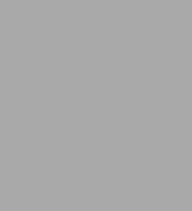
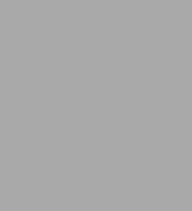
eBook
Related collections and offers
Overview
Written by one of the field’s most well known experts, the Gas Turbine Engineering Handbook has long been the standard for engineers involved in the design, selection, maintenance and operation of gas turbines. With far reaching, comprehensive coverage across a range of topics from design specifications to maintenance troubleshooting, this one-stop resource provides newcomers to the industry with all the essentials to learn and fill knowledge gaps, and established practicing gas turbine engineers with a reliable go-to reference. This new edition brings the Gas Turbine Engineering Handbook right up to date with new legislation and emerging topics to help the next generation of gas turbine professionals understand the underlying principles of gas turbine operation, the economic considerations and implications of operating these machines, and how they fit in with alternative methods of power generation.
- The most comprehensive one-stop source of information on industrial gas turbines, with vital background, maintenance information, legislative details and calculations combined in an essential all-in-one reference
- Written by an industry-leading consultant and trainer and suitable for use as a training companion or a reliable dip-in guide
- Includes hard-won information from industry experts in the form of case histories that offer practical trouble-shooting guidance and solutions
Product Details
ISBN-13: | 9780123838438 |
---|---|
Publisher: | Elsevier Science |
Publication date: | 11/23/2011 |
Sold by: | Barnes & Noble |
Format: | eBook |
Pages: | 1000 |
File size: | 37 MB |
Note: | This product may take a few minutes to download. |
About the Author
Read an Excerpt
Gas Turbine Engineering Handbook
By Meherwan P. Boyce
Elsevier
Copyright © 2012 Elsevier Inc.All rights reserved.
ISBN: 978-0-12-383843-8
CHAPTER 1
An Overview of Gas Turbines
The gas turbine is a power plant that produces a great amount of energy depending on its size and weight. The gas turbine has found increasing service in the past 60 years in the power industry among both utilities and merchant plants as well as the petrochemical industry throughout the world. Its compactness, low weight, and multiple fuel application make it a natural power plant for offshore platforms. Today there are gas turbines that run on natural gas, diesel fuel, naphtha, methane, crude, low-BTU gases, vaporized fuel oils, and biomass gases.
The last 20 years have seen a large growth in gas turbine technology. The growth is spearheaded by the growth of materials technology, new coatings, new cooling schemes, and the growth of combined-cycle power plants. This, with the conjunction of increase in compressor pressure ratio from 7:1 to as high as 45:1, has increased simple-cycle gas turbine thermal efficiency from about 15% to 45%.
Table 1-1 gives an economic comparison of various generation technologies from the initial cost of such systems to the operating costs of these systems. Because distributed generation is very site specific, the cost will vary and the justification of installation of these types of systems will also vary. Sites for distributed generation vary from large metropolitan areas to the slopes of the Himalayan mountain range. The economics of power generation depends on the fuel cost, running efficiencies, maintenance cost, and initial cost, in that order. Site selection depends on environmental concerns such as emissions, noise, fuel availability, size, and weight.
Gas Turbine Cycle in the Combined Cycle or Cogeneration Mode
The utilization of gas turbine exhaust gases, for steam generation or the heating of other heat transfer mediums, or the use of cooling or heating buildings or parts of cities is not a new concept and is currently being exploited to its full potential.
The fossil power plants of the 1990s and into the early part of the new millennium were the combined-cycle power plants, with the gas turbine being the center piece of the plant. It was estimated that, between 1997 and 2006, there was an addition of 147.7 GW of power. These plants have replaced the large steam turbine plants, which were the main fossil power plants through the 1980s. The combined-cycle power plant is not new in concept, since some have been in operation since the mid-1950s. These plants came into their own with the new high-capacity and high-efficiency gas turbines.
The new market place of energy conversion will have many new and novel concepts in combined-cycle power plants. Figure 1-1 shows the heat rates of these plants, present and future, and Figure 1-2 shows the efficiencies of the same plants. The plants referenced are the simple-cycle gas turbine (SCGT) with firing temperatures of 240°F (1315°C), recuperative gas turbine (RGT), the steam turbine (ST) Plant, the combined-cycle power plant (CCPP), and the advanced combined-cycle power plants (ACCPPs), such as combined-cycle power plants using advanced gas turbine cycles, and finally the hybrid power plants (HPP).
Table 1-2 depicts an analysis of the competitive standing of the various types of power plants, their capital cost, heat rate, operation and maintenance costs, availability, reliability, and time for planning. By examining the capital cost and installation time of these new power plants, it is obvious that the gas turbine is the best choice for peaking power. Steam turbine plants are about 50% higher in initial costs of $800–$1000/kW than combined-cycle plants, which are about $400–$900/kW. Nuclear power plants are the most expensive plants. The high initial costs and the long time in construction make such a plant unrealistic for a deregulated utility.
Efficiency and heat rate are interchangeable, as they represent the efficient conversion of fuel to energy. The following relationship gives the easy conversion from heat rate to efficiency.
Efficiency = 3412.2/BTU/kWh = 2544.4/BTU/HPh = 3600/kJ/kWh
In the area of performance, the steam turbine power plants have an efficiency of about 35% when compared with combined-cycle power plants, which have an efficiency of about 55%. Newer gas turbine technology will make combined-cycle efficiencies range between 60% and 65%. As a rule of thumb, a 1% increase in the efficiency could mean that 3.3% more capital can be invested. However, one must be careful that the increase in the efficiency does not lead to a decrease in the availability. From 1996 to 2000, we have seen a growth in the efficiency of about 10% and a loss in the availability of about 10%. This trend must be turned around since many analyses show that a 1% drop in the availability needs about 2–3% increase in the efficiency to offset that loss. The larger gas turbines, just due to their size, take more time to undergo any of the regular inspections, such as combustor, hot gas path, and major overall inspections, thus reducing the availability of these turbines.
The time taken to install a steam plant from conception to production is about 42–60 months whereas it was about 22–36 months for combined-cycle power plants. The actual construction time is about 18 months, whereas obtaining environmental permits in many cases take 12 months and engineering takes 6–12 months. The time taken for bringing the plant online affects the economics of the plant, the longer the capital is employed without return the more it accumulates interest, insurance, and taxes.
It is obvious from this that as long as natural gas or diesel fuel is available, the choice of combined-cycle power plants is obvious.
Gas Turbine Performance
In 1791, John Barber, an Englishman, was the first to patent a design that used the thermodynamic cycle of the modem gas turbine. Figure 1-3 shows the sketch on which he based his patent. His design contained the basics of the modem gas turbine; it had a compressor, a combustion chamber, and a turbine. The main difference between his design and the modern one was that the turbine was equipped with a chain-driven reciprocating type of compressor. He intended its use for jet propulsion.
Many people consider Frank Whittle as the father of the modern-day gas turbine. The Whittle gas turbine was built in January 1930 and had a thrust of 1,000 lbf and an efficiency of 14%. The air was compressed in a centrifugal compressor and was then expanded through a radial-inflow turbine. Figure 1-4 is a photograph of the Whittle turbine and Figure 1-5 is its schematic diagram. In 1903, General Electric developed a turbocharger, and in 1941, it modified the Whittle engine for America's first aero-engine. In 1945, Westinghouse developed the first gas turbine based solely on US design; the turbine included an axial-flow compressor, a turbine, and an annular combustor.
The aerospace engines have been leaders in most of the technology in the gas turbine. The design criteria for these engines were high reliability, high performance, with many starts and flexible operation throughout the flight envelope. The engine life of about 3,500 hours between major overhauls was considered good. The performance of the aerospace engine has always been rated primarily on its thrust/weight ratio. Increase in engine thrust/weight ratio is achieved by developing the blades of high aspect ratio in the compressor as well as optimizing the pressure ratio and firing temperature of the turbine for maximum work output per unit flow.
The industrial gas turbine has always emphasized long life and this conservative approach has resulted in the industrial gas turbine in many aspects giving up high performance for rugged operation. The industrial gas turbine has been conservative in the pressure ratio and the firing temperatures. This has all changed in the last 10 years; spurred on by the introduction of the "aeroderivative gas turbine," the industrial gas turbine has dramatically improved its performance in all operational aspects. This has resulted in a dramatic reduction of the performance gap between these two types of gas turbines. The gas turbine to date in the combined-cycle mode is fast replacing the steam turbine as the base load provider of electrical power throughout the world. This is even true in Europe and the United States of America where the large steam turbines were the only type of base load power in the fossil energy sector. The gas turbine from the 1960s to the late 1980s was used only as peaking power in those countries; it was used as base load mainly in the "developing countries" where the need of power was increasing rapidly and that the waiting period of three to six years for a steam plant was unacceptable.
Figures 1-6 and 1-7 show the growth of the pressure ratio and firing temperature, respectively. The growth of these is parallel to each other, as both growths are necessary to achieve the optimum thermal efficiency.
The increase in pressure ratio increases the gas turbine thermal efficiency when accompanied by the increase in turbine's firing temperature. Figure 1-8 shows the effect on the overall cycle efficiency of the increasing pressure ratio and firing temperature. The increase in the pressure ratio increases the overall efficiency at a given temperature; however, increasing the pressure ratio beyond a certain value at any given firing temperature can actually result in lowering the overall cycle efficiency.
In the past, the gas turbine was perceived as a relatively inefficient power source when compared with other power sources. Its efficiencies were as low as 15% in the early 1950s; however, today its efficiencies are in the range of 45–50%, which translates to a heat rate of 7582 BTU/kW h (8000 kJ/kW h) to 6824 BTU/kW h (7199 kJ/kW h). The limiting factor for most gas turbines has been the turbine inlet temperature. With new schemes of cooling, using steam or conditioned air, and breakthroughs in blade metallurgy, higher turbine temperatures have been achieved. The new gas turbines have fired inlet temperatures as high as 260°F (1427°C) and pressure ratios of 40:1 with the efficiencies of 45% and above.
Gas Turbine Design Considerations
The gas turbine is the best suited prime mover when the needs at hand such as capital cost, time from planning to completion, maintenance costs, and fuel costs are considered. The gas turbine has the lowest maintenance and capital costs among major prime movers. It also has the fastest completion time to full operation among other plants. Its disadvantage was its high heat rate but this has been addressed and the new turbines are among the most efficient types of prime movers. The combination of plant cycles further increases the efficiencies to the low 60% region.
The design of any gas turbine must meet essential criteria based on operational considerations. Chief among these criteria are as follows:
1. High efficiency
2. High reliability and thus high availability
3. Ease of service
4. Ease of installation and commission
5. Conformance with environmental standards
6. Incorporation of auxiliary and control systems that have a high degree of reliability
7. Flexibility to meet various service and fuel needs
A look at each of these criteria will enable the user to get a better understanding of the requirements.
(Continues...)
Excerpted from Gas Turbine Engineering Handbook by Meherwan P. Boyce. Copyright © 2012 Elsevier Inc.. Excerpted by permission of Elsevier.
All rights reserved. No part of this excerpt may be reproduced or reprinted without permission in writing from the publisher.
Excerpts are provided by Dial-A-Book Inc. solely for the personal use of visitors to this web site.
Table of Contents
1. Overview of Gas Turbines 2. Theoretical and Actual Cycle Analysis 3. Compressor and Turbine Performance Characteristics 4. Performance and Mechanical Standards 5. Rotor Dynamics 6. Centrifugal Compressors 7. Axial-Flow Compressors 8. Radial-Inflow Turbines 9. Axial-Flow Turbines 10. Combustors 11. Materials 12. Gas Clean Up System 13. Bearings and Seals 14. Gears 15. Lubrication 16. Spectrum Analysis 17. Balancing 18. Couplings and Alignment 19. Control Systems and Instrumentation 20. Gas Turbine Performance Test 21. Maintenance Techniques 22. Case Studies