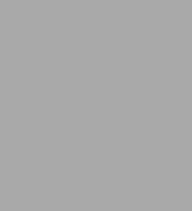
World Class Master Scheduling: Best Practices and Lean Six Sigma Continuous Improvement
272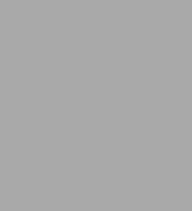
World Class Master Scheduling: Best Practices and Lean Six Sigma Continuous Improvement
272eBook
Related collections and offers
Overview
Product Details
ISBN-13: | 9781604276305 |
---|---|
Publisher: | Ross, J. Publishing, Incorporated |
Publication date: | 03/01/2006 |
Sold by: | Barnes & Noble |
Format: | eBook |
Pages: | 272 |
File size: | 5 MB |
About the Author
Read an Excerpt
CHAPTER 1
UNDERSTANDING THE MASTER SCHEDULE
Master scheduling is probably one of the most important and yet least appreciated processes to control costs in business today. Top management ignores it, middle managers take it for granted, and line management often unknowingly subverts the integrity of the schedule by causing unnecessary changes to it. In contrast, high-performance businesses treat the master scheduling process as the heartbeat of the supply chain and utilize best practices in this space to minimize cost and efficiency and to maximize customer service. Techniques in master scheduling cover lots of business process territory, including links to demand planning, financial planning, inventory strategy, customer service, and rules of engagement.
Topics covered in the chapters to come include what good process would look like, how top managers interact with this driver of requirements called master scheduling, and how to implement a high-performance master production scheduling process in your business. Master scheduling is a passion with some manufacturing professionals. The objective of this book is to capture some of that passion. It is a pleasure to put into writing the power of one process that can help improve numerous processes within both manufacturing and distribution companies. Observation of hundreds of businesses using both good and bad process has helped with the conclusions. The logical place to start this discussion is by defining the master schedule.
THE MASTER SCHEDULE
The master schedule in an enterprise resource planning (ERP) business system is the detailed driver of requirements in manufacturing companies. This accounting of known and unknown requirements is a company's determination of firm and forecasted signals empowered to drive procurement and manufacturing requirements. This schedule can dictate amount of inventory and timing of the procurement and can even influence lot size or order size. This is an extremely important set of requirements and makes the disciplines and rules governing the schedule very important to most businesses concerned about cost, efficiency, and customer service.
In high-performance businesses, top management engages in a planning process referred to as the sales and operations planning (S&OP) process. It should be noted that some companies refer to this as the SIOP (sales, inventory, and operations planning) process. In this book, it will be referred to as the S&OP process. The master scheduler plays a critical role in the development of the spreadsheets and performance metrics evaluated in S&OP. Probably even more important is the requirement in high-performance companies that the master schedule link directly with this top management planning process. In the S&OP planning process, the CEO, president, and vice presidents of both demand and supply engage in risk management within the planning horizon of 12 rolling months. No one understands the risks of creating the right product using only forecasts for the demand signals better than the master scheduler.
In a high-performance ERP organization, sometimes referred to as a Class A ERP organization, the two most influential positions are the plant manager and, you guessed it, the master scheduler. The master schedule not only defines the activities required to meet the top management S&OP but also dictates the requirements from customer demand. This already sounds like quite a job and it is. Figure 1.1 depicts the relationship of the master schedule to the rest of the ERP process flow. Top management planning decisions feed into the master production schedule (MPS) and drive emphasis and create the forecasted demand. The MPS in turn feeds back vital data concerning customer activity and coordinates the interaction of the two inputs. This feedback affects the next S&OP cycle.
The MPS is the detailed schedule that resides within the ERP business system that drives inventory strategy, supply chain accountability, inventory levels, customer service, and machine and capacity utilization. The main categories that are driven fall into two areas: known requirements and unknown requirements. This may seem too simple to even state, but it is the essence of understanding the master scheduling process.
The darker shaded areas in Figure 1.2 represent the known requirements. Where the darker shaded areas appear, there are normally many detailed stockkeeping unit (SKU) level requirements driven from either firm orders from customers or firm orders from planned requirements. In the case illustrated in Figure 1.2, if each rectangular shaded area represents one day, the conclusion from this figure is that backlogged orders only go out about six days, and even then capacity is not full for the six days. Only Monday and Tuesday are close to being filled (Tuesday might even be a little over capacity per the diagram).
This is the basic structure of the MPS in its simplest form. As this book progresses, best practices examples of how high-performance companies deal with the realities of business will be used. The first step is to tie inventory strategy tightly to this schedule, in order to understand the impact. Inventory strategy must be well understood to execute master scheduling well.
INVENTORY STRATEGY
Inventory strategy (sometimes referred to as manufacturing strategy) is the buffer inventory plan for each product family in a planning process. The buffer inventory plan is the plan for where in the business the inventory will be buffered, if at all. Sometimes buffer will be in raw material, sometimes it may be in finished goods, and sometimes it will not exist at all except in the forecasted plan. If the flexibility and responsiveness within the supply chain match the need, there is no reason to have buffer. Very few manufacturing plants, however, meet the criteria completely to go buffer-free. In those companies without buffer, the plan has to be decided based on product family process capability. Figure 1.3 gives a sense of how these strategies fit together. Keep in mind that most companies do not engage in just one of the strategies. It is most common for companies to have several inventory strategies, with separate pricing strategies, rules of engagement, and service requirements for each product family.
It is necessary to review inventory strategy as you set up the MPS because the entire manufacturing planning world revolves around these strategies. Although many companies do not acknowledge this thinking, all companies have to make these decisions. Too many organizations will say they use one type of inventory strategy and actually do something totally different. Still others do not recognize that their strategies differ from one product family or line to another.
It is common for those in top management to believe that their business methodology is one inventory strategy. It is just as common for them to get involved with the process and find that they do not really understand what is going on in the detail planning process. Maybe it is unfair to be so critical, but most of the time, especially in so-called "make-to-order" environments, there are buffers distributed in various places within the process. These have to be recognized and understood in order to have real control over the manufacturing process. After all, these buffers are probably there for a reason. It is paramount to know what is in place and for what reason it was initially positioned. It could very well make a difference in planning methodology or inventory strategy overall. It certainly affects customer service and profitability.
With the proper acknowledgment of actual buffer strategy, management is more in control of the risks taken and no one is surprised by inventory that by design is built into the process. Inventory strategies change the method used for master scheduling suppliers and components. Inventory strategy is smart policy, but the rules agreed to internally — what products, how much, and when — need to be understood by all the players. Many times, finished goods inventory is scrutinized, as it is very visible and better understood. Sometimes inventory does not need to be built in advance of the customer order. This is the whole point of inventory strategy. Lean philosophy has gotten a lot of press recently and deservedly so, but inventory strategy has been around for years and covers some common ground.
It is important to realize that acknowledging rules of engagement and utilizing good inventory strategy is not a methodology designed to say no to the customer. Inventory strategy is acknowledged so that everyone in the business has the same shared goals. Its role is to acknowledge and understand what it costs when we say yes to the customer.
The acknowledgment of inventory strategy is not difficult to determine. In fact, it is dictated to you if the background data are understood. When lead time requirements from the customer are shorter than the total accumulative lead time of the supply chain and manufacturing process, some of the process must be planned. That means some of the lead time in the process is committed to via forecasted requirements. Inventory strategy should be mapped out, agreed to by both demand- and supply-side management, and rules of engagement documented. When the market practices or strategies change, high-performance organizations regularly update the handshake between the parties. Again, the objective is lowest cost with highest service. To acknowledge the realities of inventory strategy is to allow for the most cost-effective and highest customer service processing of orders.
Master scheduling different inventory strategies will make a difference in scheduling approach and what techniques will be used. That opens up the discussion on the definitions of product families.
PRODUCT FAMILY
Through lots of evolution within the ERP process, companies have determined that there is an optimum level of detail for planning at the top management level. This level of detail generically is referred to as product family. If product family has a specific meaning to you in your environment, do not get too involved yet trying to apply your definition. Product family can be defined differently in every business. The definition used in this book will be a common one, so set aside your definition for now. The good news is that you can call what in this book will be referred to as "product family" anything you want as long as everyone in your business understands it the same way.
As you can see from Figure 1.4, there is an optimum level of detail for the product family designation. This requires experimentation. It is difficult at best to try to define a generic formula to pinpoint the correct configuration that would work for all manufacturing companies. It just is not that simple. It is also common for a company to revise product families several times before settling on consistent groupings. Finance, forecasting, and operations planning all must share these common planning groupings. It is this insistence that allows the real power of the S&OP process to work and the master schedule to be most effective.
BILL OF MATERIAL
The SKU level to be scheduled by master scheduling is determined by the bill of material (BOM). The BOM is the recipe for how the product is put together and what components are required. The BOM records are one of the most important assets of an organization. They not only influence the manufacturing process but also impact the planning process in several ways. Generally, the more levels in the BOM, the greater the lead time and the more complicated the inventory strategy requirement will be.
BOMs do not have to be just the recipe for the finished product. They can be used for planning the unknown in master scheduling. Planning BOMs, as these special bills are called, are always used in high-performance operations. These specialized records may not always be called planning BOMs, but that is what they are. Planning BOMs drive components to be positioned in anticipation of a customer order. Good master scheduling always utilizes planning BOMs. Examples of their use might include engines and transmissions for auto manufacturing or resin for plastics molding. Complex subassemblies require signals to be in position prior to receipt of the real customer order. The use of planning BOMs will be discussed further in Chapter 5.
CAPACITY PLANNING IN THE MPS PROCESS
There are two types of capacity related to this discussion: demonstrated capacity and theoretical capacity. It is extremely important to distinguish between the two. In many businesses, highly energetic people with the best of intentions think that a carrot has to be out in front of the donkey's nose for the cart to be drawn at top speed. This may be true in lower performing plants, but not in high-performance ERP facilities.
At one facility, promises were made to corporate management that levels of production would reach new record volumes. Sales were surprisingly high, which was exactly what management wanted to hear. All it really did was buy time between the monthly reviews and create a false sense of security. The underpinnings were not there to actually carry out this promise. As will be demonstrated throughout this book, there is no place in master scheduling for overstated requirements. The most important job a master scheduler can do is keep the schedule tight and realistic. This is not possible without an understanding of demonstrated capacity. Capacity is a major concern for the master scheduler, maybe the most important factor governing the scheduling process. A high-performance master scheduler always uses demonstrated capacity and is not easily fooled by opinions and emotions not backed by data or facts.
Returning to our example, the master scheduler really suspected the truth about the capacity but went along with management. He did not feel it was his place to raise a red flag. He was very wrong! Additionally, unless demonstrated capacity is very consistent and repeatable, there is an argument to be made that some small amount of buffer time should be also considered. At Frigidaire's dishwasher plant in Kinston, North Carolina, this is called buffer "overspeed." Most high-performance facilities schedule some buffer time. No capacity is lost because if the schedule is on time, work is brought up from the next period. If this all sounds a bit confusing, it will be clarified as the story progresses.
In the previous depiction in Figure 1.2, "capacity" was shown at the top of the schedule. In Figure 1.5, level A is an imaginary level of capacity, just above the filled bucket value of capacity scheduled for consumption. The inference from the diagram is that the master scheduler should not schedule to the maximum demonstrated capacity all the time. To do so is to fail at master scheduling. Demonstrated capacity is what the process can generally yield. It does not mean that the process will always deliver at that level. Good master schedulers take their responsibilities very seriously. When they miss schedules, it is a reflection on their accuracy and performance. Class A master scheduling requires that schedules are hit 95+% of the time. To accomplish this, demonstrated capacity must be well understood and schedules continually synchronized with reality. In high-performance organizations, this must happen at least once a week. It is common for this to be done daily or even hourly, although if a good job is done initially, the frequency should be minimized. In high-performance companies, synchronizing the schedule is not that difficult; often only small schedule tweaks are required. This practice should not be compromised. It also requires recognition of known and unknown requirements (see Figure 1.6). Any consideration of an alternative practice is generally not in accordance with good master scheduling process.
While discussing reality, let's talk about customer orders. In most businesses, customer behavior generally is not predictable. Orders do not come in at the same rate every day. Some days orders are heavy, and other days orders are light. If this sounds familiar, you are not alone. Customers do not always work from a level schedule. They are reacting to their customers as well. Ultimately, it is the customers at the retail level that drive the whole supply chain. Normal process variation might look like Figure 1.7.
In reality, this is probably how the orders come into your order entry process. No matter where you are in the food chain, consumer spending affects demand, and consumers can be finicky, to say the least. This is not how most companies want to run their operation on the supply side. For that reason, some load smoothing is done regularly. This smoothing is initially done in the operations planning process, but the real schedule leveling takes place at the MPS. This is where planned orders meet firm customer orders.
(Continues…)
Excerpted from "World Class Master Scheduling"
by .
Copyright © 2006 J. Ross Publishing, Inc..
Excerpted by permission of J. Ross Publishing, Inc..
All rights reserved. No part of this excerpt may be reproduced or reprinted without permission in writing from the publisher.
Excerpts are provided by Dial-A-Book Inc. solely for the personal use of visitors to this web site.
Table of Contents
Preface,
Acknowledgments,
The Author,
About APICS,
Web Added Value,
Chapter 1: Understanding the Master Schedule,
Chapter 2: Utilizing Inventory Strategy,
Chapter 3: Master Production Schedule Integration with Enterprise Resource Planning,
Chapter 4: Demand Planning Influences,
Chapter 5: The Details Behind Master Scheduling,
Chapter 6: Order Management,
Chapter 7: Roles of the Players in the Master Production Scheduling Process,
Chapter 8: Sales and Operations Planning,
Chapter 9: Measuring the Master Production Scheduling Process,
Chapter 10: Management Systems,
Chapter 11: Integration with Material Requirements Planning,
Chapter 12: Forecast Requirements,
Chapter 13: Software Tools,
Chapter 14: Master Scheduler Job Description,
Chapter 15: Class A ERP Business Model and Performance,
Chapter 16: Integrating the Master Production Schedule with Lean and Six Sigma,
Chapter 17: Discussions with the "Masters",
Glossary of Terms,
Checklist for High-Performance Master Scheduling,