacturer's reputation for warranty service in the local area. All manufacturers retain the right to void the warranty if installation instructions are not closely followed, and they can often find a way to avoid honoring a claim if so inclined. Key issues to consider in a warranty are as follows:
Is the warranty prorated from the date of installation, or is there an introductory term of 5 to 10 years when the full value can be recovered?
How long are warranties valid against wind damage, algae growth, or other types of damage?
Does the warranty cover a portion of the labor costs of tear-off, disposal, and installation, or does it cover materials only?
Is the warranty transferable?
Perhaps most importantly, does the manufacturer have a strong reputation for warranty service in the local area?
Underlayment
The roof deck should be sound and level before laying the underlayment. Fifteen-pound or heavier felt underlayment is required by code in some areas. Whether or not it is required, underlayment is cheap insurance against problems. There are several good reasons to install underlayment:
It protects the roof deck from rain before the roofing is installed.
It provides an extra weather barrier in case of blowoffs or water penetration through the roofing or flashings.
It protects the roofing from any resins that bleed out of the sheathing.
It helps prevent unevenness in the roof sheathing from telegraphing through the shingles.
It is usually required for the UL fire rating to apply (since shingles are usually tested with underlayment).
Standard Slopes. On roofs with a slope of 4:12 or greater, use a single layer of 15 lb. asphalt-saturated felt, starting at the eaves and lapping upper courses over lower by a minimum of 2 inches. Vertical joints should lap a minimum of 4 inches and be offset by at least 6 feet in successive rows (see Figure 2-2).
Secure each course along seams and edges with enough corrosion-resistant nails to hold it in place until the roofing is installed. In high-wind areas, apply fasteners a maximum of 36 inches on-center along overlaps.
For best protection against leaks, run felt 6 inches over ridges and hips, from each direction, and 6 inches up any adjoining walls. Valleys should be lined with a full width of roofing felt (or bituminous membrane) pushed tight into the valley so there is no slack. Side courses of underlayment should run over the valley lining and extend 6 inches past its edge. (See "Valley Flashing" page 59.)
Low Slopes. Asphalt shingles can be used on roofs with a slope of 2:12 to 4:12 if double-coverage underlayment is used. Start with a 19-inch strip of 15 lb. asphalt-saturated felt along the eaves, and lap succeeding courses by 19 inches as shown in Figure 2-3.
Wherever there is a possibility of ice or snow buildup or the backup of water from leaves or pine needles, install a self-adhering bituminous membrane along the eaves that extends up the roof to a point at least 36 inches inside the interior wall line. An alternative approach, not widely used anymore, is to seal all laps in the lower courses of roofing felt with lap cement or asphalt plastic cement.
In areas with extensive snowfall or windblown rain, the best protection against leakage is to cover the entire low-slope roof area with a bituminous membrane, as shown in Figure 2-4.
Vertical end laps should be at least 3 inches and horizontal laps 6 inches. If the roof changes to a steeper slope, for example, where a shed dormer joins the main roof, extend the membrane 12 to 18 inches up the main roof slope. Bituminous membranes are self-healing around nail holes, and because they bond fully to the sheathing, any leaks that occur cannot spread. As a safeguard against expensive callbacks, many roofers now apply membrane to the entire surface of any roof with a slope of 4:12 or less.
Eaves Flashing. The best defense against ice dams in cold climates is a so-called "cold roof," consisting of high levels of ceiling insulation separated from the roof surface by a free-flowing vent space (see "Preventing Ice Dams," page 97). Where a cold roof cannot be achieved due to complex roof shapes, unvented roofs, or retrofit constraints, ice dams may form during severe winters, in some cases, causing pooled water to wet wall cavities and interior finishes.
Where adequate insulation and ventilation cannot be assured, self-adhering bituminous eaves flashing should be installed. The membrane should go from the lower edge of the roof to a point at least 24 inches inside the interior wall line (Figure 2-5).
Where two lengths of eaves flashing meet at a valley, run each across the valley, starting with the length from the roof with the lower slope or lesser height. The valley flashing should later lap over the eaves flashing.
Skylights. With deep snow, melting water from above and around the skylight can lead to ice dams below. For full protection, some contractors extend the eaves membrane up to the bottom of any skylights and continue it around the sides and top of the skylight. By wrapping the skylight curb with membrane as well, any potential flashing leaks are also eliminated as shown in Figure 2-5 (see also "Skylight Flashing," page 127.)
If it is impractical to install membrane all the way from eaves to skylight, install a 3-foot-wide band of membrane below the skylight, lapping the bottom edge of the membrane over the row of shingles where the membrane terminates.
Drip Edge. Drip edge should always be used along the eaves to kick water away from the fascia, and it is a good idea along rakes as well. Drip edge should lap over the underlayment at the rakes and under it at the eaves (as shown in Figure 2-6). Overlap joints in the drip edge by 2 inches. Shingles can be set even the with the drip edge or overlap by up to 3/4 inch.
Some manufacturers of eaves membranes specify that the drip edge be installed on top of the membrane along the eaves, violating the principle that upper layers of flashing should overlap lower layers. To remedy the problem, the manufacturers suggest using a second strip of membrane to seal the top of the drip edge to the eaves membrane. In practice, however, most installers place the drip edge first and lap the eaves membrane over it, consistent with good building practice.
Installation
Installation Temperature. Ideally, shingles should be installed at temperatures ranging from 40°F to 85°F. Below 40°F, shingles are brittle and crack easily when hammered or bent. Above 85°F, it is easy to tear the shingles or mar the granular coating. In hot temperatures, roofers often start very early in the morning and break at midday. In cold temperatures, it is best to store the shingles in a heated enclosure until they are installed.
Manual Sealing. In cold climates, the sealant strip may not set up properly and may require manual sealing. For three-tab shingles, place two quarter-size spots of plastic roof cement under the lower corners of each tab (as shown in Figure 2-7). With laminated shingles, place four to six quarter-sized dots, spaced evenly, about one inch above the bottom of the overlapping shingle.
Starter Course. After the underlayment and drip edge are installed, a starter course of asphalt shingles, with the tabs removed, is nailed along the eaves so its sealant strip seals down the first course.
(Continues...)
Excerpted from Best Practices Guide to Residential Construction by Steve Bliss Excerpted by permission.
All rights reserved. No part of this excerpt may be reproduced or reprinted without permission in writing from the publisher.
Excerpts are provided by Dial-A-Book Inc. solely for the personal use of visitors to this web site.
Table of Contents
Preface ixAcknowledgments xi
Chapter 1 Exterior Finish 1
Rain-Screen Principle 2
Sheathing Wrap 3
Flashing Membranes 5
Wall Flashing 6
Wood Sidings 9
Wood Shingles and Shakes 15
Fiber-Cement Siding 19
Vinyl Siding 21
Stucco 24
Wood and Composite Trim 29
Trim Details 36
Caulks and Sealants 37
Exterior Adhesives 40
Exterior Wood Finishes 42
Resources 47
Chapter 2 Roofing 51
Asphalt Shingles 51
Clay, Concrete, and Composite Tile 62
Metal Roofing 74
Modular Shingles 80
Wood Shakes and Shingles 85
Low-Slope Roofing 94
Walkable Roofing Membranes 96
Roof Ventilation 97
Resources 101
Chapter 3 Windows and Doors 103
Window Types 103
Window Materials and Construction 105
Window Energy Efficiency 112
Window Flashing 119
Skylights 123
Exterior Doors 127
Resources 132
Chapter 4 Decks and Porches 135
Framing Materials 135
Decking Materials 137
Fasteners 141
Construction Details 144
Rooftop Decks 150
Covered and Screened Porches 151
Finishes for Decking 154
Resources 156
Chapter 5 Interior Finish 159
Drywall 159
Wood Floors 164
Resilient Flooring 176
Laminate Flooring 179
Carpeting 180
Interior Trim 183
Interior Doors 186
Stains and Clear Finishes 188
Sound Control 188
Lighting 194
Resources 206
Chapter 6 Kitchen and Bath 209
Kitchen Design Basics 209
Bathroom Design Basics 217
Kitchen and Bath Flooring 223
Ceramic and Stone Tile 227
Kitchen Cabinets 244
Countertops 247
Plumbing Fixtures 251
Kitchen and Bath Ventilation 261
Resources 264
Chapter 7 Indoor Air Quality 267
Overview 267
Whole-House Ventilation Strategies 270
Air Cleaning Strategies 277
Common Indoor Pollutants and Sources 281
Resources 297
Index 299