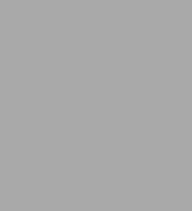
Lean Six Sigma Logistics: Strategic Development to Operational Success
304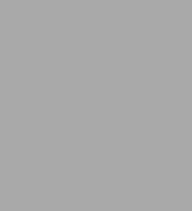
Lean Six Sigma Logistics: Strategic Development to Operational Success
304eBook
Available on Compatible NOOK devices, the free NOOK App and in My Digital Library.
Related collections and offers
Overview
Product Details
ISBN-13: | 9781604277067 |
---|---|
Publisher: | Ross, J. Publishing, Incorporated |
Publication date: | 08/01/2005 |
Sold by: | Barnes & Noble |
Format: | eBook |
Pages: | 304 |
File size: | 7 MB |
About the Author
Read an Excerpt
CHAPTER 1
WHAT IS LEAN SIX SIGMA LOGISTICS?
Lean Six Sigma Logistics. Although it may sound as if it would require a yearlong training course to do the topic justice, most logisticians are in fact using Lean Six Sigma Logistics techniques without realizing it. As the competitive environment changes the way we do business, companies are embracing Lean and Six Sigma initiatives to support cost reductions and quality improvements. Although Lean and Six Sigma programs were separate initiatives in most organizations initially, today's firms see that Lean and Six Sigma do not compete against but rather complement each other and provide for dovetailing of continuous improvement activities.
But what does this have to do with logistics? The quick answer is "everything." Once grounded in Lean and Six Sigma principles, the logistician will realize that logistics, Lean, and Six Sigma form a natural union. This union leverages the strengths and weaknesses of each discipline to create a cultural and operational model that will aid the logistician to solve age-old issues while improving operations and contributing to business success at all levels.
Where does one start when dealing with a topic as complex as Lean Six Sigma Logistics? Mathematicians have shown us that Y is a function of X, so if we truly want to understand Y (Lean Six Sigma Logistics), the best place to start is with the Xs. In this case, the Xs we need to understand individually are logistics, Lean, and Six Sigma. Once we can envision the three focus areas on their own, then we can see how they come together, allowing the whole to be greater than the sum of the parts.
WHAT IS LOGISTICS?
There seem to be as many definitions of "logistics" as there are logisticians. And this is not a bad thing! Why? Because logistics is so far-reaching and yet so integrated into our businesses that it is hard for one definition ever to meet the challenge of summing up what we do in a few short sentences.
Although logistics does involve internal operations and stretches to up- and downstream trading partners in the supply chain, it is fair to say that any definition of logistics will need to involve the management of inventory, whether it is in the form of hard goods (materials, people) or soft goods (information). If there is no inventory to move around, there is no need for logistics.
WHAT IS LEAN?
"Lean" concepts are deeply rooted in the Toyota Production System. In its purest form, Lean is about the elimination of waste and the increase of speed and flow. Although this is a high-level oversimplification, the ultimate objective of Lean is to eliminate waste from all processes. According to Lean theory, at the top of the list of known wastes is excess inventory. More simply, we need to eliminate any inventory that is not required to support operations and the immediate need of the customer. In this book, we identify excess inventory along with six other potential sources of waste in logistics: transportation, space and facilities, time, packaging, administration, and knowledge. Clearly, each of these resources — all necessary for logistics planning and execution — becomes waste when not utilized effectively to generate: (1) the greatest possible value in the eyes of customers and (2) healthy return for the company.
Lean and the Logistician
The impact of Lean on the logistician is significant. A common misconception of the Lean philosophy is that it only finds application in manufacturing settings. The goal of Lean is to eliminate waste, decrease work-in-process inventories, and, in turn, decrease process and manufacturing lead times, ultimately increasing supply chain velocity and flow. Lean also has a vital cultural element to it that is crucial to the logistician, the concept of "total cost." The Lean practitioner does not focus on individual cost factors such as transportation or warehousing, but rather focuses on total cost. With inventory carrying costs representing 15 to 40 percent of total logistics costs for many industries, making decisions based on total cost has dramatic implications for the logistician. Unfortunately though, many organizations never embrace the total cost concept fully, as poor decisions are made continually based on traditionally visible cost drivers like transportation, warehousing, and per-unit purchase prices.
WHAT IS SIX SIGMA?
Six Sigma is a management methodology that attempts to understand and eliminate the negative effects of variation in our processes. Based on an infrastructure of trained professionals (black belts), Six Sigma delivers a problem-solving model armed with "voice of the customer" utilities and statistical process control tools. Define-Measure-Analyze-Improve-Control (DMAIC) is a map, or step-by-step approach, to understand and improve on organizational challenges (see Chapter 21). Six Sigma-trained employees will work on "projects" using the DMAIC model to reduce variation in processes and to attempt to achieve "Six Sigma quality," a statistical reference to 3.4 defects per million opportunities.
At the heart of Six Sigma is the principle of variation reduction: If we can understand and reduce variation in our processes, then we can implement improvement initiatives that will center the process and ensure accuracy and reliability of the process around customer expectations. For example, an average order-to-delivery cycle time of five days may reflect a variation between two and eight days. It is this variation that leads to customer nonconfidence and the resultant inventory buildup and/or loss of sales.
Six Sigma and the Logistician
The concept of variation reduction is paramount to the logistician. As stated above, logistics is about managing inventory, and managing inventory is about managing variance. If we look at the different types of inventory, we will plainly see why variation plays such a vital role in how we manage inventories throughout the business and the supply chain.
For example, safety or "buffer" stocks are inventories that we need to hedge against unknowns (i.e., the variations from the norm). That is, we maintain safety stocks because of variation in supplier quality, transportation reliability, manufacturing process capability, and customer demand patterns. In other words, if we can understand and control variation in our processes from supplier to customer, then we will be able to reduce our reliance on the buffers dramatically. In this regard, logisticians need to think of themselves as actuaries, like those who develop rates for automobile insurance. Actuaries look at key variables — the age of drivers, gender of the drivers, types of vehicle driven, measures of past behavior (e.g., speeding tickets and accidents) — and then they determine insurance rates that reflect the variability in the data. This is precisely why the sixteen-year-old male who drives a sports car will have the highest insurance rates!
Logisticians are no different than the actuaries in this analogy. For demographics and sports cars, the logistician substitutes supplier competence, transportation reliability, and demand fluctuation. Then the logistician determines the "insurance rate," using inventory as the unit of currency. The problem here, though, is that too many logisticians are treating their companies like teenage drivers when, in fact, the company performance is more like a middle-aged soccer parent who drives a minivan. A down-to-earth example of this is when a manufacturer has leveled demand from a supplier who is an hour down the road from the plant, yet the manufacturer continues to carry twelve days worth of that supplier's parts in inventory! Why? Most likely the answer is twofold. The first reason is that the leveled flow (and therefore low variability of demand) is not understood; the second reason is more emotional. The emotional part of the equation is simply that industry is addicted to inventory. Make no mistake about it — industry has an addiction to inventory, and as with any addiction, inventory is something that most companies cannot imagine living without.
WHAT IS LEAN SIX SIGMA LOGISTICS?
Now that we have explored the three elements of Lean Six Sigma Logistics, we need to put them together to appreciate fully how they dovetail and complement each other. Summarizing from the above, recall that:
1. Logistics is about managing inventory.
2. Lean is about speed, flow, and the elimination of waste.
3. Six Sigma is about understanding and reducing variation.
Therefore, Lean Six Sigma Logistics can be defined as:
The elimination of wastes through disciplined efforts to understand and reduce variation, while increasing speed and flow in the supply chain.
The Logistics Bridge Model
Both Lean and Six Sigma lend distinctive disciplines and tools to logistics. Using these disciplines and tools will allow an organization to uncover and deal with wastes and inefficiencies. Although Lean and Six Sigma tools are very powerful, we need to remember that for Lean and Six Sigma to work in logistics, a fundamental mind shift must occur. This mind shift requires that we first begin to make decisions based on the concept of "total logistics costs," and second, we have the courage to eliminate waste in its various forms. This may sound simple, but reality will prove otherwise. Organizational norms, management tradition, and financial accounting methods will fight against "total cost" and will continue to support our natural tendencies to create waste. The purpose of this book is to provide a template for the design and implementation of a logistics strategy based on Lean and Six Sigma principles. We have called this template the Logistics Bridge Model.
The Logistics Bridge Model is a model that can be used as a compass for the logistics professional. That is, it will provide direction and insight on how to solve today's logistics challenges and set the course for ongoing success. At the heart of these challenges is the need to bridge our suppliers with our own processes and then bridge our processes to the customer. All of this must happen while we face competitive and shareholder pressures to reduce costs and increase market share.
The Logistics Bridge Model teaches us that Lean Six Sigma Logistics is made up of three main principles. These principles are:
1. Logistics Flow
2. Logistics Capability
3. Logistics Discipline
Logisticians can draw from these three principles to design their own, personally tailored solutions to meet the specific challenges faced by their organization. Our goal is to provide the logistics professional with guiding principles that can be used to solve any logistics challenge that might be faced. To accomplish this, we have divided the book into four sections.
In Section 1, we continue to explore the importance of excellence in logistics and supply chain management. Section 2 examines the wastes that are all too often created in the absence of Lean Six Sigma implementation. Section 3 provides the details of the Logistics Bridge Model, the guiding principles to Lean Six Sigma Logistics. We illustrate the key tenets to logistics strategic visioning, tactical development, and successful operational execution. Section 4introduces key methods and tools that can be utilized for strategy development,problem solving, measurement, and Lean Six Sigma Logistics implementation. Toward the close of the book, a real-world example is provided as an exercise in critical thinking and problem solving related to Lean Six Sigma Logistics.
As the authors, it is our hope that this book will provide you as a logistics professional with the "golden nugget" for which you have been searching. Whether you have responsibility for a distribution facility or a global supply chain, Lean Six Sigma Logistics has much to offer. The same holds true whether you work in the commercial sector, for a nonprofit organization, or for a government entity. At a minimum, we trust that you will learn new principles that can be added to your current operations and strategy. At best, the logistics professional can use the Logistics Bridge Model to design, develop, and implement a comprehensive logistics strategy.
CHAPTER 2THE IMPORTANCE OF LOGISTICS AND SUPPLY CHAIN MANAGEMENT
If you were asked to generate a list of the world's best companies — companies that enjoy sustainable growth and healthy margins — which would you include? Would companies like Wal-Mart, Toyota, 3M, and Dell come to mind? How do companies like these somehow manage to stay ahead of the curve, to lead where others must follow? What is it that makes companies like these stand out from the crowd? Is it that their assortment and quality of products clearly outshine those of competitors? Possibly. Is it that they communicate the inherent value of their products better than their competitors? Maybe. Is it that they enjoy considerable channel power and negotiate favorable terms with suppliers? Perhaps. Is it that their supply chains and integrated logistics operations provide distinctive competitive advantage? Definitely. While these pillars of modern-day business achievement provide desired products at a good value to customers, all four have their supply chains to credit for much of their success.
DISCOVERING THE DARK CONTINENT OF LOGISTICS
How is it that logistics and supply chain management can make such a difference? After all, isn't logistics "merely" a company's management of material, product, and information flows in the supply chain? Those who work in the field of logistics recognize the difficulties associated with getting the right product to the right place at the right time in the right quantity and condition at the lowest possible cost. It involves not only a lot of heavy lifting, but also deep thought and decisive action to provide promised service at the lowest cost. Back in 1962, renowned management guru Peter Drucker once referred to logistics as an untapped source of innovation and opportunity, calling it the economy's "dark continent." Four decades later, logistics management is only somewhat better understood among business practitioners and the general public. It is regarded as an afterthought among many companies, a necessary cost of doing business that has little viable input on corporate strategy. Yet, ask the CEOs of the leading companies noted above what role logistics plays in their enterprises. Excellence in logistics provision not only supports the missions of these companies but, in fact, also serves as a focal point in their very competitiveness. Take Wal-Mart, for instance. How well does its model of "every day low pricing" stand in the absence of cross-docking and economies of scale in transportation, keeping costs below those of rival retailers? And, at the end of the day, what good are "every day low prices" if the products are not on the shelf in sufficient quantity and quality? So, it is not only the low prices but also the exceptional service that differentiates Wal-Mart from rivals.
Too often, companies fail to deliver on the implicit promises that are made to customers. What is worse is when an explicit promise is left unfulfilled. Consider the promotional advertisements and fliers that appear in newspapers almost daily. What happens when the retailer promoting the product depletes its inventory? If the retailer is lucky, customers facing the empty shelf will accept a rain check or the promise to accept the order at a later date when inventory is replenished. However, in many instances, the customer knows that he or she can take the promotional flier to a rival store that will honor the deal offered by the first retailer. What might such an experience mean for the future relationship between the retailer and that particular customer? For one thing, the retailer is likely to order greater quantities of product in the future to overcome the stockout situation. However, the customer may not return in the future, knowing that a rival store down the street will honor the deals promoted by the first store. In this instance, the second retailer actually benefits from the promotions of the first store. Meanwhile, what happens when the consumer in question tells a few people about this experience? The impact of that original stockout can be amplified dramatically as others consider similar action in the future, bypassing the promotion-happy retailer in favor of the customer-responsive one. So, simply adding inventory is not the answer but, in fact, is a big step backwards.
Wal-Mart enjoys fewer product stockouts than its competitors not because of higher inventories but because of better inventory management achieved through high-frequency replenishment. Order cycle times (the time from order placement to order delivery) are forty-eight hours or less for U.S. stores, allowing store shelves to be replenished as much as four times faster than competitors. Not only does frequent replenishment of stores support in-stock objectives, but it also provides for "fresher" products. Like availability, the timeliness of product delivery have become a key differentiator in many markets. "Freshness" is obviously important for perishable consumer products like fruits, vegetables, dairy products, baked goods, and infant formula, but now it is also commonly advertised as important for products like soft drinks and beer. The waste of obsolete inventory is created when supplies are left unclaimed at the time of their expiration.
(Continues…)
Excerpted from "Lean Six Sigma Logistics"
by .
Copyright © 2005 J. Ross Publishing, Inc..
Excerpted by permission of J. Ross Publishing, Inc..
All rights reserved. No part of this excerpt may be reproduced or reprinted without permission in writing from the publisher.
Excerpts are provided by Dial-A-Book Inc. solely for the personal use of visitors to this web site.
Table of Contents
Preface | xi | |
Acknowledgments | xiii | |
About the Authors | xv | |
Web Added Value | xvii | |
Section 1 | Lean Six Sigma Logistics: Why Bother? | |
Chapter 1 | What Is Lean Six Sigma Logistics? | 3 |
What Is Logistics? | 4 | |
What Is Lean? | 4 | |
Lean and the Logistician | 4 | |
What Is Six Sigma? | 5 | |
Six Sigma and the Logistician | 5 | |
What Is Lean Six Sigma Logistics? | 6 | |
The Logistics Bridge Model | 7 | |
Chapter 2 | The Importance of Logistics and Supply Chain Management | 9 |
Discovering the Dark Continent of Logistics | 9 | |
This Thing Called "Supply Chain Management" | 11 | |
The Logistics Wastes | 14 | |
Section 2 | The Logistics Wastes | |
Chapter 3 | The Waste of Inventory | 19 |
Logistics and Inventory Management | 19 | |
The Temptation of Inventory | 20 | |
The Costs of Holding Inventory | 22 | |
Chapter 4 | The Waste of Transportation | 27 |
Logistics and Transportation Management | 27 | |
Transportation and Logistics Trade-offs | 29 | |
Transportation Carrier Relationships | 31 | |
Minimizing the Day-to-Day Wastes in Transportation | 32 | |
Chapter 5 | The Waste of Space and Facilities | 35 |
Logistics and Warehousing | 35 | |
How Many Facilities? How Much Space? | 36 | |
Are Advanced Technologies a Cure or Merely a Crutch? | 37 | |
Chapter 6 | The Waste of Time | 39 |
Logistics and Time Wastes | 39 | |
Order Transmission | 39 | |
Order Processing | 41 | |
Order Filling | 42 | |
Order Staging and Verification | 43 | |
Order Shipping and Delivery | 44 | |
Chapter 7 | The Waste of Packaging | 47 |
Logistics and Product Packaging | 47 | |
Packaging as a Source of Waste | 48 | |
Packaging as a Waste | 49 | |
Packaging as a Visual Control | 50 | |
Chapter 8 | The Waste of Administration | 51 |
Logistics and Administration | 51 | |
Administration as Help and Hindrance | 52 | |
Technology and Administration | 52 | |
Chapter 9 | The Waste of Knowledge | 55 |
Logistics and Knowledge | 55 | |
Cultivating Knowledge | 56 | |
Managing the Flow of Knowledge | 57 | |
The River of Wastes | 59 | |
Section 3 | The Logistics Bridge Model | |
Chapter 10 | A Tour of the Bridge | 65 |
History of Lean Six Sigma Logistics | 66 | |
The Importance of the Logistics Bridge Model | 66 | |
The CEO's Perspective | 67 | |
The Implementer's Perspective | 69 | |
The Logistics Bridge Model: Getting Started | 70 | |
Chapter 11 | Logistics Flow: Asset Flow | 71 |
People Flow | 72 | |
The People "Perfect Order" | 73 | |
Organizing People | 73 | |
Bridging the People Gap | 74 | |
Inventory Flow | 75 | |
Understanding Safety Stock | 76 | |
Inventory Management | 77 | |
Starting with the Systems Approach | 77 | |
Inventory and Cause and Effect | 78 | |
Inventory Management Fundamentals | 79 | |
Fixed Resources Flow | 80 | |
Identifying and Mapping Fixed Resources | 81 | |
Questioning the Need | 82 | |
Vision of Excellence and Fixed Resource Flow | 83 | |
Chapter 12 | Flow: Information Flow | 85 |
Data Flow | 86 | |
Historical Data | 86 | |
Event and Real-Time Data | 87 | |
Future and Deterministic Data | 87 | |
Data Excellence | 89 | |
Knowledge Flow | 89 | |
Continuous Improvement and Knowledge Flow | 90 | |
Standardized Work and Knowledge Sharing | 91 | |
Getting Knowledge to Flow | 92 | |
Communication Flow | 93 | |
Strategic Communication | 93 | |
Hoshin Planning | 94 | |
Operational Communication | 95 | |
Chapter 13 | Flow: Financial Flow | 97 |
Income Statement Flow | 98 | |
Logistics Activities and Hidden Operating Costs | 99 | |
Logistics Costs Flow Across the Organization | 100 | |
Inventory Carrying Costs and the Income Statement | 101 | |
Vision of Excellence and the Income Statement | 102 | |
Balance Sheet Flow | 103 | |
Inventory as a Current Asset | 104 | |
Inventory Turns and the Balance Sheet | 105 | |
The Balance Sheet and Business Strategy | 106 | |
Flexibility | 106 | |
Visibility | 107 | |
Cash Flow | 107 | |
Cash Flow Drivers | 108 | |
Accounts Payable and Cash | 108 | |
Accounts Receivable and Cash | 110 | |
Revenue Growth and Cash | 110 | |
Gross Margin and Cash Flow | 111 | |
Selling, General, and Administrative Expense and Cash Flow | 111 | |
Capital Expenditure and Cash Flow | 112 | |
Inventory and Cash Flow | 113 | |
Vision of Excellence and Cash Flow | 113 | |
Chapter 14 | Capability: Predictability | 115 |
Organization | 116 | |
Highlighting Waste and Creating Visibility | 117 | |
Standardized Operations and Setting Priorities | 118 | |
The Organized Workplace: Clutter, Complexity, and Quality | 119 | |
Measurement and the Organized Workplace | 119 | |
Coordination | 120 | |
Coordination and Value Stream Mapping | 121 | |
Coordination and Detailed Planning | 122 | |
Coordination and Measurement | 124 | |
Complexity | 124 | |
Complexity of Products | 125 | |
Complexity of Processes | 126 | |
Chapter 15 | Capability: Stability | 129 |
Standardization | 130 | |
The Key Aspects of Standardization | 130 | |
Standardization and Continuous Improvement | 131 | |
Flexibility | 132 | |
Developing Flexibility and Back to Basics | 133 | |
Flexibility and Lead Time | 134 | |
Logistics Infrastructure Flexibility | 135 | |
Planned Network Design and Visibility | 136 | |
Control | 137 | |
Today's Capability Is the System's Capability | 138 | |
Common and Special Cause Variation | 139 | |
Chapter 16 | Capability: Visibility | 141 |
Understandability | 142 | |
Beginning to Understand | 143 | |
Channel Partners and Their Important Role | 143 | |
Opportunities and the Moment of Truth | 144 | |
Measurability | 145 | |
Voice of the Customer | 146 | |
Creating Internal Measures of Meaning | 148 | |
Actionability | 149 | |
Chapter 17 | Discipline: Collaboration | 153 |
Teamwork | 154 | |
Processes and Knowing the Customer | 155 | |
Building Teams | 156 | |
Complementary Skills and Opposing Views | 156 | |
Natural Stages of Team Development | 157 | |
Strategic Sourcing | 158 | |
Raw Material Suppliers | 159 | |
Standardization, Complexity, and Dual Sourcing | 160 | |
Beware the Term "Partnership" | 160 | |
Collaboration and Logistics Services | 161 | |
Third-Party Logistics | 162 | |
Developing a Lean Third-Party Logistics Relationship | 163 | |
Project Management | 165 | |
Project Management: The Basics | 166 | |
Meeting Agenda (Compass) | 167 | |
Storyboard | 167 | |
Gantt Chart | 168 | |
Failure Mode and Effects Analysis | 169 | |
Chapter 18 | Discipline: Systems Optimization | 173 |
Total Cost | 174 | |
Explicit and Implicit Costs | 174 | |
Horizontal Integration | 177 | |
Perceived Difficulty and System Constraints | 179 | |
Compensation and Incentive Programs | 179 | |
Teamwork, Imperfection, and Defensive Behavior | 180 | |
Breaking Down the Walls | 181 | |
Vertical Integration | 181 | |
From Customer to Supplier | 182 | |
Vertical Integration and Information | 182 | |
Variability, Leveled Flow, and Vertical Integration | 183 | |
Chapter 19 | Discipline: Waste Elimination | 185 |
Quality at the Source | 186 | |
The Benefits of Quality at the Source | 187 | |
Logistics and Quality at the Source | 189 | |
Continuous Improvement | 190 | |
Continuous Improvement: The Bare Facts | 190 | |
The Challenges of Continuous Improvement Implementation | 192 | |
Bridging the Gap | 193 | |
Getting People Trained | 194 | |
Execution | 195 | |
Acting as Lean Six Sigma Logistics Leaders | 195 | |
Section 4 | Building the Bridge: Lean Six Sigma Logistics Tools | |
Chapter 20 | Strategy and Planning Tools | 201 |
Surveying the Tool Kit | 201 | |
Voice of the Customer | 202 | |
Voice of the Business | 204 | |
Value Stream Mapping | 206 | |
Pareto Analysis and ABC Classification | 208 | |
The XY Matrix | 211 | |
Chapter 21 | Problem-Solving Tools | 213 |
DMAIC (Define-Measure-Analyze-Improve-Control) | 213 | |
Define | 214 | |
Measure | 214 | |
Analyze | 215 | |
Improve | 216 | |
Control | 217 | |
Causal Analysis Tools | 218 | |
Brainstorming | 218 | |
Cause-and-Effect Diagrams | 219 | |
Five-Why Analysis | 220 | |
Design of Experiments | 222 | |
Inferential Statistics | 223 | |
Chapter 22 | Operational Tools | 227 |
Flow Concepts | 227 | |
Just-in-Time and the Pull System | 227 | |
Lead-Time Management, Speed, and Flexibility | 229 | |
Leveled Flow | 230 | |
Frequency and Lot Size | 232 | |
Organization Concepts | 232 | |
Standardized Work Plan | 233 | |
The SIMPOC Model | 233 | |
5S Organization and Visual Control | 234 | |
Red Tag Initiatives | 235 | |
Poka-Yoke | 236 | |
Chapter 23 | Measurement Tools | 237 |
Data Collection Plan | 237 | |
Process Capability | 238 | |
Defects per Million Opportunities | 241 | |
Sigma Calculations | 242 | |
Conventional Measures of Logistics Performance | 245 | |
Total Cost Analysis | 246 | |
Chapter 24 | Case Study: GoldSMART Products, Inc. | 249 |
Lean Six Sigma Logistics: A Real-World Story | 249 | |
GoldSMART Products, Inc.: A Cast in Lean Six Sigma Logistics | 250 | |
The Calm Before the Storm | 250 | |
The Approach of Ominous Clouds | 251 | |
In the Eye of the Storm | 252 | |
Riding Out the Storm | 255 | |
Seeing Daylight Again | 260 | |
Chapter 25 | Summary and Conclusion | 267 |
Index | 271 |