The short but concise introduction into the specific properties of this material class focuses on the practical needs of the designer and lays the foundation for the following in-depth discussion of part design suitable for production and the intended end-use application. Numerous detailed examples highlight practical tips and rules of thumb for successful part design.
The short but concise introduction into the specific properties of this material class focuses on the practical needs of the designer and lays the foundation for the following in-depth discussion of part design suitable for production and the intended end-use application. Numerous detailed examples highlight practical tips and rules of thumb for successful part design.
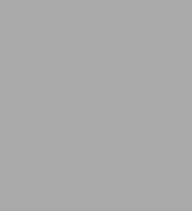
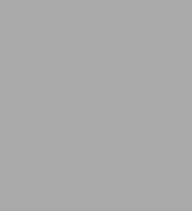
eBook
Available on Compatible NOOK devices, the free NOOK App and in My Digital Library.
Related collections and offers
Overview
The short but concise introduction into the specific properties of this material class focuses on the practical needs of the designer and lays the foundation for the following in-depth discussion of part design suitable for production and the intended end-use application. Numerous detailed examples highlight practical tips and rules of thumb for successful part design.
Product Details
ISBN-13: | 9783446412828 |
---|---|
Publisher: | Hanser Publications |
Publication date: | 01/03/2006 |
Sold by: | Barnes & Noble |
Format: | eBook |
Pages: | 517 |
File size: | 36 MB |
Note: | This product may take a few minutes to download. |
Table of Contents
1 Market Overview 1
1.1 Examples of Applications from Various Industry Sectors 4
1.1.1 Aerospace 4
1.1.2 Precision Engineering 7
1.1.3 Automotive Engineering 9
1.1.4 General Mechanical Engineering 14
1.1.5 Design of Technical Equipment 15
1.1.6 Construction Industry 18
1.2 Forecast 22
2 Structure and Properties 31
2.1 Chemical Structure (Constitution) 31
2.1.1 Degree of Polymerization - Relative Molecular Weight 34
2.1.2 Homopolymerization and Copolymerization 38
2.2 Intermolecular Binding Energies (Secondary Valence Bonds) 40
2.2.1 Absorption of Water by Polyamides 41
2.3 Spatial Arrangement of Atoms and Groups of Atoms in Molecules (Configuration) 47
2.3.1 Tacticity 48
2.3.2 Branching 48
2.3.3 Cross-Linking 49
2.4 Architecture of Polymer Systems 50
2.4.1 Homogeneous and Heterogeneous Polymer Mixtures 50
2.4.2 Plasticization 51
2.4.3 Fillers and Reinforcement 51
2.5 Morphology (Supermolecular Structures) 54
2.5.1 Amorphous Microstructure 54
2.5.2 Crystalline Microstructure 55
2.5.3 Anisotropy 60
2.5.3.1 Molecular Alignments 60
2.5.3.2 Filler or Fiber Alignment 62
2.6 Thermomechanical Ranges 64
2.6.1 Thermoplastics with Amorphous Structure 64
2.6.2 Thermoplastics with Semicrystalline Structure 66
2.6.3 Elastomers 67
2.6.4 Thermosets 67
3 Brief Description of the Properties of Generic Polymeric Materials 71
3.1 Thermoplastics 71
3.1.1 Polymer Blends 80
3.1.2 Functional Polymers 83
3.2 Elastomers 88
3.3 Thermosets 90
3.4 Fibrous Reinforcements 94
3.4.1 Glass Fibers 95
3.4.1.1 Production and Reinforcing Forms of Glass Fiber Material 95
3.4.1.2 Types of Glass and Fiber Properties 96
3.4.2 Carbon Fibers97
3.4.3 Aramid Fibers 97
3.4.4 Metal Fibers, Whiskers, and Ceramic Fibers 97
4 Physical Properties - Characteristic Values - Test Methods and Procedures 101
4.1 Deformation Behavior under Uniaxial Dynamic Tensile Stress (Stress-Strain Experiments) 101
4.1.1 Molecular Deformation and Fracture Mechanisms 101
4.1.2 Characteristic Stress-Strain Curves 103
4.1.3 Determination of Stress-Strain Diagrams and Characteristic Properties of Materials 104
4.1.4 Effects of Temperature, Time, and Humidity on Stress-Strain Curves 107
4.1.5 Mathematical Description of Stress-Strain Curves 109
4.2 Deformation Behavior under Uniaxial, Long-Term, Static Tensile Loads (Tensile Creep Testing) 111
4.2.1 Mathematical Description of Creep Curves 113
4.3 Toughness and Impact Resistance 115
4.3.1 Determination of Tensile Stress-Strain Toughness 116
4.3.2 Determination of Toughness by Flexural Impact Test 116
4.3.3 Penetration or Dart Drop Impact Test 119
4.4 Behavior under Cyclic Loads 120
4.4.1 Determination of Characteristic Features of Fatigue 122
4.5 Poisson's Ratio 125
4.6 Thermal Properties 127
4.6.1 Thermal Expansion 127
4.6.2 Dimensional Stability 129
4.6.2.1 Modulus of Elasticity and Modulus of Rigidity as a Function of Temperature 129
4.6.2.2 Deflection Temperature 130
4.6.2.3 Softening Point 131
4.6.3 Heat Aging 132
4.6.3.1 Safety Considerations and Standards 135
4.6.4 Summary Analysis of the Effects of Temperature 136
4.7 Tribological Properties 136
4.7.1 Fundamentals 138
4.7.1.1 Adhesion and Surface Energy of Solids 139
4.7.1.2 Deformation and Hysteresis Loss 144
4.7.1.3 Boundary Conditions for Adhesive and Deformative Sliding 145
4.7.2 Friction and Wear in Mated Polymer and Steel Surfaces 145
4.7.2.1 Effect of Steel Surface Roughness on Steel/Polymer Combinations 147
4.7.2.2 Effect of Relative Molecular Weight on Friction and Wear 150
4.7.2.3 Effect of the Moisture Content of Polyamides on Friction and Wear 151
4.7.2.4 Effect of High-Energy Radiation 153
4.7.2.5 Effect of Form and Sequence of Motion on Friction and Wear 155
4.7.3 Friction and Wear in Mated Pairs of Polymeric Materials 156
4.7.3.1 Sliding Friction 156
4.7.3.2 Wear Due to Sliding Friction for Mated Polymeric Material Pairs 157
4.7.4.2 The Effects of Physical Properties on Friction and Wear System Properties 158
4.7.5 Effect of Additives on Friction and Wear Properties 158
4.7.5.1 Effect of Fibers on Wear 159
4.7.5.2 Effect of Other Inorganic Additives 163
4.7.5.3 Effect of Polymeric Additives 163
4.7.6 Stick-Slip 165
4.7.6.1 Changing Stick-Slip Behavior by Modifying the Parameters of the Sliding System 166
4.7.7 Jet Erosion 168
5 Calculations for Structures under Mechanical Load - Examples of Geometrically Simple Structural Parts under Static Loads 175
5.1 Specific Materials and Processing Problems 175
5.1.1 Deformation Behavior under Uniaxial Dynamic Tensile Stress 175
5.2 Determination of Strength 177
5.2.1 Basic Procedure for Structural Part Design 177
5.2.1.1 Characteristic Strength 178
5.2.1.2 Safety Factors 180
5.2.1.3 Reducing Factors 181
5.2.2 Uniaxial State of Stress 182
5.2.2.1 Example of a Thin-Walled Pipe under Internal Pressure 183
5.2.3 Multiaxial State of Stress 184
5.2.3.1 Failure Criteria 184
5.2.3.2 Examples of Shear Loads 187
5.3 Calculation of Strains and Deformations 190
5.3.1 Linear Elastic Behavior 190
5.3.2 Nonlinear Elastic Behavior 191
5.4 Analysis of Stress and Deformation in Structures under Flexural Loads with the Aid of a Simple FE Approach 196
5.5 Calculation of Structural Parts Subjected to Impact Loads 198
5.6 Structural Design of Fiber-Composite Structures 199
5.6.1 Mechanical Properties of Laminates 200
5.6.1.1 Deformation Behavior under Uniaxial Tensile Load, Damage Limit 200
5.6.1.2 Fundamental Elasticity Variables in a UD Layer 200
5.6.1.3 Averaged Characteristic Values for Mat Laminates 202
5.6.2 Methods of Calculation 205
5.6.2.1 Calculation of Averaged Values 205
5.6.2.2 Continuum Theory 205
5.6.2.3 Network Theory 205
5.7 Computer-Aided Development 207
5.7.1 Computer-Aided Design (CAD) 207
5.7.2 Rapid Prototyping 208
5.7.3 Rapid Tooling 210
6 Design and Material Considerations for Parts Subjected to Mechanical Loads 213
6.1 Flexible Structures 213
6.1.1 Modulus of Elasticity 213
6.1.2 Design Geometry - Moment of Inertia 214
6.1.3 Load-Geometry Interactions 215
6.2 Flexurally Rigid Structures 218
6.3 Flexurally Flexible, Torsionally Rigid Structures 220
6.4 Flexurally Rigid, Torsionally Flexible Structures 221
6.5 Torsion-Resistant, Torsionally Rigid Structures 221
6.6 Flexurally and Torsionally Rigid Structures 224
6.7 Torsionally Flexible Structures 225
6.8 Tension-Proof, Tensionally Rigid and Torsionally Flexible Structures 225
6.9 High Shear-Strength, Shear-Resistant Structures 226
6.10 Pressure-Yielding and Compression-Resistant Structures 227
6.11 Multifunctional Structures 229
6.12 Thermal Expansion and Thermal Stress 230
6.13 Universal Joints 235
7 Designing for Production 239
7.1 Mold Filling 239
7.1.1 Simulation of the Filling Operation 241
7.1.2 Causes of Orientation in Moldings 243
7.1.2.1 Effects of Orientation 246
7.1.2.2 Controlling Orientation 248
7.1.3 Causes for Formation of Weld Lines and Air Pockets 252
7.1.3.1 Effects of Weld Lines and Air Pockets 254
7.1.3.2 Controlling Weld Lines and Air Pockets 255
7.2 Cooling and Solidification 261
7.2.1 Cooling Rate 261
7.2.1.1 Effects of Cooling Rate 261
7.2.1.2 Controlling the Cooling Rate 261
7.2.2 Changes in Dimensions and Tolerances 264
7.2.2.1 Shrinkage 264
7.2.2.2 Post Molding Shrinkage 267
7.2.2.3 Tolerances 267
7.2.3 Warpage 271
7.2.3.1 Causes of Warpage 271
7.2.3.2 Controlling Warpage 274
7.3 Demolding 277
7.3.1 Draft 280
7.3.2 Demolding of Undercuts 280
7.3.2.1 Forced Demolding 281
7.3.2.2 Mold-Making Measures 281
7.3.2.3 Fusible Cores 283
7.3.3 Avoidance of Undercuts 285
7.3.3.1 Modifying the Design 285
7.3.3.2 Piercing Cores (Blocking or Shutoffs) 285
7.3.3.3 Multipart Designs 287
7.4 Sandwich Molding (Co-Injection Molding) 289
7.4.1 Two-Color Injection Molding 289
7.4.2 Rigid-Flexible Combinations 293
7.4.3 Gas Injection Technology (GIT) 299
7.4.5 External Gas Pressure Technology 303
8 Flexing Elements 311
8.1 Snap-Fit Joints 311
8.1.1 Snap-Fit Beams 317
8.1.1.1 Types of Snap-Fit Beams 317
8.1.1.2 Snap-Fit Beam Calculations 321
8.1.1.3 Additional Functions 322
8.1.2 Torsional Snap-Fit Joints 325
8.1.2.1 Types of Torsional Snap-Fit Joints 325
8.1.2.2 Torsion Snap-Fit Joint Calculations 326
8.1.3 Annular Snap-Fit Joints 327
8.1.3.1 Types of Annular Snap-Fit Joints 327
8.1.3.2 Annular Snap-Fit Joint Calculations 328
8.1.3.3 Additional Functions 330
8.1.4 Segmented Annular Snap-Fit Joints 331
8.1.4.1 Segmented Annular Snap-Fits 332
8.1.4.2 Slotted Annular Snap-Fit Joint Calculations 332
8.1.4.3 Additional Functions 334
8.2 Elastic Elements 335
8.2.1 Elastic Thermoplastic Materials 335
8.2.1.1 Flexing Springs 335
8.2.1.2 Tension Springs 337
8.2.1.3 Compression Springs 337
8.2.1.4 Torsion Springs 341
8.2.2 Springs Made of Fiber-Plastic Composites (Glass-Fiber and Carbon-Fiber Reinforced Plastic) 342
8.2.2.1 Leaf Springs 342
8.3 Integral Hinges and Integral Joints 345
8.3.1 Manufacture of Integral Hinges and Integral Joints 346
8.3.1.1 Injection Molding 346
8.3.1.2 Blow Molding 347
8.3.1.3 Embossing 349
8.3.2 Design 349
8.3.3 Materials 350
8.3.4 Integral Hinge Design Calculations 350
8.3.4.1 Calculation of the Length and Thickness of an Integral Hinge 352
8.3.5 Applications with Integral Hinges 355
8.3.5.1 Lid/Container Hinge Joints 355
8.3.5.2 Bi-Stable Hinge Joints 355
8.3.5.3 Simplified Production 357
8.3.5.4 Dynamically Loaded Integral Hinge Joints 361
8.3.5.5 Assembly Aid and Captive Binding Using Integral Hinges 361
9 Mechanical Fasteners 365
9.1 Molded Threads and Threads Produced by Machining 366
9.1.1 Screws and Bolts Made of Polymeric Material 366
9.1.2 Injection-Molded, Blow-Molded, and Machined Threads 368
9.2 Threaded Inserts 368
9.2.1 Encapsulated Threaded Inserts 368
9.2.2 Threaded Inserts Embedded by Ultrasound 368
9.2.3 Press-In Threaded Inserts 369
9.2.4 Expansion Inserts 370
9.2.5 Screw-In Inserts 370
9.2.6 Inserts Made of Polymeric Materials 371
9.2.7 Comparative Evaluation of the Various Inserts 371
9.2.8 Behavior under Dynamic Loads 374
9.3 Self-Threading Screws 374
9.3.1 Screw Shapes and Geometries 375
9.3.1.1 Included Thread Angle 377
9.3.1.2 Self-Locking Screw Threads 377
9.3.2 Design of the Screw Boss 377
9.3.2.1 Screw Engagement Depth 378
9.3.2.2 Boss Pilot Hole Diameter 378
9.3.2.3 Boss Relief Bore 379
9.3.2.4 Boss Outer Diameter 379
9.3.3 Calculation of Key Variables in a Self-Threading Screw Joint 381
9.3.3.1 Screw Drive Torque 381
9.3.3.2 Destruction Torque 383
9.3.3.3 Screw Extraction (Pull-Out) Force 383
9.3.3.4 Tightening Moment and Tensioning Force 384
9.3.3.5 Assembly Conditions 385
10 Ribbed Structures 387
10.1 Comparison with Other Methods of Reinforcement 387
10.1.1 Increasing the Modulus of Elasticity 387
10.1.2 Increasing Wall Thickness 388
10.1.3 Crimps and Corrugations 389
10.2 General Considerations in Ribbed Structures 390
10.2.1 Rib Height 390
10.2.2 Rib Position 391
10.2.3 Number of Ribs (Consumption of Material) 393
10.2.4 Support 395
10.3 Design Rules for Injection-Molded Ribs 396
10.3.1 Rib Thickness 396
10.3.2 Cooling Time 397
10.3.3 Injection Direction 398
10.3.4 Rib Intersection Points (Nodes) 400
10.4 Design Rules for Ribs Produced by Gas-Assist Molding Methods 401
10.5 Design Rules for Blow-Molded Ribs and Corrugations 403
10.5.1 Blow-Molded Corrugations 403
10.5.2 Blow-Molded Ribs 405
10.6 Design Rules for Compression-Molded Ribs 406
10.6.1 Manual Processing (Hand Lay-Up Process) 406
10.6.2 Compression Molding 407
11 Gear Wheels 411
11.1 Calculation of the Tooth and Tooth Face Temperatures in Spur Gears 413
11.1.1 Blok's Flash Temperature Hypothesis 414
11.1.2 Takanashi Method for Calculating Temperature 414
11.1.3 Hachmann and Strickle Method for Calculating Temperature 416
11.1.4 Comparison of Methods of Calculating Temperature 418
11.1.5 Optimized Temperature Calculation 419
11.1.5.1 Speed of Rotation 420
11.1.5.2 Flank Temperature 420
11.1.5.3 Relative Contact Time 422
11.1.5.4 Optimized Numerical Value Equation 423
11.2 Calculation of Load-Bearing Capacity 424
11.2.1 Tooth Damage 425
11.2.2 General Parameters 426
11.2.3 Calculation of the Load-Bearing Capacity of the Tooth Base 427
11.2.4 Calculation of the Load-Bearing Capacity of the Tooth Flank 434
11.2.5 Calculation of Tooth Deformation 440
11.3 Design 442
11.3.1 Injection Molding 442
11.3.2 Production of Gears by Machining 446
11.3.3 Shaft-Hub Joints 447
11.3.3.1 Press-Fit Joints 447
11.3.3.2 Form-Grip Joints 450
11.3.3.3 Pretensioned Form-Grip Joints 452
12 Friction Bearings 459
12.1 Friction Bearing Damage 461
12.2 Calculation of Load-Bearing Capacity for Bearings 463
12.2.1 Calculation of Mean Bearing Temperature 463
12.2.2 Calculation of Temperature of Sliding Surface 466
12.2.3 Static Load-Bearing Capacity 466
12.2.3.1 Load on the Bearing Material 467
12.2.3.2 Deformation of the Bearing Bushing 471
12.2.4 Dynamic Load-Bearing Capacity 475
12.2.4.1 Continuous Operation 475
12.2.4.2 Intermittent Operation 476
12.2.4.3 Wear 477
12.3 Bearing Design 478
12.3.1 Bearing Clearance 478
12.3.2 Bearing Wall Thickness 480
12.3.3 Bearing Production 481
12.3.4 Design Examples of Bearings 481
13 Wheels and Rollers 485
13.1 Roller Damage 486
13.2 Calculation of Load-Bearing Capacity 488
13.2.1 Pressure Parameter as an Approximate Design Limit 488
13.2.2 Deformation of Rollers under Static Load 492
13.2.3 Rollers under Dynamic Load 498
13.2.3.1 Free-Wheeling Rollers (without Drive) 498
13.2.3.2 Driven Rollers 504
Index 509