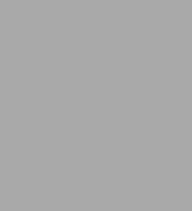
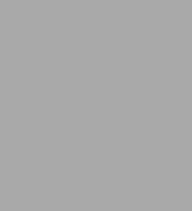
eBook
Related collections and offers
Overview
The history of the helicopter may be traced back to the Chinese flying top (c. 400 B.C.) and to the work of Leonardo da Vinci, who sketched designs for a vertical flight machine utilizing a screw-type propeller. In the late nineteenth century, Thomas Edison experimented with helicopter models, realizing that no such machine would be able to fly until the development of a sufficiently lightweight engine. When the internal combustion gasoline engine came on the scene around 1900, the stage was set for the real development of helicopter technology.
While this text provides a concise history of helicopter development, its true purpose is to provide the engineering analysis required to design a highly successful rotorcraft. Toward that end the book offers thorough, comprehensive coverage of the theory of helicopter flight: the elements of vertical flight, forward flight, performance, design, mathematics of rotating systems, rotary wing dynamics and aerodynamics, aeroelasticity, stability and control, stall, noise and more.
Wayne Johnson has worked for the U.S. Army and NASA at the Ames Research Center in California. Through his company Johnson Aeronautics, he is engaged in the development of software that is used throughout the world for the analysis of rotorcraft. In this book, Dr. Johnson has compiled a monumental resource that is essential reading for any student or aeronautical engineer interested in the design and development of vertical-flight aircraft.
Product Details
ISBN-13: | 9780486131825 |
---|---|
Publisher: | Dover Publications |
Publication date: | 02/08/2012 |
Series: | Dover Books on Aeronautical Engineering |
Sold by: | Barnes & Noble |
Format: | eBook |
Pages: | 1120 |
File size: | 44 MB |
Note: | This product may take a few minutes to download. |
About the Author
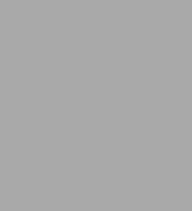
Read an Excerpt
Helicopter Theory
By Wayne Johnson
Dover Publications, Inc.
Copyright © 1980 Wayne JohnsonAll rights reserved.
ISBN: 978-0-486-13182-5
CHAPTER 1
INTRODUCTION
1-1 The Helicopter
The helicopter is an aircraft that uses rotating wings to provide lift, propulsion, and control. Figures 1-1 to 1-3 illustrate the principal helicopter configurations. The rotor blades rotate about a vertical axis, describing a disk in a horizontal or nearly horizontal plane. Aerodynamic forces are generated by the relative motion of a wing surface with respect to the air. The helicopter with its rotary wings can generate these forces even when the velocity of the vehicle itself is zero, in contrast to fixed-wing aircraft, which require a translational velocity to sustain flight. The helicopter therefore has the capability of vertical flight, including vertical take-off and landing. The efficient accomplishment of vertical flight is the fundamental characteristic of the helicopter rotor.
The rotor must efficiently supply a thrust force to support the helicopter weight. Efficient vertical flight means a low power loading (ratio of rotor power required to rotor thrust), because the installed power and fuel consumption of the aircraft are proportional to the power required. For a rotary wing, low disk loading (the ratio of rotor thrust to rotor disk area) is the key to a low power loading. Conservation of momentum requires that the rotor lift be obtained by accelerating air downward, because corresponding to the lift is an equal and opposite reaction of the rotating wings against the air. Thus the air left in the wake of the rotor possesses kinetic energy which must be supplied by a power source in the aircraft if level flight is to be sustained. This is the induced power loss, a property of both fixed and rotating wings that constitutes the absolute minimum of power required for equilibrium flight. For the rotary wing in hover, the induced power loading is found to be proportional to the square root of the rotor disk loading. Hence the efficiency of rotor thrust generation increases as the disk loading decreases. For a given gross weight the induced power is inversely proportional to the rotor radius, and therefore the helicopter is characterized by the large disk area of large diameter rotors. The disk loading characteristic of helicopters is in the range of 100 to 500 N/m2 (2 to 10 1b/ft2). The small diameter rotating wings found in aeronautics, including propellers and turbofan engines, are used mainly for aircraft propulsion. For such applications a high disk loading is appropriate, since the rotor is operating at high axial velocity and at a thrust equal to only a fraction of the gross weight. However, the use of high disk loading rotors for direct lift severely compromises the vertical flight capability in terms of both greater installed power and much reduced hover endurance. The helicopter uses the lowest disk loading of all VTOL (vertical take-off and landing) aircraft designs and hence has the most efficient vertical flight capability. It follows that the helicopter may be defined as an aircraft utilizing large diameter, low disk loading rotary wings to provide the lift for flight.
Since the helicopter must also be capable of translational flight, a means is required to produce a propulsive force to oppose the aircraft and rotor drag in forward flight. For low speeds at least, this propulsive force is obtained from the rotor, by tilting the thrust vector forward. The rotor is also the source of the forces and moments on the aircraft that control its position, attitude, and velocity. In a fixed wing aircraft, the lift, propulsion, and control forces are provided by largely separate aerodynamic surfaces. In the helicopter, all three are provided by the rotor.
Vertical flight capability is not achieved without a cost, which must be weighed against the value of VTOL capability in the desired applications of the aircraft. The task of the engineer is to design an aircraft that will accomplish the required operations with minimum penalty for vertical flight. The price of vertical flight includes a higher power requirement than for fixed wing aircraft, a factor that influences the first cost and operating cost. A large transmission is required to deliver the power to the rotor at low speed and high torque. The fact that the rotor is a mechanically complex system increases first cost and maintenance costs. The rotor is a source of vibration, hence increased maintenance costs, passenger discomfort, and pilot fatigue. There are high alternating loads on the rotor, reducing the structural component life and in general resulting in increased maintenance cost. The stability and control characteristics are often marginal, especially in hover, unless a reliable automatic control system is used. In particular, good instrument flight characteristics are lacking without stability augmentation. Aircraft noise is an increasingly important factor in air transportation, as it is the primary form of interaction of the system with a large part of society. The helicopter is among the quietest of aircraft (or at least it can be), but utilization of its VTOL capability often involves operation close to urban areas, leading to stricter noise requirements in order to achieve its potential. All these factors can be overcome to design a highly successful aircraft. The engineering analysis required for that task is the subject of this book.
1-1.1 The Helicopter Rotor
The conventional helicopter rotor consists of two or more identical, equally spaced blades attached to a central hub. The blades are maintained in uniform rotational motion, usually by a shaft torque from the engine. The lift and drag forces on these rotating wings produce the torque, thrust, and other forces and moments of the rotor. The large diameter rotor required for efficient vertical flight and the high aspect ratio blades required for good aerodynamic efficiency of the rotating wing result in blades that are considerably more flexible than high disk loading rotors such as propellers. Consequently, there is a substantial motion of the rotor blades in response to the aerodynamic forces in the rotary wing environment. This motion can produce high stresses in the blades or large moments at the root, which are transmitted through the hub to the helicopter. Attention must therefore be given in the design of the helicopter rotor blades and hub to keeping these loads low. The centrifugal stiffening of the rotating blade results in the motion being predominantly about the blade root. Hence the design task focuses on the configuration of the rotor hub.
A frequent design solution that was adopted early in the development of the helicopter and only recently altered is to use hinges at the blade root that allow free motion of the blade normal to and in the plane of the disk. A schematic of the root hinge arrangement is given in Fig 1-4. Because the bending moment is zero at the blade hinge, it must be low throughout the root area, and no hub moment is transmitted through the blade root to the helicopter. This configuration makes use of the blade motion to relieve the bending moments that would otherwise arise at the root of the blade. The motion of the blade allowed by these hinges has an important role in the behavior of the rotor and in the analysis of that behavior. Some current rotor designs eliminate the hinges at the root, so that the blade motion involves structural bending. The hub and blade loads are necessarily higher than for a hinged design. The design solution is basically the same, however, because the blade must be provided with enough flexibility to allow substantial motion, or the loads would be intolerable even with advanced materials and design technology. Hence blade motion remains a dominant factor in rotor behavior, although the root load and hub moment capability of a hingeless blade has a significant influence on helicopter design and operating characteristics.
The motion of a hinged blade consists basically of rigid body rotation about each hinge, with restoring moments due to the centrifugal forces acting on the rotating blade. Motion about the hinge lying in the rotor disk plane (and perpendicular to the blade radial direction) produces out-of-plane deflection of the blade and is called flap motion. Motion about the vertical hinge produces deflection of the blade in the plane of the disk and is called lag motion (or lead-lag). For a blade without hinges the fundamental modes of out-of-plane and in-plane bending define the flap and lag motion. Because of the high centrifugal stiffening of the blade these modes are similar to the rigid body rotations of hinged blades, except in the vicinity of the root, where most of the bending takes place. In addition to the flap and lag motion, the ability to change the pitch of the blade is required in order to control the rotor. Pitch motion allows control of the angle of attack of the blade, and hence control of the aerodynamic forces on the rotor. This blade pitch change, called feathering motion, is usually accomplished by movement about a hinge or bearing. The pitch bearing on a hinged blade is usually outboard of the flap and lag hinges; on a hingeless blade the pitch bearing may be either inboard or outboard of the major flap and lag bending at the root. There are also rotor designs that eliminate the pitch bearings as well as the flap and lag hinges; the pitch motion then occurs about a region of torsional flexibility at the blade root.
The mechanical arrangement of the rotor hub to accommodate the flap and lag motion of the blade provides a fundamental classification of rotor types as follows:
a. Articulated rotor. The blades are attached to the hub with flap and lag hinges.
b. Teetering rotor. Two blades forming a continuous structure are attached to the rotor shaft with a single flap hinge in a teetering or seesaw arrangement. The rotor has no lag hinges. Similarly, a gimballed rotor has three or more blades attached to the hub without hinges, and the hub is attached to the rotor shaft by a gimbal or universal joint arrangement.
c. Hingeless rotor. The blades are attached to the hub without flap or lag hinges, although often with a feathering bearing or hinge. The blade is attached to the hub with cantilever root restraint, so that blade motion occurs through bending at the root. This rotor is also called a rigid rotor. However, the limit of a truly rigid blade, which is so stiff that there is no significant motion, is applicable only to high disk loading rotors.
1-1.2 Helicopter Configuration
The arrangement of the rotor or rotors on a helicopter is perhaps its most distinctive external feature and is an important factor in its behavior, notably its stability and control characteristics. Usually the power is delivered to the rotor through the shaft, accompanied by a torque. The aircraft in steady flight can have no net force or moment acting on it, and therefore the torque reaction of the rotor on the helicopter must be balanced in some manner. The method chosen to accomplish this torque balance is the primary determinant of the helicopter configuration. Two methods are in general use; a configuration with a single main rotor and a tail rotor, and configurations with twin contrarotating rotors.
The single main rotor and tail rotor configuration uses a small auxiliary rotor to provide the torque balance (and yaw control). This rotor is on the tail boom, typically slightly beyond the edge of the main rotor disk. The tail rotor is normally vertical, with its shaft horizontal and parallel to the helicopter lateral axis. The torque balance is produced by the tail rotor thrust acting on an arm about the main rotor shaft. The main rotor provides lift, propulsive force, and roll, pitch, and vertical control for this configuration.
A twin main rotor configuration uses two contrarotating rotors, of equal size and loading, so that the torques of the rotors are equal and opposing. There is then no net yaw moment on the helicopter due to the main rotors. This configuration automatically balances the main rotor torque without requiring a power-absorbing auxiliary rotor. The rotor-rotor aerodynamic interference losses absorb about the same amount of power, however. The most frequent twin rotor arrangement is the tandem helicopter configuration-fore and aft placement of the main rotors on the fuselage usually with significant overlap of the rotor disks and with the rear rotor raised vertically above the front rotor. A side-by-side twin rotor arrangement has also found some application.
1-1.3 Helicopter Operation
Operation in vertical flight, with no translational velocity, is the particular role for which the helicopter is designed. Operation with no velocity at all relative to the air, either vertical or translational, is called hover. Lift and control in hovering flight are maintained by rotation of the wings to provide aerodynamic forces on the rotor blades. General vertical flight involves climb or descent with the rotor horizontal, and hence with purely axial flow through the rotor disk. A useful aircraft must be capable of translational flight as well. The helicopter accomplishes forward flight by keeping the rotor nearly horizontal, so that the rotor disk sees a relative velocity in its own plane in addition to the rotational velocity of the blades. The rotor continues to provide lift and control for the aircraft. It also provides the propulsive force to sustain forward flight, by means of a small forward tilt of the rotor thrust.
Safe operation after loss of power is required of any successful aircraft. The fixed wing aircraft can maintain lift and control in power-off flight, descending in a glide at a shallow angle. Rotary wing aircraft also have the capability of sustaining lift and control after a loss of power. Power-off descent of the helicopter is called autorotation. The rotor continues to turn and provide lift and control. The power required by the rotor is taken from the air flow provided by the aircraft descent. The procedure upon recognition of loss of power is to set the controls as required for autorotative descent, and establish equilibrium flight at the minimum descent rate. Then near the ground the helicopter is flared, using the rotor-stored kinetic energy of rotation to eliminate the vertical and translational velocity just before touchdown. The helicopter rotor in vertical power-off descent has been found to be nearly as effective as a parachute of the same diameter as the rotor disk; about half that descent rate is achievable in forward flight.
A rotary wing aircraft called the autogiro uses autorotation as the normal working state of the rotor. In the helicopter, power is supplied directly to the rotor, and the rotor provides propulsive force as well as lift. In the autogiro, no power or shaft torque is supplied to the rotor. The power and propulsive force required to sustain level forward flight are supplied by a propeller or other propulsion device. Hence the autogiro is like a fixed-wing aircraft, since the rotor takes the role of the wing in providing only lift for the vehicle, not propulsion. Sometimes the aircraft control forces and moments are supplied by fixed aerodynamic surfaces as in the airplane, but it is better to obtain the control from the rotor. The rotor performs much like a wing, and has a fairly good lift-to-drag ratio. Although rotor performance is not as good as that of a fixed wing, the rotor is capable of providing lift and control at much lower speeds. Hence the autogiro is capable of flight speeds much slower than fixed-wing aircraft. Without power to the rotor itself, however, it is not capable of actual hover or vertical flight. Because autogiro performance is not that much better than the performance of an airplane with a low wing loading, it has usually been found that the requirement of actual VTOL capability is necessary to justify the use of a rotor on an aircraft.
1-2 History
The initial development of rotary-wing aircraft faced three major problems that had to be overcome to achieve a successful vehicle. The first problem was to find a light and reliable engine. The reciprocating internal combustion engine was the first to fulfill the requirements, and much later the adoption of the turboshaft engine for the helicopter was a significant advance. The second problem was to develop a light and strong structure for the rotor, hub, and blades while maintaining good aerodynamic efficiency. The final problem was to understand and develop means of controlling the helicopter, including balancing the rotor torque. These problems were essentially the same as those that faced the development of the airplane and were solved eventually by the Wright brothers. The development of the helicopter in many ways paralleled that of the airplane. That helicopter development took longer may be attributed to the cost of vertical flight, which required a higher development of aeronautical technology before the problems could be satisfactorily overcome.
(Continues...)
Excerpted from Helicopter Theory by Wayne Johnson. Copyright © 1980 Wayne Johnson. Excerpted by permission of Dover Publications, Inc..
All rights reserved. No part of this excerpt may be reproduced or reprinted without permission in writing from the publisher.
Excerpts are provided by Dial-A-Book Inc. solely for the personal use of visitors to this web site.
Table of Contents
AcknowledgementsNotation
1. Introduction
1-1 The Helicopter
1-1.1 The Helicopter Rotor
1-1.2 Helicopter Configuration
1-1.3 Helicopter Operation
1-2 History
1-2.1 Helicopter Development
1-2.2 Literature
1-3 Notation
1-3.1 Dimensions
1-3.2 Physical Description of the Blade
1-3.3 Blade Aerodynamics
1-3.4 Blade Motion
1-3.5 Rotor Angle of Attack and Velocity
1-3.6 Rotor Forces and Power
1-3.7 Rotor Disk Planes
1-3.8 NACA Notation
2. Vertical Flight I
2-1 Momentum Theory
2-1.1 Actuator Disk
2-1.2 Momentum Theory in Hover
2-1.3 Momentum Theory in Climb
2-1.4 Hover Power Losses
2-2 Figure of Merit
2-3 Extended Momentum Theory
2-3.1 Rotor in Hover or Climb
2-3.2 Swirl in the Wake
2-3.3 Swirl Due to Profile Torque
2-4 Blade Element Theory
2-4.1 History of the Development of Blade Element Theory
2-4.2 Blade Element Theory for Vertical Flight
2-4.2.1 Rotor Thrust
2-4.2.2 Induced Velocity
2-4.2.3 Power or Torque
2-5 Combined Blade Element and Momentum Theory
2-6 Hover Performance
2-6.1 Tip Losses
2-6.2 Induced Power Due to Nonuniform Inflow and Tip Losses
2-6.3 Root Cutout
2-6.4 Blade Mean Lift Coefficient
2-6.5 Equivalent Solidity
2-6.6 The Ideal Rotor
2-6.7 The Optimum Hovering Rotor
2-6.8 Effect of Twist and Taper
2-6.9 Examples of Hover Polars
2-6.10 "Disk Loading, Span Loading, and Circulation"
2-7 Vortex Theory
2-7.1 Vortex Representation of the Rotor and Its Wake
2-7.2 Actuator Disk Vortex Theory
2-7.3 Finite Number of Blades
2-7.3.1 Wake Structure for Optimum Rotor
2-7.3.2 Prandtl's Tip Loading Solution
2-7.3.3 Goldstein's Propeller Analysis
2-7.3.4 Applications to Low Inflow Rotors
2-7.4 Nonuniform Inflow (Numerical Vortex Theory)
2-7.5 Literature
2-8 Literature
3. Vertical Flight II
3-1 Induced Power in Vertical Flight
3-1.1 Momentum Theory for Vertical Flight
3-1.2 Flow States of the Rotor in Axial Flight
3-1.2.1 Normal Working State
3-1.2.2 Vortex Ring State
3-1.2.3 Turbulent Wake State
3-1.2.4 Windmill Brake State
3-1.3 Induced Velocity Curve
3-1.3.1 Hover Performance
3-1.3.2 Autorotation
3-1.3.3 Vortex Ring State
3-1.4 Literature
3-2 Autorotation in Vertical Descent
3-3 Climb in Vertical Flight
3-4 Vertical Drag
3-5 Twin Rotor Interference in Hover
3-6 Ground Effect
4. Forward Flight I
4-1 Momentum Theory in Forward Flight
4-1.1 Rotor Induced Power
4-1.2 "Climb, Descent, and Autorotation in Forward Flight"
4-1.3 Tip Loss Factor
4-2 Vortex Theory in Forward Flight
4-2.1 Classical Vortex Theory Results
4-2.2 Induced Velocity Variation in Forward Flight
4-2.3 Literature
4-3 Twin Rotor Interference in Forward Flight
4-4 Ground Effect in Forward Flight
5. Forward Flight II
5-1 The Helicopter Rotor in Forward Flight
5-2 Aerodynamics of Forward Flight
5-3 Rotor Aerodynamic Forces
5-4 Power in Forward Flight
5-5 Rotor Flapping Motion
5-6 Examples of Performance and Flapping in Forward Flight
5-7 Review of Assumptions
5-8 Tip Loss and Root Cutout
5-9 Blade Weight Moment
5-10 Linear Inflow Variation
5-11 Higher Harmonic Flapping Motion
5-12 Profile Power and Radial Flow
5-13 Flap Motion with a Hinge Spring
5-14 Flap Hinge Offset
5-15 Hingeless Rotor
5-16 Gimballed or Teetering Rotor
5-17 Pitch-Flap Coupling
5-18 "Helicopter Force, Moment, and Power Equilibrium"
5-19 Lag Motion
5-20 Reverse Flow
5-21 Compressibility
5-22 Tail Rotor
5-23 Numerical Solutions
5-24 Literature
6. Performance
6-1 Hover Performance
6-1.1 Power Required in Hover and Vertical Flight
6-1.2 Climb and Descent
6-1.3 Power Available
6-2 Forward Flight Performance
6-2.1 Power Required in Forward Flight
6-2.2 Climb and Descent in Forward Flight
6-2.3 D/L Formulation
6-2.4 Rotor Lift and Drag
6-2.5 P/T Formulation
6-3 Helicopter Performance Factors
6-3.1 Hover Performance
6-3.2 Minimum Power Loading in Hover
6-3.3 Power Required in Level Flight
6-3.4 Climb and Descent
6-3.5 Maximum Speed
6-3.6 Maximum Altitude
6-3.7 Range and Endurance
6-4 Other Performance Problems
6-4.1 Power Specified (Autogyro)
6-4.2 Shaft Angle Specified (Tail Rotor)
6-5 Improved Performance Calculations
6-6 Literature
7. Design
7-1 Rotor Types
7-2 Helicopter Types
7-3 Preliminary Design
7-4 Helicopter Speed Limitations
7-5 Autorotational Landings after Power Failure
7-6 Helicopter Drag
7-7 Rotor Blade Airfoil Selection
7-8 Rotor Blade Profile Drag
7-9 Literature
8. Mathematics of Rotating Systems
8-1 Fourier Series
8-2 Sum of Harmonics
8-3 Harmonic Analysis
8-4 Fourier Coordinate Transformation
8-4.1 Transformation of the Degrees of Freedom
8-4.2 Conversion of the Equations of Motion
8-5 Eigenvalues and Eigenvectors of the Rotor motion
8-6 "Analysis of Linear, Periodic Systems"
8-6.1 "Linear, Constant Coefficient Equations"
8-6.2 "Linear, Periodic Coefficient Equations"
9. Rotary Wing Dynamics I
9-1 Sturm-Liouville Theory
9-2 Out-of-Plane Motion
9-2.1 Rigid Flapping
9-2.2 Out-of-Plane Bending
9-2.3 Nonrotating Frame
9-2.4 Bending Moments
9-3 In-plane Motion
9-3.1 Rigid Flap and Lag
9-3.2 In-Plane Bending
9-3.3 In-Plane and Out-of-Plane Bending
9-4 Torsional Motion
9-4.1 Rigid Pitch and Flap
9-4.2 Structural Pitch-Flap and Pitch-Lag Coupling
9-4.3 Torsion and Out-of-Plane Bending
9-4.4 Nonrotating Frame
9-5 Hub Reactions
9-5.1 Rotating Loads
9-5.2 Nonrotating Loads
9-6 Shaft Motion
9-7 Coupled Flap-Lag Torsion Motion
9-8 Rotor Blade Bending Modes
9-8.1 Engineering Beam Theory for a Twisted Blade
&nbs
10-8.2 Finite-Length Vortex Line Element
10-8.3 Rectangular Vortex Sheet
11. Rotary Wing Aerodynamics II
11-1 Section Aerodynamics
11-2 Flap Motion
11-3 Flap and Lag Motion
11-4 Nonrotating Frame
11-5 Hub Reactions
11-5.1 Rotating Frame
11-5.2 Nonrotating Frame
11-6 Shaft Motion
11-7 Summary
11-8 Pitch and Flap Motion
12. Rotary Wing Dynamics II
12-1 Flapping Dynamics
12-1.1 Rotating Frame
12-1.1.1 Hover Roots
12-1.1.2 Forward Flight Roots
12-1.1.3 Hover Transfer Function
12-1.2 Nonrotating Frame
12-1.2.1 HoverRoots and Modes
12-1.2.2 Hover Transfer Functions
12-1.3 Low Frequency Response
12-1.4 Hub Reactions
12-1.5 Two-Bladed Rotor
12-1.6 Literature
12-2 Flutter
12-2.1 Pitch-Flap Equations
12-2.2 Divergence Instability
12-2.3 Flutter Instability
12-2.4 Other Factors Influencing Pitch-Flap Stability
12-2.4.1 Shed Wake Influence
12-2.4.2 Wake-Excited Flutter
12-2.4.3 Influence of Forward Flight
12-2.4.4 Coupled Blades
12-2.4.5 Additional Degrees of Freedom
12-2.5 Literature
12-3 Flap-Lag Dynamics
12-3.1 Flap-Lag Equations
12-3.2 Articulated Rotors
12-3.3 Hingeless Rotors
12-3.4 Improved Analytical Models
12-3.5 Literature
12-4 Ground Resonance
12-4.1 Ground Resonance Equations
12-4.2 No-Damping Case
12-4.3 Damping Required for Ground Resonance Stability
12-4.4 Two-Bladed Rotor
12-4.5 Literature
12-5 Vibration and Loads
12-5.1 Vibration
12-5.2 Loads
12-5.3 Calculation of Vibration and Loads
12-5.4 Blade Frequencies
12-5.5 Literature
13. Rotary Wing Aerodynamics III
13-1 Rotor Vortex Wake
13-2 Nonuniform Inflow
13-3 Wake Geometry
13-4 Vortex-Induced Loads
13-5 Vortices and Wakes
13-6 Lifting-Surface Theory
13-7 Boundary Layers
14 Helicopter Aeroelasticity
14-1 Aeroelastic Analyses
14-2 Integration of the Equations of Motion
14-3 Literature
15 Stablity and Control
15-1 Control
15-2 Stability
15-3 Flying Qualities in Hover
15-3.1 Equations of Motion
15-3.2 Vertical Dynamics
15-3.3 Yaw Dynamics
15-3.4 Longitudinal Dynamics
15-3.4.1 Equations of Motion
15-3.4.2 Poles and Zeros
15-3.4.3 Loop Closures
15-3.4.4 Hingeless Rotors
15-3.4.5 Response to Control
15-3.4.6 Examples
15-3.4.7 Flying Qualities Characteristics
15-3.5 Lateral Dynamics
15-3.6 Coupled Longitudinal and Lateral Dynamics
15-3.7 Tandem Helicopters
15-4 Flying Qualities in Forward Flight
15-4.1 Equations of Motion
15-4.2 Longitudinal Dynamics
15-4-2.1 Equations of Motion
15-4-2.2 Poles
15-4-2.3 Short Period Approximation
15-4-2.4 Static Stability
15-4-2.5 Example
15-4-2.6 Flying Qualities Characteristics
15-4.3 Lateral Dynamics
15-4.4 Tandem Helicopters
15-4.5 Hingeless Rotor Helicopters
15-5 Low Frequency Rotor Response
15-6 Stability Augmentation
15-7 Flying Qualities Specifications
15-8 Literature
16 Stall
16-1 Rotary Wing Stall Characteristics
16-2 NACA Stall Research
16-3 Dynamic Stall
16-4 Literature
17 Noise
17-1 Helicopter Rotor Noise
17-2 Vortex Noise
17-3 Rotational Noise
17-3.1 Rotor Pressure Distribution
17-3.2 Hovering Rotor with Steady Loading
17-3.3 Vertical Flight and Steady Loading
17-3.4 Stationary Rotor with Unsteady Loading
17-3.5 Forward Flight and Steady Loading
17-3.6 Forward Flight and Unsteady Loading
17-3.7 Thickness Noise
17-3.8 Rotating Frame Analysis
17-3.9 Doppler Shift
17-4 Blade Slap
17-5 Rotor Noise Reduction
17-6 Literature
Cited Literature
Index